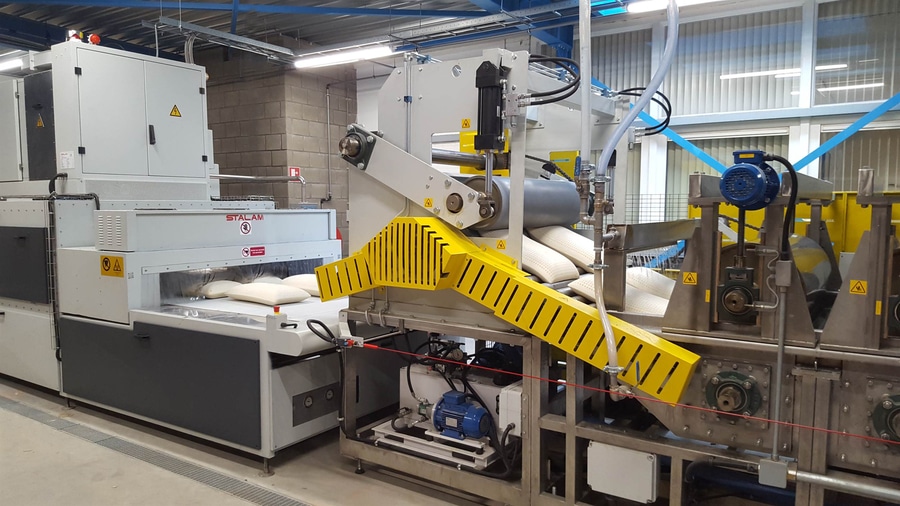
Voir la traduction automatique
Ceci est une traduction automatique. Pour voir le texte original en anglais cliquez ici
#Tendances produits
Le processus Dunlop : comment améliorer l'efficacité et la qualité de la production de mousse de latex ?
La technologie des radiofréquences permet de surmonter les principaux inconvénients du procédé Dunlop traditionnel car elle ne repose pas sur le transfert de chaleur...
Le processus Dunlop : comment améliorer l'efficacité et la qualité de la production de mousse de latex ?
Le latex naturel est un composé liquide récolté sur l'arbre à caoutchouc (Hevea Brasiliensis) dont les principales cultures sont situées en Asie du Sud-Est. Une fois récolté sur l'arbre, le liquide est mélangé à de l'ammoniac et à du TMTD/ZnO pour mieux préserver ses propriétés. Ce latex LA standardisé (latex à faible teneur en ammoniac) est utilisé comme matière première pour produire des ballons, des gants, des articles sanitaires, etc. mais aussi des articles en mousse de latex tels que des noyaux de matelas et des oreillers
Le processus DUNLOP : les origines
En 1887, John Boyd Dunlop (1840-1921), né en Écosse, invente le premier pneu gonflable pour le tricycle de son fils, basé sur la vulcanisation thermique du caoutchouc naturel, puis le fait breveter le 7 décembre 1888. Mais deux ans plus tard, son brevet a été officiellement invalidé car un autre inventeur écossais, Robert William Thomson (1822-1873), avait déjà breveté la même technologie en Grande-Bretagne, en France (1846) et aux États-Unis (1847). Néanmoins, le procédé a été nommé d'après Dunlop et est devenu le principal système de vulcanisation des produits en caoutchouc et en mousse de latex.
Les technologies deviennent des standards industriels : Méthodes DUNLOP et TALALAY
Il existe actuellement deux méthodes standard pour la production d'articles en mousse de latex : les procédés DUNLOP et TALALAY. Inventé à la fin des années 1940, le procédé TALALAY est plus long et plus complexe que le procédé DUNLOP. Ce système n'est utilisé que par quelques producteurs dans le monde et ne représente qu'une petite part de marché. Les matières premières de base des deux systèmes sont le latex naturel (NL) ou le latex SBR (styrène-butadiène-caoutchouc) ou des mélanges des deux.
La méthode DUNLOP
Si l'on utilise du latex naturel pur, le "lait" de latex est mélangé aux produits chimiques nécessaires. Une fois maturé, le composé est moussé à l'aide d'un mélangeur mécanique (le latex SBR peut être moussé sans maturation) et versé dans des moules métalliques. Un agent gélifiant est ajouté au mélange, afin de générer une réaction rapide qui stabilise la structure de la mousse. Les moules sont ensuite placés dans un four ou un tunnel à vapeur pour vulcaniser les noyaux. Comme les produits en mousse sont de bons isolants thermiques, les moules sont équipés d'un grand nombre de broches pour transférer la chaleur dans la mousse elle-même. Une fois vulcanisé, le noyau de l'oreiller ou du matelas est décapé, lavé, séché et enfin prêt à être vendu.
La méthode TALALAY
Dans le processus TALALAY, trois autres phases sont nécessaires avant l'étape de vulcanisation :
- le moule n'est rempli qu'à 40-60%. Ensuite, il est fermé et de l'air est pompé pour faire gonfler la mousse afin de remplir tout le volume du moule ;
- la mousse est congelée à -20°C pour stabiliser la structure ;
- Le CO2 est injecté par une valve dans le moule pour gélifier la mousse.
Le reste du processus suit les mêmes étapes que le processus DUNLOP, c'est-à-dire la vulcanisation, le décapage, le lavage et le séchage.
Le procédé de vulcanisation traditionnel de Dunlop utilise la vapeur comme moyen de chauffage pour activer les réactions de réticulation des chaînes de polymères. La mousse, qui contient de nombreuses petites bulles d'air, est par nature un mauvais conducteur thermique. Par conséquent, laisser la chaleur s'infiltrer dans le noyau d'un matelas épais ou dans les moules d'un oreiller est un processus lent et inefficace. Des moules en métal lourd et coûteux, équipés de nombreuses broches métalliques, sont en fait utilisés pour tenter d'accélérer le processus, mais celui-ci reste néanmoins consommateur de temps et d'énergie.
Au cours des décennies, certains produits chimiques ont été remplacés pour améliorer le processus global, mais le processus de base, c'est-à-dire la réticulation des molécules de caoutchouc avec du soufre, n'a pas changé jusqu'à présent, tout comme les inconvénients typiques des méthodes conventionnelles de transfert de chaleur.
Processus lent, pertes d'énergie élevées. Y a-t-il une solution ? Oui, il y en a une !
Le "nouveau processus Dunlop
La technologie de la radiofréquence permet de surmonter les principaux inconvénients du procédé Dunlop traditionnel car elle ne repose pas sur le transfert de chaleur, de sorte que même les articles en mousse de latex épais, façonnés et denses (noyaux de matelas, oreillers anatomiques, etc.) peuvent être chauffés et vulcanisés rapidement : en fait, la radiofréquence est instantanément absorbée en quantité contrôlée (ajustée selon les besoins de la machine elle-même) par l'eau contenue dans la mousse, uniformément dans tout son volume. Ainsi, le chauffage de la mousse et sa vulcanisation complète ne prennent que quelques minutes, au centre comme à la surface.
Les machines de vulcanisation RF sont donc beaucoup plus petites (plus courtes) que les carrousels ou tunnels conventionnels travaillant à la vapeur ayant le même débit horaire, et la consommation d'énergie peut être réduite jusqu'à 50 %.
Les moules peuvent être fabriqués en matériaux composites légers et peu coûteux qui permettent une réduction de poids de plus de 60 % par rapport aux moules métalliques traditionnels : la masse réduite du moule contribue de manière significative à la diminution de la consommation d'énergie. De plus, les matériaux de moule appropriés permettent un démoulage facile et rapide des articles vulcanisés. Enfin, la conception du moule est plus flexible, n'étant pas liée à la présence de broches.
Il convient également de mentionner que la technologie des radiofréquences peut être utilisée avec succès même pour la production de plaques de mousse de latex continues (LPC, sur-matelas ou même un véritable matelas) jusqu'à 12 cm d'épaisseur et plus, dans un délai beaucoup plus court et en réduisant considérablement la consommation d'énergie, étant donné que la vulcanisation traditionnelle à la vapeur de plaques de plus de 5 cm d'épaisseur est une tâche presque impossible en raison du manque de pénétration de la chaleur en l'absence de tiges métalliques.
Qu'en est-il du séchage de la mousse de latex après vulcanisation, lavage et pressage ?
Les mêmes raisons techniques qui rendent la radiofréquence plus efficace et plus rentable que les méthodes traditionnelles de vulcanisation à la vapeur peuvent être appliquées à la phase finale de séchage des produits en mousse de latex après lavage et pressage.
Les avantages de l'utilisation de séchoirs à radiofréquence plutôt que de séchoirs chauffés à la vapeur peuvent être résumés comme suit :
séchage rapide et uniforme : environ 20 minutes suffisent pour sécher même les noyaux de matelas épais et denses dont la teneur en humidité résiduelle est inférieure à 1 %, sans aucune tache humide ; les produits façonnés comme les oreillers et les sièges anatomiques sèchent également de manière parfaitement uniforme dans les parties plus épaisses comme dans les parties plus fines ;
pas de jaunissement de la surface du produit, en raison de la basse température dans le tunnel de séchage (la radiofréquence chauffe le noyau du produit et non sa surface extérieure) ;
un temps de conditionnement court, de sorte que le produit peut être emballé pour être expédié rapidement après le séchage sans risque de moulage sur le chemin des clients ;
une réduction significative de l'encombrement des équipements de séchage, grâce à la brièveté du processus ;
processus en ligne économe en énergie, réduction des coûts de séchage et de manutention des produits ;
une empreinte carbone réduite, grâce à la technologie électrothermique.
On peut donc dire que la technologie des radiofréquences est une véritable révolution dans l'industrie de la mousse de latex, tant dans la phase de vulcanisation que dans celle du séchage, offrant aux producteurs de mousse de latex d'énormes avantages en termes d'efficacité de la production, de réduction des coûts et de qualité des produits.