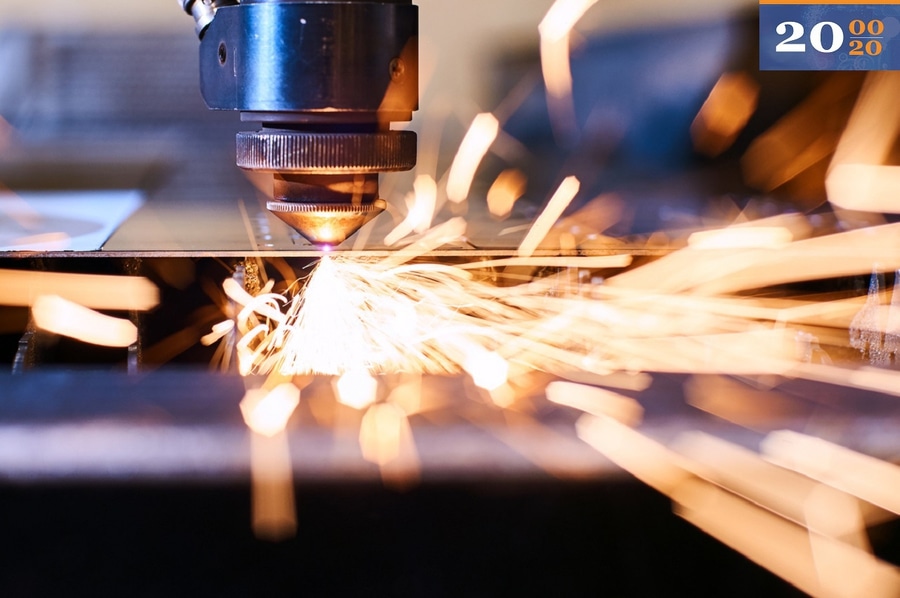
Voir la traduction automatique
Ceci est une traduction automatique. Pour voir le texte original en anglais cliquez ici
#Actualités du secteur
CECIMO : "La grande révolution pour l'industrie de la machine-outil est la numérisation
À l'occasion du 20e anniversaire de notre éditeur, la société de sourcing industriel DirectIndustry, nous célébrons 20 ans d'innovations industrielles en donnant la parole aux acteurs qui ont donné vie à ces innovations.
Dans cette interview, nous nous concentrons sur les machines-outils. Filip GEERTS, directeur général de CECIMO - Association européenne des industries de la machine-outil et des technologies de fabrication connexes, nous fait part de ses réflexions sur 20 ans d'innovations dans le domaine de la machine-outil.
20 ans de MACHINES-OUTILS avec le CECIMO
Le Cecimo est une organisation européenne de coordination des fabricants de machines-outils, composée de 15 associations nationales et représentant quelque 1 300 entreprises industrielles en Europe. L'organisation se concentre sur la création de conditions économiques idéales pour l'industrie des machines-outils, condition préalable à l'innovation, dans le but d'aider les fabricants européens de machines-outils à renforcer leur position de leader mondial.
Le magazine DirectIndustry : Quelle a été la grande révolution des machines-outils au cours des 20 dernières années ?
Filip GEERTS : La GRANDE révolution de ces 20 dernières années est la numérisation. La numérisation (y compris l'intelligence artificielle) génère de nouvelles opportunités et transforme de plus en plus tous les segments de la fabrication, de la conception à la maintenance. C'est un moteur de l'optimisation des activités et de l'efficacité énergétique. La numérisation conduit également au développement de nouveaux modèles commerciaux et de nouveaux services basés sur les données, par exemple la maintenance prédictive
Le magazine DirectIndustry : Les machines-outils sont une industrie qui évolue généralement lentement. Mais il semble qu'en 20 ans, les choses ont beaucoup changé. Qu'en pensez-vous ?
F.G. : En effet, les choses ont beaucoup changé en 20 ans. Pour donner un exemple, l'utilisation de l'Additive Manufacturing (AM) se développe dans de nombreux secteurs, mais son utilisation n'est pas encore très répandue. Les technologies additives présentent un grand potentiel et de nombreux avantages, par exemple pour la réduction du poids des composants, la capacité à produire des pièces complexes et la personnalisation. Néanmoins, dans de nombreux cas, une sorte de post-traitement soustractif est nécessaire avant de finaliser la pièce. L'AM ne va pas remplacer la fabrication soustractive, mais il sera nécessaire de profiter des avantages des procédés additifs et des machines-outils traditionnelles, ainsi que de les intégrer dans une chaîne de processus ou dans des machines hybrides.
Deux autres tendances sont la robotique et l'automatisation qui conduisent la fabrication vers ce qu'on appelle les "usines du futur". Dans l'atelier, les robots peuvent être intégrés au processus de production tout en laissant les activités d'usinage et de découpe à la machine-outil. Ils sont utiles pour aider les techniciens dans des tâches telles que la manutention et peuvent accroître la productivité de l'ensemble de l'atelier. En tant qu'industrie constamment tournée vers l'innovation, le secteur européen de la machine-outil voit ces tendances d'un œil positif. Tous les ingrédients pour être au centre de la phase "Usines du futur" sont présents en Europe, où toute une série de nouvelles technologies, y compris celles développées en Europe, vont interagir les unes avec les autres. L'interaction entre les machines CNC de pointe et les robots en est un exemple.
Le magazine DirectIndustry : Concentrons-nous sur l'AM. Comment évaluer son impact sur le secteur ?
F.G. : De nouvelles industries ont commencé à adopter la GA, car elles découvrent les nombreux avantages qu'elle apporte à leur activité. En termes d'applications, l'aérospatiale a été l'un des premiers à adopter la GA et continuera à être l'un des principaux secteurs pour la GA. De nombreuses entreprises de ce secteur ont exploité la flexibilité et l'efficacité de la géométrie offerte par la GA pour éliminer des quantités importantes de matériaux inutiles. D'autres secteurs, tels que la construction et l'énergie, ont commencé à adopter la GA, profitant du niveau élevé de complexité, de résistance et de qualité. La GA peut potentiellement modifier les chaînes d'approvisionnement de nombreux secteurs. Deux aspects qui pourraient avoir un impact substantiel sur la croissance future de la GA sont le développement de normes harmonisées et d'une main-d'œuvre qualifiée. La normalisation est un élément crucial pour l'industrialisation de la GA en Europe. Dans un passé récent, nous avons observé l'implication croissante de plusieurs acteurs de la GA dans les organisations de normalisation (tant au niveau de l'ISO qu'au niveau du CEN), ce qui a donné une grande impulsion à l'élaboration des normes. Le manque de compétences dans le domaine de la GA reste l'un des plus grands obstacles à la croissance du secteur. Il est urgent d'élargir le vivier de travailleurs européens capables de travailler avec des machines AM
Le magazine DirectIndustry : L'usinage hybride n'existait pas il y a 20 ans. Que pouvez-vous dire de cette évolution ?
F.G. : Les machines-outils hybrides qui intègrent la CNC et l'AM pourraient représenter la prochaine étape dans le développement de l'industrie de la machine-outil. L'impression 3D se développe rapidement, et les imprimantes 3D deviennent des outils CNC importants. Il existe encore certaines limites car l'impression 3D avec des métaux nécessite généralement que le métal soit fritté ou fondu à un moment donné du processus, ce qui donne des propriétés mécaniques qui peuvent être très différentes de celles d'une pièce usinée à partir d'un alliage laminé ou trempé à chaud. À ce stade, le défi du processus d'impression 3D consiste à respecter les tolérances précises de l'usinage de haute précision. Par conséquent, il est plus probable que les imprimantes 3D travaillent côte à côte avec des machines CNC plus traditionnelles, plutôt que de les remplacer complètement. Toutefois, il existe également des avantages significatifs : réduction des coûts (par exemple, réduction des déchets de matériaux, réduction de la main-d'œuvre et possibilité de modifications multiples de la conception) ; amélioration des fonctionnalités (par exemple, la possibilité de produire des montages d'outils impossibles à réaliser avec les techniques de fabrication conventionnelles) ; et capacité accrue de personnalisation.
Le magazine DirectIndustry : L'usinage est synonyme de gaspillage et aujourd'hui, par rapport à il y a 20 ans, l'objectif est de parvenir à une industrie climatiquement neutre. Quels types de technologies ont été mis en œuvre pour rendre les machines-outils plus écologiques ?
F.G. : Le secteur des machines-outils est un fournisseur de technologies de fabrication avancées qui contribuent à un secteur plus circulaire et plus durable. Un exemple d'un tel développement est la texturation de surface au laser. Plus de 80% des textures dans la fabrication sont réalisées par gravure chimique. Les technologies de texturation laser offrent une alternative plus propre aux procédés de gravure et permettent de créer des textures en 3D directement à partir de données numériques. Cela signifie l'absence d'utilisation de produits chimiques, un processus répétable et simplifié à 100 %, un niveau de rebut réduit et un processus entièrement numérique : tout cela contribue à une production et à des produits plus durables. Ces développements contribuent également à produire des pièces avec une efficacité supérieure pendant leur durée de vie. L'injection directe d'essence (IDI) en est un exemple. Le développement de l'injection directe d'essence n'a été possible qu'avec la mise au point d'une nouvelle technologie de fabrication, le perçage au laser femtoseconde. Mais il n'y a pas que les développements matériels qui peuvent faire progresser la fabrication circulaire. En fait, les plus grands développements proviennent des logiciels. Des gains d'efficacité de 30 à 50 % ont pu être réalisés grâce aux développements logiciels.
Le magazine DirectIndustry : De nouveaux matériaux tels que les composites ont également fait leur apparition. Quel a été leur impact sur l'industrie des machines-outils ?
F.G. : Les nouveaux matériaux représentent, si l'on considère les principaux clients des fabricants, qui sont le secteur automobile, le secteur aérospatial et le secteur médical, de nouveaux défis mais aussi des opportunités. Les deux premiers secteurs ont besoin de structures techniques légères et très résistantes, de forme parfois complexe, pour réduire le poids, les matériaux nécessaires et la consommation d'énergie de leur produit final. Le secteur médical a besoin de nouveaux matériaux biocompatibles avec des revêtements au niveau des nanoparticules. La production de ces pièces avancées touche tous les aspects du processus de production : personnalisation de masse, développement de machines reconfigurables, amélioration des capteurs, automatisation, etc. En substance, des matériaux plus avancés conduiront sans aucun doute à la mise au point de machines plus innovantes
Le magazine DirectIndustry : La simulation numérique n'existait pas non plus il y a 20 ans : aujourd'hui, nous pouvons simuler les réductions avant qu'elles ne se produisent.
F.G. : Les simulations numériques rapides et précises sont devenues un must pour les fabricants qui cherchent à tirer le meilleur parti des initiatives de fabrication intelligente. Les fabricants doivent éviter les erreurs de programmation coûteuses qui pourraient causer des dommages désastreux aux machines-outils et aux pièces coûteuses. Même une erreur de programmation mineure, par exemple dans le cas d'une pièce aérospatiale, peut devenir une dépense importante. Pour éviter de telles erreurs, il est devenu essentiel de garantir une qualité élevée en utilisant la simulation numérique, par exemple pour régler correctement la coupe. Cependant, certains des obstacles dans le contexte de la simulation numérique concernent l'accès à des modèles solides précis des machines-outils, le nombre élevé d'options dans le matériel et l'outillage des machines ainsi que la performance par rapport à la précision. Deux tendances qui prennent actuellement de l'ampleur dans la simulation numérique sont la sensibilisation aux machines et la recherche de données interactives. L'industrie a connu des progrès spectaculaires dans ce domaine au cours des dernières années, mais il reste encore du travail à faire. En outre, grâce à la surveillance et au contrôle des processus, l'opérateur peut superviser l'ensemble du processus plutôt que de vérifier la pièce à la fin de celui-ci. Le processus peut alors être corrigé tout en continuant à fonctionner, ce qui se traduit par moins de gaspillage et plus d'efficacité.
Le magazine DirectIndustry : De nouveaux acteurs sont apparus sur le marché en provenance de Taïwan, de Corée du Sud et de Chine. Les entreprises européennes et américaines sont-elles toujours leaders sur le marché ?
F.G. : L'industrie des machines-outils est un secteur dynamique et très internationalisé. De nombreux fabricants planifient leurs activités dans différents pays et la chaîne d'approvisionnement mondiale des machines-outils couvre aujourd'hui l'Europe et l'Amérique du Nord, traditionnellement liées à la fabrication, mais aussi les pays d'Amérique latine et d'Asie. Les entreprises européennes et américaines sont toujours les leaders du marché, restant à la pointe de la production et de l'innovation. Toutefois, les entreprises asiatiques, notamment celles de Chine, de Corée du Sud et de Taïwan, sont de plus en plus intégrées dans la chaîne de valeur internationale des machines-outils, soit en tant que fournisseurs, soit en tant que constructeurs.
Par exemple, l'Asie est devenue une région clé en termes de production : en 2018, la part de la production chinoise de machines-outils dans la production mondiale totale de machines-outils était de 28 %, tandis que la production sud-coréenne et taïwanaise de MT s'élevait respectivement à 6,6 % et 5 %. Si l'on considère le commerce, on constate que les marchés régionaux sont devenus sensiblement interdépendants. Le principal client des fabricants européens en dehors de l'Europe est la Chine, qui représente 25 % de leurs exportations totales vers les marchés extérieurs. Le Japon et Taïwan, quant à eux, sont les principaux fournisseurs des fabricants européens, fournissant respectivement 37 % et 15 % du total des importations de machines-outils non européennes. Dans l'ensemble, l'industrie de la machine-outil continue à se développer vers l'extérieur, sous l'impulsion d'entreprises très compétitives et orientées vers le monde.
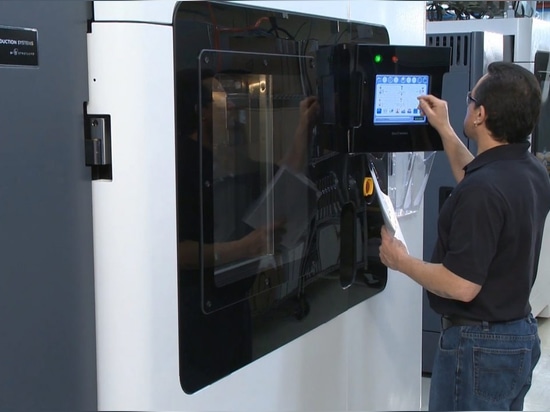
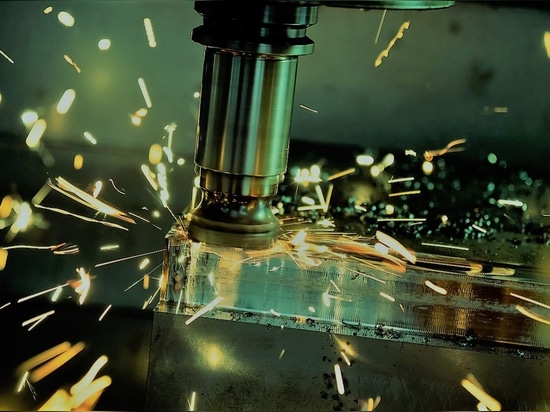