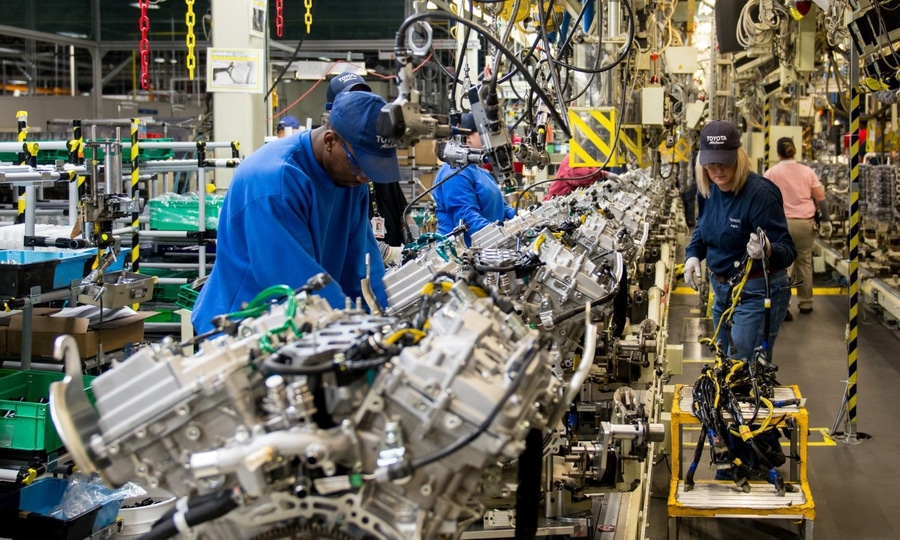
Voir la traduction automatique
Ceci est une traduction automatique. Pour voir le texte original en anglais cliquez ici
#Actualités du secteur
L'usine de moteurs Toyota réduit ses coûts énergétiques grâce à de nouvelles commandes de compresseurs d'air
Les nouvelles commandes permettent d'économiser 1 million de kilowattheures par an et soutiennent les objectifs de Toyota en matière d'émissions zéro.
Vous avez entendu parler des véhicules sans émissions. Mais qu'en est-il de la production de véhicules sans émissions ? C'est la vision de Toyota, l'un des plus grands constructeurs automobiles du monde. Son défi environnemental Toyota 2050 l'invite à éliminer les émissions de CO2 de ses usines de production mondiales d'ici 2050.
Pour atteindre ces objectifs ambitieux, Toyota prend des mesures visant à la fois à réduire sa consommation d'énergie et à passer à une énergie réutilisable. Comme en témoigne l'usine de Huntsville, en Alabama, ces efforts aident Toyota non seulement à réduire son empreinte écologique, mais aussi à améliorer ses résultats.
Coûts énergétiques gonflés
L'usine de Huntsville fabrique des moteurs pour des véhicules Toyota populaires comme le Tacoma, le Tundra et le Highlander. Les travailleurs de l'usine reçoivent des pièces de moteur qui ont été coulées dans d'autres installations pour les usiner et les assembler dans les moteurs qui équiperont les véhicules dans d'autres installations encore.
Le système de compression d'air de l'usine est crucial pour le processus de production. Composé principalement de cinq grands compresseurs d'air centrifuges, le système fournit de l'air à travers l'usine de 1,2 million de pieds carrés pour divers processus de machines, l'automatisation et le séchage des composants de moteurs.
Les systèmes d'air comprimé (CA) sont par nature très gourmands en énergie. Le système de l'usine de Huntsville ne fait pas exception à la règle ; il représente 25 % des coûts énergétiques annuels de l'usine.
Les anciens contrôles ont fait du système un consommateur d'énergie encore plus important qu'il ne le devait. Les commandes vieillissantes étaient lentes à démarrer les compresseurs, ne leur permettaient pas de fonctionner ensemble comme un système intégré et ne disposaient pas de suffisamment de stockage d'AC pour répondre aux pics de demande d'air.
En raison de ces limitations, les membres de l'équipe ont dû maintenir les compresseurs en marche plus que nécessaire pendant la majeure partie de la journée afin d'assurer une capacité d'air suffisante pour faire face aux courtes et occasionnelles poussées de la demande dans l'usine. Eddy Kiggen, un spécialiste des installations chez Toyota, explique,
"Nous avons besoin d'un minimum de 81 PSI pour que les machines fonctionnent sans arrêt. Mais comme les compresseurs ont mis beaucoup de temps à démarrer, nous avons dû maintenir une pression de 91 PSI juste pour être sûrs de ne pas tomber en panne à 81 PSI de basse pression CA"
Le contrat électrique de l'usine a créé d'autres défis. Le contrat fait payer plus cher l'énergie consommée pendant les heures de pointe. Lorsque les membres de l'équipe devaient faire démarrer l'un des gros compresseurs pendant ces périodes pour maintenir la capacité de l'usine, un seul démarrage de machine pouvait augmenter la facture d'électricité de l'usine de 100 % des frais d'énergie d'une journée.
Améliorations locales et à l'échelle de l'usine
Pour aider à maîtriser les coûts énergétiques et soutenir son initiative "énergie 2050", Toyota Motor Manufacturing, Alabama (TMMAL) a décidé de moderniser les systèmes de contrôle des compresseurs d'air de l'usine.
Pour ce travail, ils se sont tournés vers IZ Systems and Case Engineering, un constructeur de machines partenaire du programme Rockwell Automation PartnerNetwork. L'entreprise a fourni une solution en deux parties qui comprenait des contrôles locaux et à l'échelle de l'usine.
Localement, Case a fait migrer les contrôleurs des cinq gros compresseurs vers sa solution de contrôle AirLogix. La solution est basée sur la plate-forme de contrôle CompactLogix et comprend une interface opérateur PanelView Plus 7 pour donner aux travailleurs des données sur les performances et les diagnostics de chaque compresseur.
Au niveau de l'usine, Case a utilisé sa solution de partage de charge AirMaster pour créer un système de contrôle aérien principal. Cette solution est basée sur la plate-forme ControlLogix et utilise le logiciel FactoryTalk View SE pour la collecte et la visualisation des données. Case a travaillé avec IZ Systems, qui a également installé un réservoir de stockage de 5 000 gallons pour une CA boostée de 500 PSI afin de permettre un temps de récupération du système sans défaillance.
Une valve modulante délivre de l'air pendant les périodes de forte demande en air. Cet air stocké assure une transition en douceur lorsqu'une machine centrifuge supplémentaire est nécessaire pour répondre à la demande d'air de l'usine.
Relancer l'épargne
Les nouvelles commandes plus efficaces du compresseur d'air ont permis à l'usine de Huntsville de réduire sa consommation annuelle d'énergie de près d'un million de kilowattheures par an, soit environ 68 000 dollars par an. Cela n'inclut pas les économies réalisées en évitant les démarrages pendant les heures de pointe.
En conséquence, l'usine a récupéré son investissement dans les nouveaux contrôles plus rapidement que son objectif de deux ans. C'est ce qu'a déclaré Kiggen,
"Nous avons pu réduire notre point de consigne pour le système de 91 à 85 PSI. C'est là que se trouve la majorité des économies réalisées sur ce projet"
La mise à jour des commandes locales permet aux compresseurs de fonctionner plus efficacement que les anciennes commandes en augmentant la capacité d'étranglement de chaque machine. Le nouveau contrôleur principal surveille la pression et le débit d'air permettra de démarrer ou d'arrêter les compresseurs en fonction de la demande. Il tirera l'AC du réservoir de stockage à haute pression pendant qu'un compresseur se met en marche, pour faire face aux pics de demande et se protéger contre les problèmes potentiels.
"De la manière dont il est configuré maintenant, nous avons toujours assez de pression dans le réservoir de stockage pour les éventuels creux ou pannes de compresseur. Même si le prochain compresseur que nous essayons de démarrer tombe en panne, nous pouvons en démarrer un autre et les gens de l'usine ne sauront rien de ce qui s'est passé"
Le nouveau système donne aux travailleurs des informations sur les tendances pour surveiller la pression et le débit d'air, la consommation d'énergie et les données critiques de chaque machine, y compris les vibrations. Et parce que ces informations sont disponibles en temps quasi réel - ce que les membres de l'équipe n'avaient pas auparavant - elles permettent d'analyser le système d'AC et d'aider au dépannage.
Les membres de l'équipe peuvent consulter les informations localement sur chaque machine dans le cadre du suivi de leurs opérations de routine. Toyota et Case Engineering peuvent les consulter de n'importe où grâce à un accès à distance.
"Après l'électricité, l'air est le service le plus important que nous ayons, c'est pourquoi nous le surveillons de près. Je regarde les données quotidiennement pour voir comment le système fonctionne et pour examiner son efficacité. Je reçois un SMS si nous avons un problème, comme une chute de pression ou si le réservoir de stockage tombe en dessous d'un certain niveau. Nous aimons aussi que Case soit connecté et qu'il soit informé d'un problème afin qu'il puisse se connecter pour le régler immédiatement"
Toyota envisage de reproduire ce projet ailleurs pour réaliser des économies d'énergie similaires tout en continuant à tendre vers des émissions de CO2 nulles.
"Produire du CO2 zéro dans le processus de construction d'un véhicule est une tâche très importante. En ce moment, nous essayons d'économiser le plus d'énergie possible avant de nous lancer dans les énergies renouvelables. Et pour cette usine, ces améliorations de contrôle sont les projets énergétiques les plus réussis que nous ayons réalisés depuis longtemps"
Les résultats mentionnés ci-dessus sont spécifiques à l'utilisation par Toyota des produits et services de Rockwell Automation en conjonction avec d'autres produits
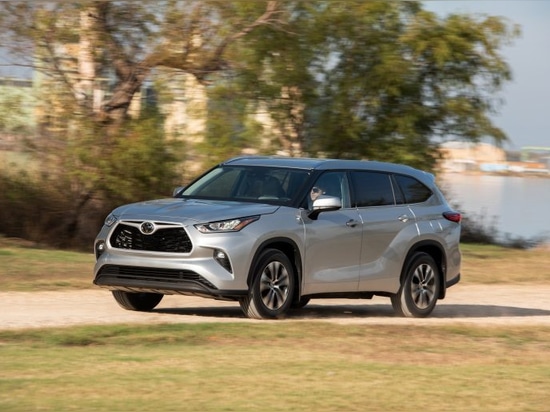
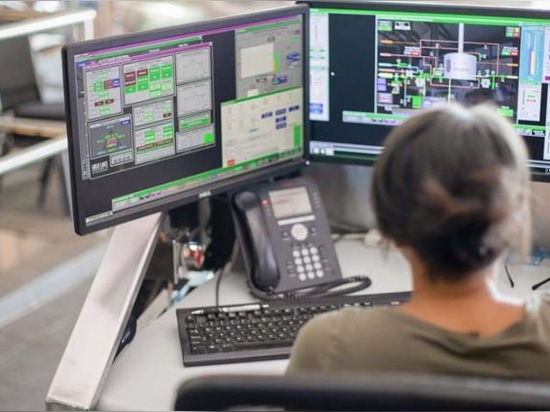
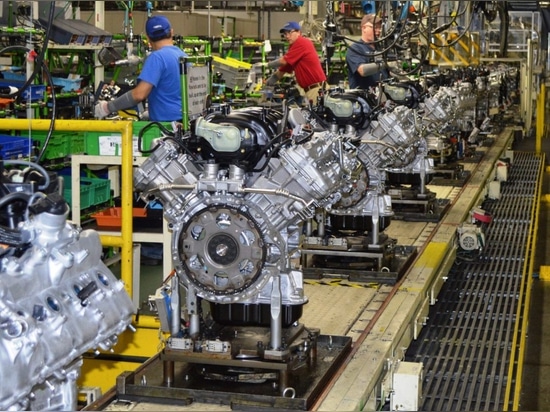
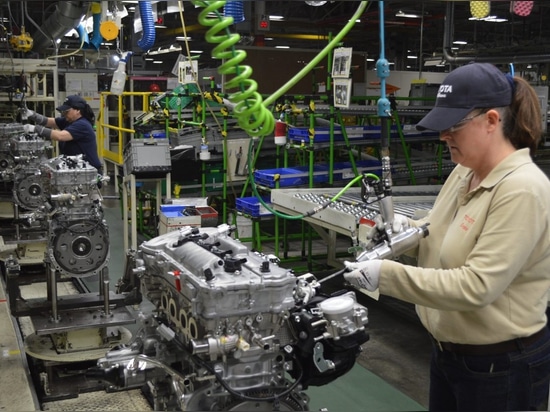