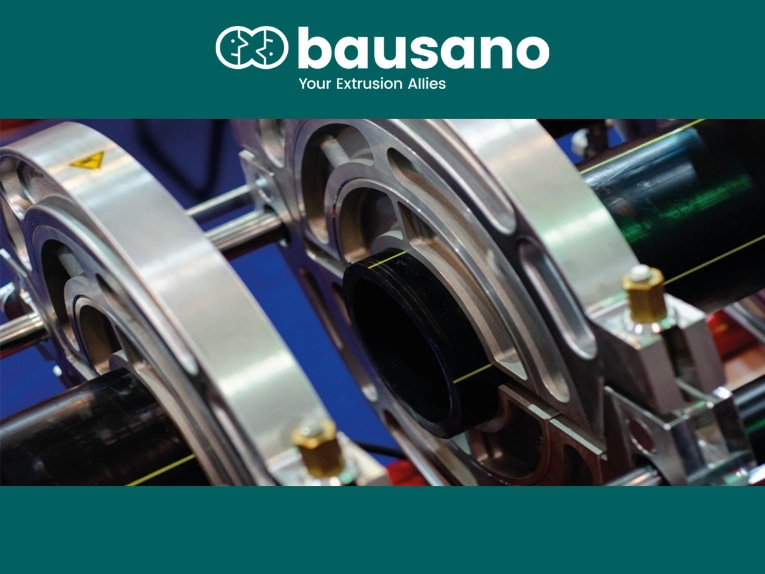
#Actualités du secteur
Tuyaux en PEHD de diamètre supérieur et problèmes de refroidissement
Le maintien des dimensions dans les spécifications est problématique pour l'extrusion de tuyaux en PEHD à paroi épaisse de grand diamètre (> 75 mm de paroi) en raison de l'affaissement causé par une résistance à la fusion insuffisante de la résine.
Le diamètre du tuyau en PEHD augmente pendant l'extrusion et cela provoque une augmentation de l'épaisseur, le tuyau ne refroidit pas efficacement de l'intérieur et de l'intérieur du noyau et la vitesse linéaire diminue.
Les tuyaux de grand diamètre prennent généralement 3,30 heures pour être produits et peuvent avoir divers segments de cristallinité, d'épaisseur et de teneur en humidité différentes. Dans la plupart des processus d'extrusion de PEHD, 60 % à 80 % de la cristallisation a lieu pendant la phase de refroidissement du traitement, et jusqu'à 90 % se produit dans la semaine suivant le traitement. La cristallisation restante peut prendre des mois, selon la température ambiante. Cependant, la cristallisation se poursuit jusqu'à ce qu'une structure cristalline stable soit atteinte.
Pour les tuyaux à paroi épaisse, l'intérieur du tuyau reste fondu pendant dix heures, provoquant un écoulement de fusion vers le bas appelé affaissement. Cela peut entraîner de graves non-uniformités dans l'épaisseur de la paroi du tuyau.
Celle-ci peut être compensée de deux manières :
En compensant l'écart de filière, mais cela prend du temps et conduit toujours à l'utilisation de matière supplémentaire
En utilisant un matériau HDPE à faible affaissement et en optimisant le processus de refroidissement.
La manière conventionnelle de réduire l'affaissement consiste à ajuster manuellement l'excentricité de la matrice, jusqu'à ce qu'un profil d'épaisseur de paroi acceptable soit atteint.
Pour minimiser les efforts et compenser l'effet d'affaissement, l'écartement de la filière est ajusté avant de commencer l'extrusion de manière à ce que l'écartement de la filière soit plus en haut et moins en bas de la filière.
Nous pouvons utiliser des instruments de mesure d'épaisseur de ligne à ultrasons, avec quatre emplacements à 90° les uns des autres et donner un affichage de la variation d'épaisseur sur l'écran. Alternativement, un équipement portable peut être utilisé pour mesurer l'épaisseur de ligne à divers endroits du tuyau.
Une fois que nous avons connaissance de la variation d'épaisseur, nous pouvons l'affiner en modifiant la température du réchauffeur segmenté de manière appropriée pour contrôler l'épaisseur et économiser le gaspillage ainsi qu'améliorer la qualité.
En raison de l'épaisseur de paroi élevée et du processus de refroidissement lent régi par la conductivité thermique du PE, il est de la plus haute importance que le HDPE à l'état fondu possède une résistance à la fusion suffisante pour empêcher le matériau de s'affaisser au fond du tuyau.
L'utilisation d'hexène, un composé organique, développé pour les tuyaux de très grand diamètre est connue pour fournir une meilleure résistance à la croissance lente des fissures et une résistance à la propagation rapide des fissures, ainsi qu'une résistance à la fusion supérieure.
La distribution du poids moléculaire a été ajustée pour augmenter la viscosité à de faibles taux de cisaillement, ce qui réduit l'affaissement, tout en permettant d'utiliser le même matériau pour des tuyaux de plus petit diamètre.
Une nouvelle façon a été proposée pour réduire l'affaissement, en faisant tourner le tuyau pendant le refroidissement.
Vous pouvez trouver plus de détails auprès de Yashodhan Kanade, un grand technologue en PVC.