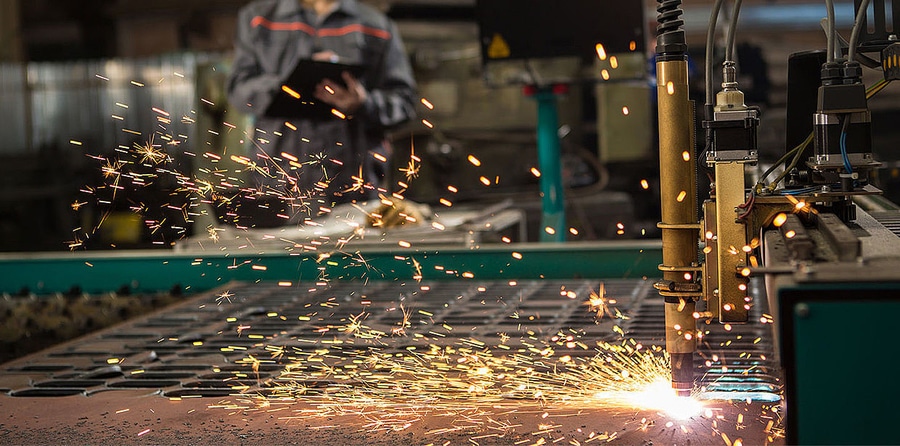
Voir la traduction automatique
Ceci est une traduction automatique. Pour voir le texte original en anglais cliquez ici
#Actualités du secteur
Découpe de tôle : Le processus correct de découpe du métal
Pour qu'une pièce de métal devienne un produit, elle doit être découpée. Les processus de découpe sont aussi variés que les formes de métal. Dans cet article, nous vous donnons un aperçu de ce qui est pertinent pour le traitement industriel de la tôle.
Qu'il s'agisse de matériaux fins ou épais, de produits sur mesure ou de masse, les exigences en matière de découpe du métal peuvent varier considérablement. Plusieurs processus en aval en dépendent également. Dans l'industrie du traitement et de la fabrication des métaux, l'efficacité est très importante. C'est pourquoi les outils de coupe manuels tels que les cisailles à métaux ne jouent pratiquement aucun rôle.
Si l'on classe les procédés de découpe en fonction de l'épaisseur des tôles, l'oxycoupage autogène arrive en tête. Ces procédés sont utilisés pour les aciers non alliés et faiblement alliés d'épaisseur moyenne à grande. Il est également apprécié en raison de sa rentabilité pour les tôles d'une épaisseur de 50 mm et plus. Pour les tôles d'une épaisseur supérieure à 250 mm, il n'existe actuellement aucune autre méthode de découpe.
Lors de l'oxycoupage, une flamme chauffe le matériau en surface jusqu'à ce qu'il atteigne sa température d'inflammation (entre 1150 et 1250 °C pour l'acier doux). Le métal brûle grâce à l'apport d'oxygène. La chaleur de combustion chauffe à son tour le matériau sous-jacent jusqu'à la température d'allumage. Cela permet au processus de se poursuivre automatiquement (de manière autogène) en profondeur. L'oxyde de fer non brûlé devient liquide et est expulsé du joint avec l'oxygène de coupe. Il peut se déposer sous forme de scories sur la face inférieure du matériau.
L'oxycoupage autogène fonctionnant mal ou pas du tout avec des matériaux tels que les aciers fortement alliés, l'aluminium ou le cuivre, l'oxycoupage plasma a été mis au point. Le procédé crée un orage dans la tôle : dans la nature, un orage produit de l'ozone (O3) sous forme de gaz plasmatique lorsqu'un arc électrique se décharge. Après un orage, on peut sentir l'odeur de l'"air pur".
Le plasma est un gaz conducteur d'électricité. Le découpage au plasma utilise la chaleur du plasma pour liquéfier le matériau en un point précis. L'énergie cinétique élevée du flux de volume du gaz plasmatique souffle ensuite le matériau liquéfié.
La coupe dans le métal est réalisée en soufflant le trait de scie et le taux d'alimentation de la tête de coupe. Les épaisseurs de matériau typiques pour le découpage au plasma se situent approximativement entre 0,5 et 160 mm. Grâce à ses vitesses de coupe élevées, ce procédé s'est également imposé dans des domaines d'application jusqu'alors réservés à l'oxycoupage.
Si vous souhaitez utiliser des tôles plus fines pour la découpe, l'emboutissage est un procédé important. Il permet de produire des pièces plates ou d'introduire des formes et des contours dans une tôle. Les pièces embouties sont fabriquées industriellement dans une machine d'emboutissage à l'aide d'outils d'emboutissage. Ce dernier se compose de deux parties, la presse et la matrice, dont l'ouverture correspond à celle de la presse. Pendant le processus d'estampage, la presse se déplace linéairement et plonge dans la matrice. Les bords du poinçon et de la matrice se déplacent parallèlement l'un à l'autre, séparant ainsi la feuille.
Lors du formage de la tôle, le résultat du processus d'emboutissage n'est pas une coupe continue, même s'il en a parfois l'apparence. Au contraire, les forces avec lesquelles la presse d'emboutissage appuie sur le matériau coupent dans la zone supérieure. Dans la zone inférieure, le matériau se brise lorsque le poinçon sort du matériau.
Il doit y avoir un espace de coupe entre l'arête de coupe du poinçon et l'arête de coupe de la percée de l'insert. Sa taille dépend de la résistance et de l'épaisseur du matériau. En général, la fente de coupe atteint 2 à 5 % de l'épaisseur du matériau. La taille de la fente de coupe influence ensuite divers facteurs, notamment la hauteur de la bavure sur la pièce découpée.
Le grignotage est un cas particulier de poinçonnage. Dans ce processus, un outil de poinçonnage ouvert d'un côté est utilisé pour aligner de nombreux trous sur le bord d'une feuille. Contrairement à l'estampage et au cisaillage conventionnels, ce procédé permet d'obtenir un plan de joint et un façonnage libre ou un processus de coupe indépendant de l'outil. L'outil peut se déplacer dans toutes les directions et ainsi créer des formes complexes.
L'un des avantages de l'estampage est qu'il permet de produire efficacement de nombreuses pièces similaires. Toutefois, les coûts d'outillage ont un effet négatif sur les petites séries ou les pièces individuelles. C'est pourquoi la découpe au laser s'est imposée dans le traitement de la tôle. Les faisceaux laser utilisés sont constitués d'ondes électromagnétiques. Le faisceau laser peut chauffer et ablater presque n'importe quel matériau, ce que l'on appelle l'ablation en physique.
À proprement parler, deux processus se déroulent simultanément lors de la découpe au laser : Tout d'abord, le matériau au niveau du front de coupe absorbe le faisceau laser et s'échauffe. D'autre part, le gaz de soufflage expulse le matériau ablaté hors de la ligne de coupe, protégeant ainsi l'optique de focalisation des vapeurs et des éclaboussures. Selon que le matériau est retiré du trait de coupe sous forme de liquide, de produit d'oxydation ou de vapeur, on distingue la découpe par fusion au faisceau laser, la découpe par flamme au faisceau laser et la découpe par sublimation au faisceau laser. Cela a également des conséquences sur la formation de bavures. Dans le cas de l'oxycoupage laser, les arêtes de coupe présentent également une couche d'oxyde après le processus, qui doit être éliminée.
La découpe laser fonctionne jusqu'à une épaisseur de matériau d'environ 40 mm, avec l'acier inoxydable jusqu'à environ 50 mm et avec l'aluminium jusqu'à 25 mm. Ce dernier matériau est toutefois difficile à découper, car il réfléchit une grande partie du rayonnement laser et parce que sa conductivité thermique élevée dissipe une grande partie de l'énergie de la fente de découpe. Il en va de même pour le cuivre.
La découpe au jet d'eau est plutôt une niche dans le domaine de la tôlerie. Ici, un jet d'eau d'une pression de 4 000 bars et d'une vitesse de 900 m/s est utilisé pour découper le métal.
L'enlèvement de matière dans ce processus est basé sur la pression élevée que le jet exerce sur la surface du matériau. Le jet d'eau n'enlève que les particules microscopiques proches de la surface. L'eau qui s'écoule provoque en outre des forces de cisaillement qui contribuent également à l'enlèvement de matière.
L'avantage de la découpe au jet d'eau est qu'elle repose uniquement sur la pression et non sur l'énergie thermique. En effet, la chaleur des procédés tels que l'oxycoupage, le plasma ou le découpage au laser peut déformer les pièces.
Le fraisage est un autre procédé de découpe des métaux peu courant dans la fabrication de tôles. L'outil de fraisage enlève la matière en tournant autour de son axe à grande vitesse. Au cours du processus, soit l'outil traverse le contour souhaité, soit la pièce est déplacée. Au cours de ce processus, l'outil de fraisage enlève des copeaux de l'ébauche pour produire la forme.
Aussi courant que soit le fraisage dans la fabrication industrielle, il tend à être l'exception dans la fabrication de tôles pour produire le contour. On ne le trouve que dans la construction aéronautique et la technologie médicale, et parfois dans la production de panneaux avant en aluminium.
Comme dans tous les processus d'usinage, des bavures apparaissent lors du fraisage et doivent être éliminées.