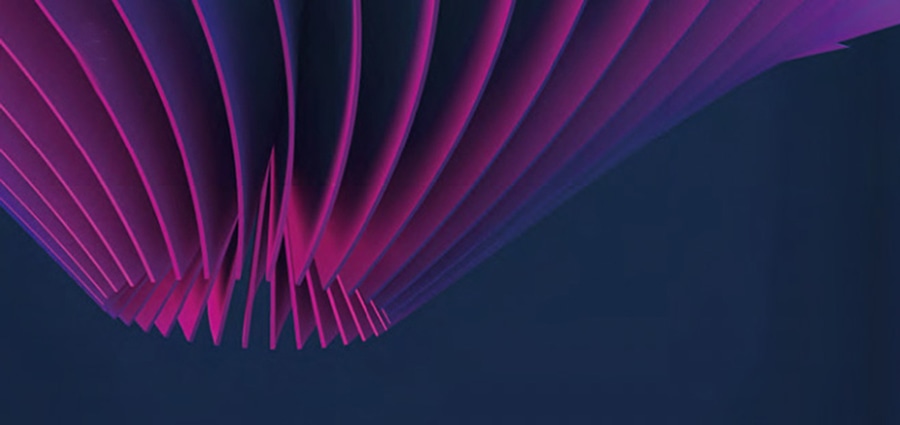
Voir la traduction automatique
Ceci est une traduction automatique. Pour voir le texte original en anglais cliquez ici
#Actualités du secteur
Usinage par électroérosion (EDM) de roues de turbines pour compresseurs industriels
Deux des points forts d'ONA dans le secteur de la fabrication de composants de turbines reposent sur notre expertise en matière d'usinage par électroérosion (EDM) de pièces très complexes, ainsi que sur plus de 25 ans d'expérience dans la fourniture de solutions clés en main pour les turbines .
C'est ce leadership sur le marché et cette connaissance experte qui ont conduit l'une des entreprises de référence dans la fabrication de pompes et de vannes à faire confiance à ONA pour développer les roues de turbine de ses équipements rotatifs.
L'électroérosion est l'option la plus efficace et la plus viable pour usiner des pièces aux géométries compliquées, telles que les cavités des turbines. Cela est dû au fait que la technologie EDM permet de surmonter les difficultés présentées par d'autres techniques traditionnelles, comme le fraisage, qui entraîne souvent des taux élevés de casse d'outils ou, surtout dans le cas de géométries fermées ou complexes comme les turbines, l'impossibilité pour les outils de fraisage d'atteindre toutes les zones à usiner.
Cependant, si l'usinage par électroérosion est la méthode la plus à même de fournir une solution optimale d'érosion et d'usinage, elle pose également des défis majeurs : L'électroérosion implique la prise en compte de plusieurs facteurs compliqués, tels que la conception et le nombre d'électrodes nécessaires, leur trajectoire, le niveau d'usure, etc.
Pour relever ces défis, notre équipe d'ingénieurs a développé une "solution clé en main" qui répond à tous les besoins donnés par le client. À cette fin, elle a étudié et évalué le cas spécifique en détail, et a réussi à développer l'application sur mesure pour l'usinage des roues, le "cœur" des turbines, qui seraient utilisées par notre client pour produire de l'énergie, pomper et déplacer les fluides des compresseurs industriels.
Comment nous avons réussi à le faire
Sur la base des dessins fournis par le client et des besoins exprimés, l'équipe d'ONA a évalué la pertinence de l'utilisation de la technologie d'électroérosion par enfonçage pour l'usinage de pièces géométriquement compliquées telles que les turbines.
1. Mise en page.
Dans cette phase initiale, il était essentiel de définir correctement les axes impliqués dans le processus, ainsi que la position et l'orientation de la pièce à usiner, car ces deux facteurs affectent considérablement la conception et la trajectoire des électrodes, la taille de l'usinage et peuvent même compromettre la viabilité du projet lui-même.
2. Conception et trajectoire des électrodes
Actuellement, il n'existe pas sur le marché de logiciel commercial de CFAO capable de déterminer la conception et la trajectoire des électrodes comme dans le cas d'autres applications, ce qui signifie qu'il faut faire appel à des connaissances spécialisées pour développer des algorithmes et des méthodologies ad hoc afin de définir ces paramètres. Il n'y a donc pas de solution unique, mais chaque pièce nécessite un projet personnalisé en fonction de ses caractéristiques et besoins particuliers.
3. Usinage des électrodes.
Les défis de l'usinage et du fraisage des électrodes elles-mêmes sont principalement liés à leurs géométries complexes et à la nécessité de respecter des tolérances très serrées ; cela signifie qu'une erreur dans l'électrode entraîne une erreur dans la pièce.
4. Les paramètres d'électroérosion.
Pour un usinage stable de la pièce, les différents paramètres d'électroérosion doivent être correctement définis. Ces paramètres sont principalement définis par la rugosité de surface requise (plus le temps d'usinage est court, plus la rugosité est élevée) et la géométrie (des surfaces plus grandes permettent d'appliquer plus d'énergie).
5. Usure de l'électrode.
L'usure est une conséquence inévitable du processus d'électroérosion ; elle ne peut être évitée mais elle peut être contrôlée et minimisée.
6. Métrologie
Compte tenu de la difficulté d'accéder à la pièce elle-même, l'analyse dimensionnelle de la pièce en question est un défi en soi ; ainsi, des méthodes comme l'analyse destructive, la définition de points stratégiques ou l'utilisation d'éléments de mesure standard sont quelques-unes des possibilités à envisager ici.
LA SOLUTION D'ONA : comment nous l'avons trouvée
Afin de surmonter avec succès tous les défis liés à ce projet, il était essentiel de faire appel à une équipe d'ingénieurs comme celle d'ONA, experts en technologie EDM.
Après une étude préliminaire approfondie de la pièce et de ses différents paramètres, et après une évaluation de la faisabilité du projet, la proposition de nos ingénieurs a été de développer une application pour notre machine d'électroérosion par enfonçage IRIS 6+. Cet équipement, entre autres avantages, offre une précision d'électroérosion maximale et des niveaux de productivité élevés
Outre le choix de la machine la plus adaptée, le développement complet de l'application finale par ONA comprenait des paramètres critiques tels que la définition des électrodes requises et l'analyse de leur usure. Dans le cas de ce projet, l'application a nécessité 4 électrodes différentes pour obtenir des trajectoires complètes. C'est également l'un des avantages concurrentiels d'ONA en termes d'optimisation du temps. Bien qu'une éventuelle usure des électrodes soit inévitable, la technologie intégrée dans le générateur numérique 100% intelligent d'ONA IRIS permet de réutiliser les électrodes et de réduire leur usure.
De même, l'équipe d'ingénieurs a développé la trajectoire tridimensionnelle (courbes, inclinaisons...) que notre machine doit suivre pour que l'ensemble du processus soit correctement exécuté et, lorsque cela était nécessaire, un outil de serrage personnalisé a été mis en place pour positionner correctement la pièce.
Conclusions
- ONA prouve sa capacité à s'attaquer à des projets intégraux clés en main.
- Développement d'une application personnalisée pour la fabrication d'une pièce très complexe en termes de forme, d'accès et de cavités.
- Exemple clair du potentiel technologique et du savoir-faire en matière d'électroérosion.
- Précision et fiabilité des machines IRIS pour l'usinage de pièces critiques et complexes.
- ONA en tant que partenaire technologique spécialisé dans des secteurs tels que la fabrication de composants de turbines. Dans ce cas particulier, l'accent est mis sur l'usinage des roues, mais vous pouvez lire ici une autre étude de cas concernant notre solution personnalisée pour l'usinage des alésages de diffuseur dans les pales de turbine.
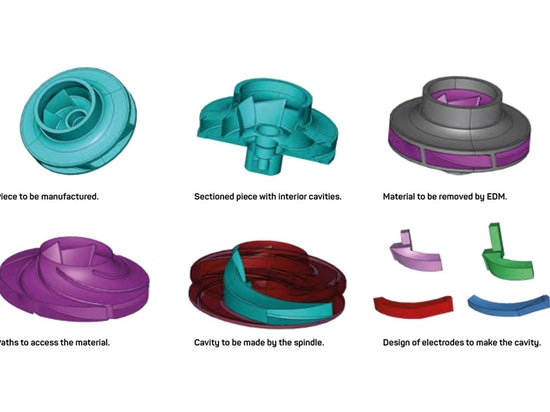
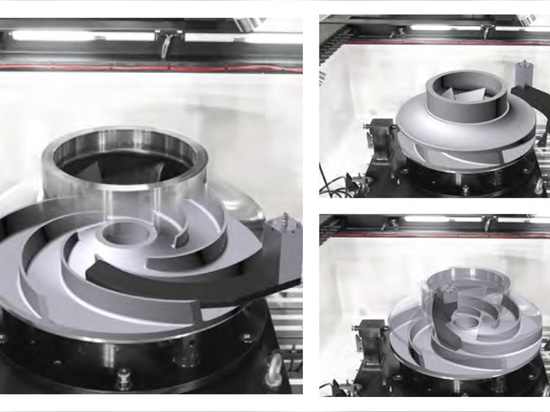