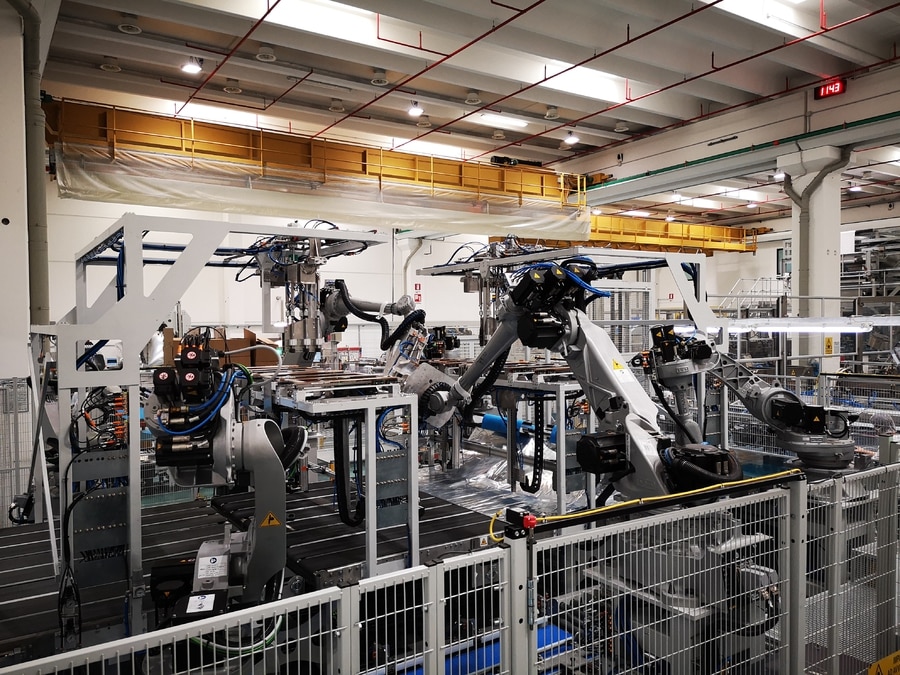
Voir la traduction automatique
Ceci est une traduction automatique. Pour voir le texte original en anglais cliquez ici
#Actualités du secteur
L'automatisation extrême appliquée aux emballages souples
Robots articulés Comau pour le pliage multiple de sacs multicouches
Les robots articulés Comau ont été intégrés dans l'usine du groupe Goglio à Daverio (près de Varese, dans le nord de l'Italie). Les robots sont utilisés à la fois pour le pliage multiple de sacs multicouches équipés de becs de remplissage et pour l'emballage optimal des produits finis dans des boîtes en carton avec un conteneur aseptique interne.
L'installation, qui fait appel à des technologies très innovantes, a été conçue par Siscodata, un important intégrateur de systèmes.
Goglio est l'un des leaders mondiaux dans le secteur de l'emballage flexible. Fondée en 1850 par la famille Goglio, l'entreprise a connu une croissance constante au fil des ans grâce à ses investissements dans des systèmes de production innovants et de plus en plus automatisés. Les clients de Goglio sont des entreprises manufacturières du monde entier qui opèrent dans divers secteurs industriels, notamment la production de café, le remplissage aseptique et à chaud, les plats préparés, les aliments et les boissons, les cosmétiques et les détergents, les produits chimiques industriels et les aliments pour animaux de compagnie.
Le modèle d'entreprise de Goglio est représenté par Fres-co System, une marque déposée créée en 1961 et qui identifie parfaitement la mission de l'entreprise : la production de systèmes d'emballage pour conserver les aliments aussi frais que s'ils sortaient de l'usine. L'offre de Goglio se compose de laminés souples à haute barrière, de lignes d'emballage, d'accessoires en plastique, d'assistance technique et de service.
Par son activité, Goglio s'engage pleinement à proposer des solutions qui garantissent une alimentation suffisante, sûre et saine pour tous, tout en respectant la planète et son équilibre. Pour atteindre ces niveaux de fiabilité des produits, l'entreprise a choisi une structure verticale pour son processus de production, comme l'explique Luigi Foglia, qui dirige l'unité des sacs aseptiques et industriels de la division Emballage. "Afin d'avoir un contrôle total sur la qualité de nos produits, nous visons à tout produire à l'intérieur de nos usines. Par exemple, pour fabriquer un sac aseptique, nous achetons du polyester, du nylon et de l'aluminium à des fournisseurs externes, mais tout le reste est réalisé en interne, y compris la production des valves et des becs et les graphiques sur les sacs. Cette approche nécessite évidemment une organisation parfaite, qui nous permet également de traiter rapidement tout produit défectueux"
Avec huit sites de production et sept bureaux commerciaux dans le monde entier, Goglio peut raisonnablement être considérée comme une entreprise mondiale. Elle emploie au total 1 754 personnes, dont 992 en Italie.
Outre la succursale de Daverio - qui abrite le siège de l'entreprise, la division Emballage/Polymères et le Centre technologique - il existe trois autres sites en Italie : Milan (division Plastiques), Zeccone (fabrication de machines) et Cadorago (division Cofibox).
À l'étranger, Goglio possède une usine de production aux Pays-Bas (emballages souples), deux aux États-Unis (emballages souples, machines et accessoires en plastique) et une autre à Tianjin, en Chine (emballages souples et fabrication de machines).
Parlant des États-Unis, Luigi Foglia a souligné : " [...] nos succursales aux États-Unis se sont développées main dans la main avec Starbucks, la célèbre franchise de café américaine avec une approche unique. Il y a des années, la direction du groupe Goglio croyait en ce projet, et les deux sociétés ont connu une croissance exponentielle au fil des ans grâce à une collaboration mutuelle"
En 2018, le groupe a réalisé un chiffre d'affaires de 375 millions d'euros, dont près de 50 % provenait de la production de café, suivie de la transformation aseptique (19,1 %), des produits industriels (11 %), de l'alimentation et des boissons (9,6 %) et d'autres divisions. La fabrication de machines représente environ 9 % du revenu total.
L'automatisation est une garantie de croissance
Luigi Foglia a affirmé : "L'automatisation a toujours fait partie de l'ADN de Goglio. Elle nous aide à rendre nos systèmes de fabrication plus efficaces tout en réduisant les coûts de production, et elle permet également à notre personnel d'effectuer des tâches à plus forte valeur ajoutée, comme le contrôle qualité" À cette fin, Goglio a entamé une collaboration fructueuse avec Comau et l'intégrateur de systèmes susmentionné Siscodata Computer Srl, qui est basé à Arcisate (près de Varèse) et qui est spécialisé dans la fabrication de systèmes robotiques pour plusieurs secteurs industriels. Plus précisément, Goglio a chargé Siscodata de développer un système robotique capable de résoudre des problèmes de production tels que le pliage et l'emballage manuel de sacs multicouches dans un film métallique équipé de becs de remplissage
Pour la production manuelle de ces sacs, Goglio utilisait une machine à plier les draps, dont la taille maximale est celle d'un lit double. Après le pliage automatisé, la procédure était effectuée par des opérateurs, qui mettaient les paquets dans des boîtes équipées de récipients aseptiques internes. Pour les plus grands paquets, tout le processus devait être effectué manuellement. Ce matériau est très glissant et, comme la taille des sacs a augmenté au fil des ans, l'utilisation des machines de pliage existantes est devenue impossible.
Goglio n'avait pas seulement besoin de robotiser le processus, mais aussi de le rendre suffisamment polyvalent pour gérer des sacs de 220 litres à double canal (1 x 1,8 m) et passer rapidement à des sacs de 1/1,5 tonne (2,2 x 2,6 m) équipés de deux types de valves différents, respectivement de 1" ou 2". L'entreprise avait donc besoin d'un moyen de robotiser et d'accélérer le pliage et le roulage de ces sacs, ainsi que le placement échelonné des produits dans des boîtes.
Siscodata, en collaboration avec Comau, a conçu un îlot robotique composé de quatre robots articulés Comau NS16, avec une charge utile de 16 kg et une portée de 1,65 m, et de deux robots Comau NJ40, avec une portée de 2,5 m, qui plient les sacs transversalement et les mettent dans les boîtes. Les robots sont positionnés sur une base en acier et sont reliés à une formeuse de caisses (qui forme des boîtes équipées d'un conteneur aseptique interne) et à une machine à scotcher. Les quatre robots de pliage sont équipés d'une pince spéciale pour collecter les sacs qui ont été déposés sur un convoyeur d'entrée ; ce dernier comporte également une machine d'empilage et une unité d'alignement des becs, qui sont assemblés sur les sacs avant le processus de pliage.
Lorsque les sacs arrivent sur le tapis roulant - par paires ou individuellement, selon leur taille - ils sont collectés par deux robots (un de chaque côté) qui les roulent et les plient. Les quatre robots NS16 travaillent en alternance pour assurer une grande vitesse. Ensuite, chaque robot place un sac plié dans une station de stockage, où les deux autres robots les collectent, les plient transversalement et les déposent dans les cartons avec un conteneur aseptique interne. Lorsque le remplissage est terminé, la machine à ruban adhésif ferme la boîte. Les produits sont placés de manière à ce qu'ils soient constamment décalés et échangés (haut/bas, droite/gauche) pour alterner les becs en plastique à l'intérieur de la boîte et optimiser l'espace. Grâce à ce nouveau système, le nombre de sacs par boîte est passé de 36 dans le processus manuel à 42/44 pièces, ce qui permet de gagner beaucoup de place lors de la phase d'expédition.
Giulio Scifo, directeur des ventes de Comau pour l'Italie, a déclaré : "Avec Siscodata, nous avons identifié les robots Comau les mieux adaptés à cette application particulière. La particularité des quatre robots NS16 est qu'ils travaillent de manière coopérative grâce à une seule armoire de commande, une caractéristique qui permet également de réaliser des économies importantes sur les coûts de duplication du matériel et d'optimisation de l'espace. Cela se voit également dans la façon dont les deux robots enroulent les sacs provenant de la bande transporteuse en parfaite synchronisation"
Le temps de cycle de la centrale étant très rapide (un sac toutes les six secondes), les techniciens de Comau et de Siscodata ont dû travailler dur pour mettre au point la solution requise. Il y avait deux défis principaux : utiliser des robots articulés avec une faible charge utile pour atteindre des vitesses élevées ; mettre en place une pince légère pour enrouler les sacs avec des tiges de plus d'un mètre de long. Par conséquent, un élément clé du projet était l'étude et la mise en œuvre d'une pince capable de rouler et de plier en même temps.
Roberto Brambilla, propriétaire de Siscodata, a expliqué le processus plus en détail : "La nécessité de faire fonctionner l'usine à grande vitesse a affecté le projet dans son ensemble. Comme nous ne pouvions pas utiliser de robots avec une charge utile élevée, car ils sont trop lourds et donc trop lents pour manipuler les charges impliquées, nous avons concentré notre attention sur le développement de la pince, qui a une portée d'environ 1,2 m et devait être à la fois rigide et légère. Pour son développement, nous avons recherché des matériaux innovants, car nous envisagions de l'utiliser encore mais il s'est avéré trop lourd. Nous sommes passés à un alliage d'aluminium utilisé dans l'ingénierie aérospatiale, ce qui a cependant provoqué un pliage critique de la pince. La solution ultime s'est avérée être l'utilisation de fibres de carbone façonnées en fonction de nos besoins. De plus, comme la pince doit également effectuer une rotation pendant la phase de roulage, nous avons ajouté un moteur sans balais supplémentaire comme septième axe, ce qui est un de plus que les six axes standard des robots Comau"
Luigi Foglia a ajouté avec grande satisfaction : " [...] Grâce à ce système, qui est pleinement opérationnel depuis début mars, nous avons pu reprendre notre production à pleine capacité, même si nous n'avons pas encore atteint le flux de travail prévu. Selon nos estimations, la capacité du système est actuellement à 75 % de l'efficacité de la production, alors que l'objectif est de 95 % de productivité et de continuité dans une journée de travail. Toutefois, nous sommes convaincus que la production continue aidera à surmonter les problèmes liés au démarrage du système et que nos objectifs seront bientôt atteints. L'avantage de ce système consiste principalement en une réduction de la main-d'œuvre et une diminution des tâches pénibles pour les opérateurs restants"
En conclusion, le système robotique installé à Goglio pour robotiser le processus d'enroulement et de pliage des BIB (Bags in Box) est doté de technologies très innovantes qui le rendent extrêmement intéressant. Pour parvenir à ce résultat, Comau et son intégrateur de système à long terme Siscodata ont travaillé en étroite collaboration afin de répondre au mieux aux besoins de Goglio. Giulio Scifo a souligné : "Ce système représente pour Comau un type d'application très particulier dans l'industrie générale. Ce n'était pas la première fois que nous mettions en place des cellules robotisées avec plusieurs robots travaillant dans un espace réduit. Le plus grand défi, dans ce cas, était la nécessité de faire coopérer les six robots en continu avec des cycles de travail particulièrement stressants"
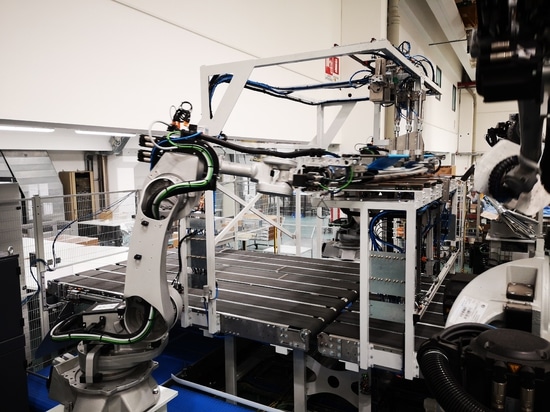