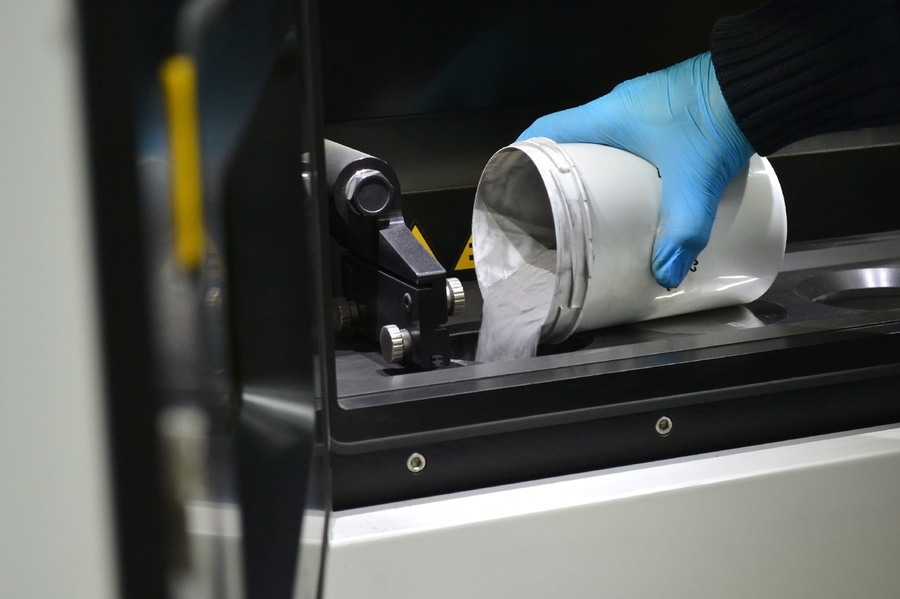
Voir la traduction automatique
Ceci est une traduction automatique. Pour voir le texte original en anglais cliquez ici
#Tendances produits
Traitement des poudres pour la fabrication additive avec des mélangeurs industriels
Les équipements de mélange, de séchage sous vide et de réaction jouent un rôle crucial dans la production et le reconditionnement des matériaux pour l'impression 3D à base de poudre.
L'impression 3D sur lit de poudre se déroule successivement, couche par couche. Pour chaque couche de la structure, un lit de poudre est d'abord déposé à l'épaisseur souhaitée. Ensuite, une source d'énergie contrôlée avec précision fait fondre ces amas de particules poudreuses dans les dimensions exactes de la section transversale. Enfin, les poudres excédentaires sont éliminées, idéalement pour être réutilisées dans les couches suivantes.
Pour obtenir un produit final fonctionnel, les poudres utilisées dans l'impression 3D doivent être suffisamment stables pour que la taille des particules, la densité apparente et les caractéristiques rhéologiques ne soient pas affectées par le processus de fusion. Parallèlement, chaque étape du processus doit se dérouler rapidement si l'on veut garantir un bon rapport coût-efficacité. La rapidité du traitement est généralement facilitée par la mise en œuvre d'un transport pneumatique, qui peut souvent entraîner un degré élevé d'abrasion. C'est pourquoi les poudres de polymères utilisées dans l'impression 3D doivent être conditionnées de manière experte.
Ce même défi s'applique au micro-frittage sélectif par laser, un processus de fabrication 3D qui utilise des poudres métalliques. Les matériaux métalliques sont déposés dans le lit de poudre à l'aide d'une racle, une opération qui prend souvent beaucoup de temps. Les caractéristiques de fluidité des matériaux jouent un rôle décisif dans l'homogénéité du lit de poudre. Les poudres doivent être aussi fluides que possible, ce qui implique une forme sphérique des particules et une distribution étroite de leur taille. En outre, les agglomérats doivent être éliminés afin d'éviter la formation de défauts laminaires ou linéaires dans le composant fini. La plupart des poudres métalliques utilisées dans l'impression 3D sont cohésives et ont une taille de particule inférieure à 10 µm, ce qui signifie qu'elles ont tendance à s'agglomérer et à adhérer à la racle ou à la surface de travail. Si ce phénomène est désagréable, il est également difficile à éviter.
Afin d'empêcher la formation d'agglomérats indésirables, les poudres d'impression 3D peuvent être recouvertes d'additifs nanoscopiques pour les conditionner. Ce processus de conditionnement s'effectue de préférence dans un mélangeur de précision automatisé ou dans un processeur à lit fluidisé, où les agglomérations et les agglomérats indésirables sont moins susceptibles de se former et où les caractéristiques de fluidité des poudres peuvent être améliorées.
Le rôle des mélangeurs, des sécheurs sous vide et des réacteurs de synthèse dans la fabrication des poudres d'impression 3D
Les équipements de mélange, de séchage et de réaction jouent un rôle important dans la métallurgie des poudres et la préparation des polymères pour l'impression 3D. Ces appareils doivent être extrêmement précis, car il n'est possible de créer un revêtement nanoscopique sur chaque particule qu'en ajoutant l'agent de revêtement au mélange en doses infimes sous forme de solution faible ou de suspension.
L'intégration homogène d'agents d'enrobage dans des ingrédients en vrac implique de créer des niveaux d'humidité uniformes dans la poudre. Pour ce faire, chaque particule doit être mouillée. Si la phase liquide doit ensuite être séchée, l'enrobage doit rester uniformément réparti sur la surface de chaque particule. Idéalement, le processus de séchage se déroule sous vide, ce qui réduit la durée et la chaleur du processus.
amixon® offre des solutions testées sur le terrain pour relever ces défis de traitement complexes, en s'appuyant sur plus de 37 ans d'expérience. Notre équipement de mélange peut même mélanger de manière homogène 100 g de suie nanodispersive à 35 tonnes de poudres métalliques. Presque chaque équipement de traitement créé par amixon® est un prototype unique, en partie grâce à des détails minutieux mais décisifs, conçus pour répondre aux besoins de traitement spécifiques de nos clients issus de diverses industries. Nous proposons aux utilisateurs finaux des consultations approfondies avec nos ingénieurs de traitement, ce qui leur donne l'occasion de discuter de leurs critères de traitement spécifiques dans les moindres détails. Ces consultations, dont le contenu est protégé par des accords de confidentialité stricts, s'avèrent incroyablement profitables pour nos clients.