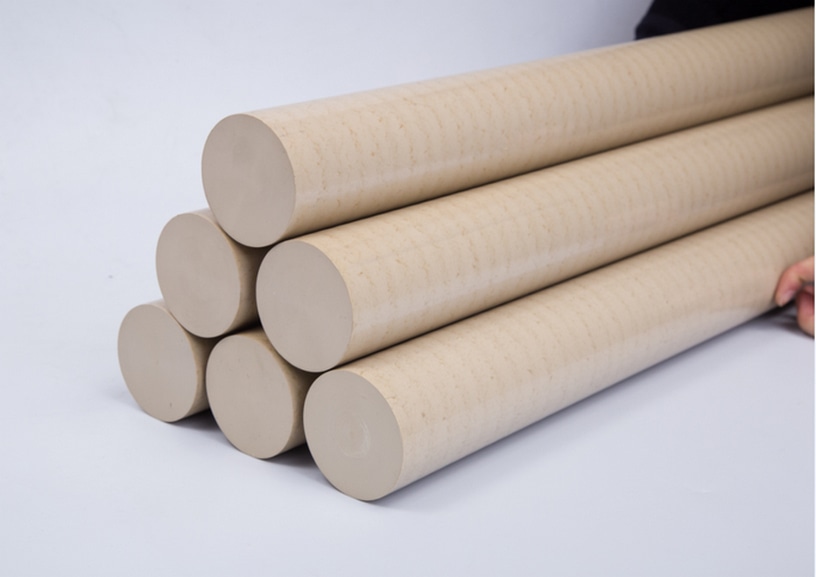
Voir la traduction automatique
Ceci est une traduction automatique. Pour voir le texte original en anglais cliquez ici
#Tendances produits
Usinage des tiges en PEEK - Principaux conseils
Caractéristiques et considérations relatives au traitement des barres en PEEK
Le PEEK est un plastique technique de haute performance qui présente de nombreux avantages significatifs par rapport aux autres plastiques techniques. Le PEEK possède d'excellentes propriétés telles que la résistance aux températures élevées, d'excellentes propriétés mécaniques, une bonne autolubrification, la résistance aux produits chimiques, l'ignifugation, la résistance au pelage, la résistance aux radiations, une isolation stable, la résistance à l'hydrolyse et la facilité de mise en œuvre.
Les barres de PEEK, également connues sous le nom de barres de polyéther-éther-cétone, sont des profils semi-finis extrudés à partir de matières premières de PEEK, qui présentent des caractéristiques telles que la résistance aux températures élevées, la résistance à l'usure, la résistance à la traction et la bonne ignifugation.
Applications des barres de PEEK :
Les barres de PEEK peuvent être utilisées pour fabriquer diverses spécifications de pièces en PEEK, adaptées aux composants mécaniques très demandés tels que les engrenages, les roulements, les sièges de vanne, les bagues d'étanchéité, les bagues d'usure de pompe et les joints.
Les pièces fabriquées à partir de barres de PEEK sont largement utilisées dans les connexions critiques des industries aérospatiale, médicale, des semi-conducteurs, pharmaceutique et alimentaire.
Quatre caractéristiques des matériaux PEEK :
1, le plastique PEEK présente un faible taux de rétraction pendant le moulage par injection, ce qui permet de contrôler la plage de tolérance dimensionnelle des pièces moulées par injection en PEEK, d'où une plus grande précision dimensionnelle par rapport aux plastiques courants.
2. Faible coefficient de dilatation thermique, d'où des variations dimensionnelles minimales avec les variations de température (dues aux changements de température ambiante ou à la chaleur de frottement générée pendant le fonctionnement).
3. une bonne stabilité dimensionnelle, c'est-à-dire la capacité des produits en plastique à conserver leur stabilité dimensionnelle pendant l'utilisation ou le stockage. Cela est dû au fait que l'énergie d'activation des molécules de polymère augmente, entraînant un certain degré d'enroulement des segments de chaîne.
4. Résistance exceptionnelle à l'hydrolyse thermique. Le PEEK absorbe très peu d'eau dans des environnements à température et à humidité élevées, contrairement aux plastiques courants tels que le nylon, qui subissent des changements dimensionnels importants en raison de l'absorption d'eau.
Questions à prendre en compte dans le traitement des barres de PEEK :
Le PEEK est également confronté à un défi commun aux matériaux polymères : l'élimination des contraintes moléculaires. La méthode générale consiste à chauffer après l'extrusion pour éliminer les contraintes moléculaires. Le réglage de la température du four est lié à la position et à la densité du matériau. Le contrôle du temps et de la température de cuisson est particulièrement crucial.
Après plusieurs jours de cuisson à différentes températures, la contrainte moléculaire des barres de PEEK est pratiquement éliminée, mais elle ne peut pas l'être complètement.
Par conséquent, les points suivants doivent être pris en compte lors de l'usinage du matériau :
1. En cas de transformation en tubes ou en joints d'étanchéité à l'aide de barres rondes, il convient de prêter attention au contrôle du perçage, notamment en sélectionnant la taille du foret, en s'assurant que le foret est suffisamment aiguisé et en contrôlant la vitesse de la machine-outil.
2. Lors du fraisage de la surface des barres rondes, il faut veiller à ne pas couper trop vite et à ne pas enlever trop de matière à la fois. Progressez graduellement et contrôlez correctement la vitesse.
3. En tenant compte des considérations ci-dessus lors du traitement des matériaux, il est possible d'éviter les problèmes inutiles et d'améliorer ainsi l'efficacité du traitement et le taux de qualification des produits.