
#Tendances produits
Robots Cleanroom pour la production médicale d‘urgence
Production médicale d’urgence : Stäubli s’engage
Au printemps 2020, l’épidémie de Covid-19 surprend la France, comme beaucoup d’autres pays. Trois entreprises industrielles, MGA Technologies, Infiplast SAS et le fabricant de robots Stäubli, ont reconnu le besoin, réagi rapidement et décidé de produire conjointement les filtres pour respirateurs grandement nécessaires.
PROBLÉMATIQUE
Fabrication d'un composant essentiel pour les respirateurs
En mars 2020, l’épidémie de Covid-19 surprend la France. Les hôpitaux français ne disposaient que de 5 000 respirateurs et il était évident qu'il y aurait bientôt une pénurie flagrante de consommables, notamment de filtres pour respirateurs. MGA Technologies, fabricant de machines sur mesure, a proposé au gouvernement de constituer un stock d’Etat de filtres pour respirateurs pour plusieurs mois, voire plusieurs années.
Infiplast, une société de plasturgie pour dispositifs médicaux, est sollicitée pour produire une pièce critique du respirateur : le boîtier contenant le filtre HME (échangeur de chaleur et d’humidité). Pour répondre rapidement à la demande de l’Etat, Infiplast a dû mettre en œuvre une chaîne de fabrication dédiée.
SOLUTION
Deux robots pour une cellule ultra performante
L’utilisation de la robotique était inévitable. Il était devenu évident que deux robots dédiés aux salles blanches (cleanroom), un modèle 4 axes et un modèles 6 axes, étaient nécessaires. Le bon fabricant a été rapidement et facilement identifié. En effet, Stäubli produit ses robots à proximité, à Faverges (Haute-Savoie), et propose des robots adaptés à la technologie médicale grâce à leur conception hygiénique.
Stäubli a immédiatement répondu à la demande de MGA Technologies et d'Infiplast. Les robots nécessaires ont été fourni en un temps record. Cela a permis de mettre en place l'ensemble du système, de la construction à la mise en service, en 10 semaines ; une prouesse puisque de tels projets prennent normalement au moins 24 semaines.
Deux robots Stäubli sont utilisés : un robot six axes TX2-90 et un modèle 4 axes de la nouvelle gamme SCARA TS2. Le premier récupère les différentes pièces plastiques composant le filtre en sortie de presse puis dispose la base du boîtier et son capot sur un plateau tournant. Après l’insertion de la mousse et de la membrane, le robot 6 axes assemble le boitier et le dispose sur le poste de soudure ultra-sons. Le SCARA TS2 positionne ensuite les boitiers pour les opérations finales de test et d’étiquetage. Il dirige ensuite les filtres conformes vers le conditionnement et dévie les autres vers les rebuts.
UTILISATION DU CLIENT
Fabrication de filtres pérenne, sûre et hautement productive
Intégrée à la mi-juillet dans la chaîne de production d’Infiplast, la cellule robotique a permis de constituer, au plus vite, le stock d’Etat de filtres HME pour les respirateurs des hôpitaux français. Grâce à un temps de cycle ultra court, un filtre est assemblé en quelques secondes. La fabrication des filtres est désormais pérennisée et les capacités sont suffisantes pour fournir des filtres au niveau international. De plus, le système d'assurance qualité intégré à la cellule garantit une production zéro défaut.
Un autre avantage de ce système compact, qui n’occupe que huit mètres carrés de surface au sol, profite aux employés : la réalisation des tâches répétitives par les robots évite notamment les troubles auditifs émis lors du soudage par ultrasons.
Les filtres Infiplast sont distribués sous la marque PROPIUM. Ils contiennent une membrane qui empêche la contamination croisée entre le patient et le respirateur, associée à une mousse humidifiant l’air insufflé dans les poumons du patient.
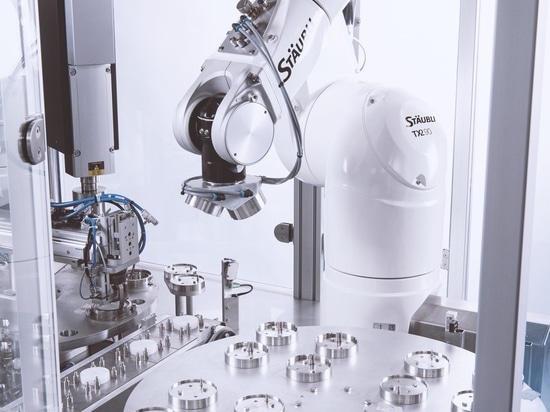