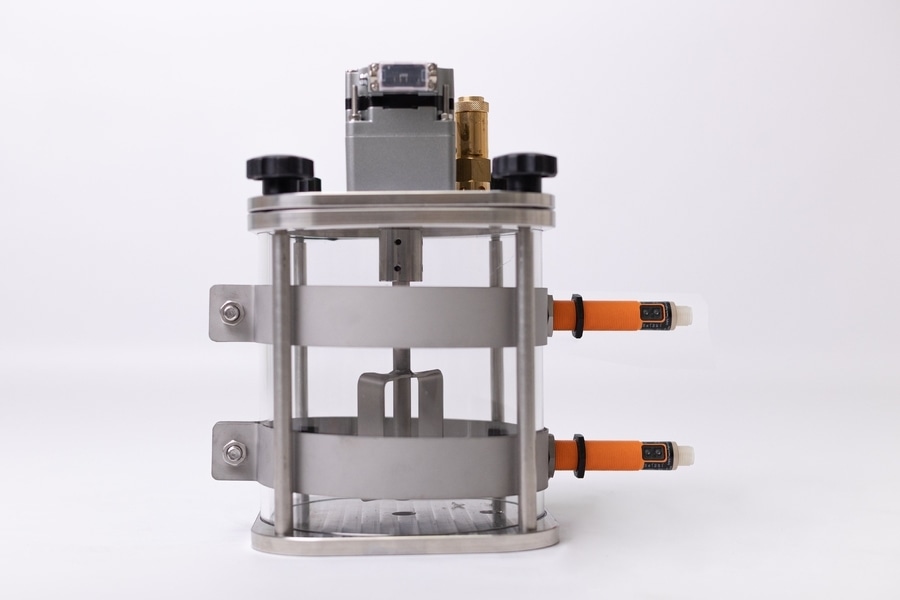
Voir la traduction automatique
Ceci est une traduction automatique. Pour voir le texte original en anglais cliquez ici
#Tendances produits
{{{sourceTextContent.title}}}
Créer de nouveaux processus de production avec les Compagnons du Devoir
{{{sourceTextContent.subTitle}}}
Réduire le coût de la production de fluides biomédicaux
{{{sourceTextContent.description}}}
Les Compagnons du Devoir et du Tour de France sont l'une des plus anciennes organisations d'artisans du monde. À l'instar des compagnons allemands (Wandergesellen), les apprentis ingénieurs doivent parcourir la France pour apprendre auprès des maîtres de leur métier. Pour participer, les apprentis doivent être titulaires d'un certificat d'aptitude professionnelle, équivalent à un NVQ de niveau 2 ou 3 au Royaume-Uni.
Nous avons été chargés d'aider les maîtres et les apprentis ingénieurs à développer un système de production complet qui transformerait les matières premières en un fluide biomédical. Le système pouvait être acheté auprès de fournisseurs d'équipements de laboratoire ou d'entreprises du secteur de la santé et de l'industrie pharmaceutique, mais il coûtait plus de 30 000 £. Le défi d'ingénierie consistait à concevoir le même système à partir de zéro, à un coût bien inférieur, afin de produire des résultats identiques, voire meilleurs.
Pour développer le processus de production à partir de zéro, les ingénieurs des Compagnons du Devoir ont dû concevoir le système, identifier le matériel clé, assurer la liaison avec les fournisseurs et créer l'automatisation et la programmation nécessaires pour créer ce fluide biomédical très complexe. La solution comprenait un processus de mélange en trois étapes, couplé à une étape de chauffage et à une étape de maintien final au cours de laquelle le fluide est maintenu en mouvement constant afin de conserver sa consistance, prêt à être distribué.
En travaillant avec les ingénieurs des Compagnons du Devoir, nous avons identifié que trois récipients sous pression transparents 2000ML-CTEL seraient la meilleure option pour leur application, car non seulement ils fournissent un environnement contrôlé pour le fluide, mais ils permettent également des contrôles visuels qui garantissent que tout changement minuscule dans la composition chimique peut être identifié et corrigé rapidement et efficacement.
Les produits chimiques bruts sont d'abord introduits dans le premier récipient sous pression transparent, qui est équipé d'un moteur électrique et d'un contrôleur SR-TEK, ainsi que d'un mélangeur à pales à ancre. Le processus automatisé mis au point par les ingénieurs des Compagnons du Devoir permet de varier précisément le mélange à différents moments pour obtenir le résultat souhaité. La flexibilité offerte par ce type d'installation est particulièrement appréciée par les équipes de R&D lorsqu'elles tentent de développer de nouveaux polymères ou fluides, car elle permet d'expérimenter et de savoir quelles variables doivent être fixées pour créer le résultat souhaité.
Une fois entièrement mélangé, le fluide est acheminé par des tuyaux vers un deuxième récipient sous pression transparent CTEL de deux litres, équipé d'un mélangeur à une seule pale, conçu pour maintenir le fluide en mouvement afin qu'il reste homogène. C'est à ce stade que la chaleur est appliquée pour poursuivre la polymérisation des matériaux.
Une fois traité, le fluide est ensuite envoyé dans une cuve de rétention finale équipée d'un autre mélangeur à lame d'ancrage à partir duquel il est distribué. Il est intéressant de noter que les trois cuves sont équipées de deux capteurs de niveau capacitifs haut et bas qui, lorsqu'ils sont reliés au contrôleur logique programmable (PLC), permettent d'automatiser l'ensemble du processus.
Le niveau de contrôle offert par ce type de système est de plus en plus populaire auprès des départements de R&D, car il signifie que les variables déterminées et fixées en laboratoire peuvent être mises à l'échelle et reproduites en production. Tout devient une science, une recette qui peut être prise et appliquée à n'importe quelle entreprise et environnement dans le monde pour produire le même résultat.
Le coût total du système complet était un tiers de celui de l'alternative commerciale toute faite. En outre, les ingénieurs des Compagnons du Devoir et du Tour de France disposent maintenant de composants de qualité de production qui peuvent être réutilisés et adaptés à de nombreux projets de recherche futurs, plutôt que d'une machine à usage unique.
Les appareils à pression transparents sont de plus en plus populaires parmi les équipes universitaires et de recherche, car ils permettent une démonstration claire des processus impliqués et un contrôle complet de l'environnement intérieur.
Pour en savoir plus sur la collaboration avec SR-TEK ou pour discuter de vos derniers besoins en matière d'applications, contactez Loris Medart, fondateur de SR-TEK, au 0044 (0) 20 8242 4853 / loris@sr-tek.com.