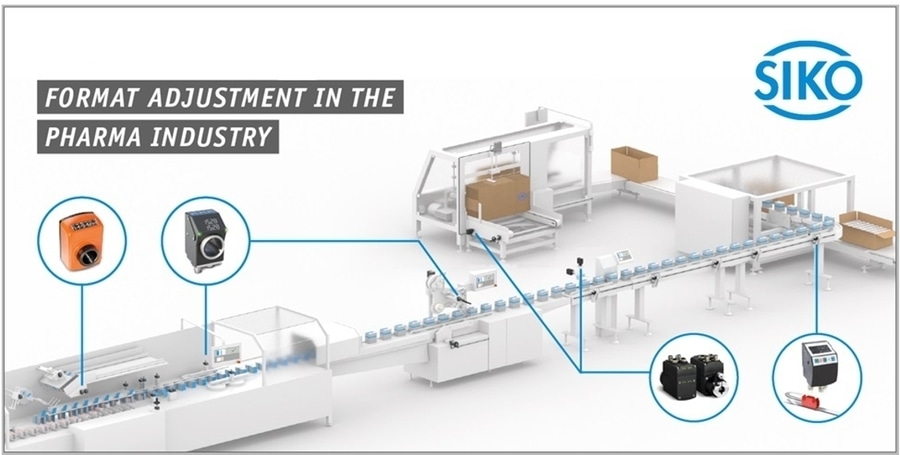
Voir la traduction automatique
Ceci est une traduction automatique. Pour voir le texte original en anglais cliquez ici
#Tendances produits
{{{sourceTextContent.title}}}
Pharma 4.0 avec changement de format intelligent
{{{sourceTextContent.subTitle}}}
SIKO présente des solutions pour optimiser les changements de taille
{{{sourceTextContent.description}}}
"Le changement de format" n'est pas nécessairement un terme qui suscite immédiatement l'attention dans l'industrie pharmaceutique. Cependant, compte tenu des défis de la fabrication pharmaceutique, qui se caractérisent par une pression sur les coûts et la concurrence ainsi que par des réglementations strictes, le changement de format intelligent est synonyme d'avantages concurrentiels en termes d'efficacité, de qualité des produits et de fiabilité des processus. Grâce à des solutions automatisées et en réseau, les entreprises pharmaceutiques peuvent faire un pas décisif vers Pharma 4.0.
Dans l'industrie pharmaceutique, le concept de centrage est pertinent, ce qui signifie que les réglages optimaux des machines doivent toujours être sélectionnés afin d'éviter les écarts inutiles dans le processus et donc une réduction de la qualité du produit. L'objectif est de mettre en réseau de manière optimale la fabrication, la technologie, la maintenance et l'acquisition de données électroniques afin d'exploiter au mieux l'efficacité des installations. En outre, la diversité croissante des produits et les tailles de lots de plus en plus petites dans la fabrication pharmaceutique exigent un haut degré de flexibilité des systèmes. C'est là qu'intervient le changement de format, qui peut être un facteur décisif pour la disponibilité des installations. Avec un changement de format optimisé, les temps de reconfiguration pour les changements de produits peuvent être considérablement réduits et la fiabilité du processus augmentée. SIKO GmbH, fabricant de capteurs et de systèmes de positionnement, a introduit différentes options pour le changement de format, des indicateurs de position purement mécaniques aux entraînements de positionnement entièrement automatisés
Avantages d'un changement de format optimisé
Dans la fabrication pharmaceutique, le changement de format a lieu partout, en particulier dans les processus d'emballage, d'étiquetage et d'inspection des produits. Chaque fois que les dimensions de la machine doivent être modifiées pour un nouveau produit, cela implique des changements de taille - que ce soit manuellement via une manivelle ou automatiquement via un actionneur.
Il faut toujours faire preuve de prudence lors de la modification des réglages de la machine, car des erreurs peuvent se glisser et avoir un effet négatif sur le résultat du produit. Le changement de format surveillé, voire automatisé, minimise le risque de réglages incorrects et peut rendre les processus plus flexibles. Les avantages d'un changement de format optimisé sont les suivants :
- une grande répétabilité, ce qui signifie que les médicaments sont toujours fabriqués avec la même forme et la même qualité
- des temps de reconfiguration plus rapides et donc une augmentation de la vitesse du processus
- une augmentation de l'efficacité et une réduction des coûts
- une augmentation de la fiabilité du processus, qui est un critère décisif dans la fabrication pharmaceutique
Une distinction est faite entre les changements de format manuels, contrôlés et automatisés. Le type de changement de format le plus approprié dépend des exigences : plus le nombre de formats à changer est élevé et plus la fabrication est exigeante du point de vue de la qualité - ce qui est généralement le cas dans le secteur pharmaceutique - plus il est judicieux d'utiliser des systèmes de positionnement surveillés ou automatisés
Changement de format manuel
Pour le changement de format manuel, on utilise des indicateurs de position mécaniques et électroniques qui indiquent la valeur réelle de la position actuelle. Ils conviennent aux machines de base avec des réglages peu fréquents. Les indicateurs de position SIKO mécaniques et numériques courants sont très précis, faciles à lire et sont configurés spécifiquement pour chaque application
Les indicateurs de position électroniques ont l'avantage, par rapport aux indicateurs mécaniques, d'être librement programmables et peuvent donc être utilisés avec une plus grande flexibilité. Des paramètres tels que le pas de la broche, les décimales, le sens de rotation, la position de montage ou l'utilisation en mode angle peuvent être configurés de manière pratique. Pratique : Les variantes mécaniques et électroniques sont compatibles pour l'installation, de sorte que la reconfiguration ou l'extension ne posent aucun problème.
Changement de taille contrôlé
Le changement de format surveillé est rendu possible par des indicateurs de position électroniques compatibles avec le bus et dotés de valeurs de consigne, qui sont intégrés dans le système de commande de la machine. Les valeurs réelles et théoriques sont échangées et comparées entre les différents indicateurs de position et l'unité de commande supérieure à l'aide d'un système de gestion des formules dans lequel toutes les variantes de produits sont stockées avec leurs valeurs de consigne sous forme de formules. Cela permet d'augmenter la sécurité du processus, car le système n'est redémarré que lorsque toutes les valeurs de consigne et les valeurs réelles des indicateurs correspondent. Les rejets ou les dommages aux parties du système sont ainsi évités. Le changement des axes est toujours effectué manuellement avec cette variante, tandis que le contrôle des réglages corrects est effectué électroniquement. La particularité des indicateurs de position électroniques réside dans les voyants lumineux qui affichent clairement l'état de la position à l'opérateur : Des feux verts pour "position correcte", des feux rouges signalent "position non correcte". En outre, l'écran comprend un indicateur de direction à flèche intégrée, qui indique dans quel sens le changement doit être effectué
Applications du changement de format contrôlé
Le changement de format surveillé peut être utile dans la fabrication de produits pharmaceutiques, par exemple, dans le cas de systèmes pour les machines d'encartonnage nécessitant des réglages fréquents ou dans le cas de l'étiquetage des produits. Un développement relativement nouveau est celui des systèmes "Track & Trace", qui exige que les médicaments sur ordonnance soient munis d'une étiquette claire et traçable. Cela implique une grande variété de processus tels que l'impression, la lecture, l'étiquetage et la pesée, et donc de nombreux réglages. La fiabilité des processus de ces systèmes est considérablement accrue par le changement de format surveillé.
Changement de format automatique
Lorsque le changement d'axe s'effectue sans intervention manuelle, on parle de changement de format automatique via des entraînements de positionnement compacts. L'actionneur, qui est mis en réseau avec le système de commande de la machine, se déplace directement dans la position requise. Avec l'automatisation, on obtient une nouvelle réduction significative des temps de reconfiguration. En outre, l'automatisation est utile si des parties du système difficiles d'accès doivent être ajustées fréquemment.
Un actionneur se caractérise par sa conception hautement intégrée, qui réunit tous les composants en un seul appareil : le moteur à courant continu sans balais (qui ne s'use pas), un réducteur puissant à faible jeu ainsi qu'un codeur de position et une électronique de puissance et de commande. L'intégration de l'actionneur dans les commandes de la machine ainsi que la communication avec les commandes sont facilement réalisables, notamment grâce à un grand nombre d'interfaces standard communes. Il s'agit notamment des interfaces Profibus ou Profinet conformes à Siemens, des interfaces série économiques telles que RS485 et CAN, IO-Link et des interfaces Ethernet industriel modernes.
Selon les exigences de l'application, différentes classes de puissance d'actionneurs sont nécessaires : des petits actionneurs à faible puissance pour un réglage fin dans un magasin de boîtes pliantes aux systèmes d'alimentation de grandes boîtes en carton où des agrégats entiers de la machine doivent être déplacés avec des actionneurs à couple relativement élevé
De plus, avec cette variante de changement de taille, la commande ne déclenche un redémarrage du système que lorsque l'échange de données de processus entre l'entraînement et la commande a abouti à une correspondance entre les valeurs réelles et les valeurs de consigne.
Maintenance prédictive
Une autre fonctionnalité de l'actionneur compact permet de tirer des conclusions sur l'état de fonctionnement de l'actionneur lui-même et du système : la capacité de diagnostic. En collectant et en surveillant divers paramètres de l'entraînement, tels que la consommation de courant dans le moteur, les valeurs de température ou de tension au niveau du circuit de commande et de charge, les irrégularités et donc la nécessité d'une maintenance peuvent être détectées à un stade précoce. Si les valeurs spécifiées sont dépassées, des mesures peuvent être prises immédiatement.
Conclusion : Plus d'automatisation, plus de données
Dans la fabrication pharmaceutique, le changement de format intelligent comporte plusieurs dimensions : il y a les effets directement mesurables tels que la réduction des temps de réglage, l'augmentation de la disponibilité de l'installation, l'accroissement de l'efficacité et l'amélioration de la fiabilité du processus. En outre, les solutions intelligentes permettent de réaliser ces processus secondaires de fabrication de la manière la plus discrète possible. Dans la mesure du possible, vous ne devriez pas avoir à vous soucier du changement de format ; s'il fonctionne bien et de manière fiable, vous pouvez vous consacrer à des activités essentielles et exigeantes telles que le dégagement de la ligne ou la documentation détaillée
Les composants périphériques tels que les indicateurs de position et les servomoteurs deviennent de plus en plus importants en raison de l'automatisation et de la numérisation croissantes. Les développements récents tels que les systèmes "Track & Trace" en sont la preuve. Des avantages supplémentaires tels que la collecte de données, l'autodiagnostic et la surveillance de la durée de vie des composants font du changement de format intelligent un élément crucial de Pharma 4.0.
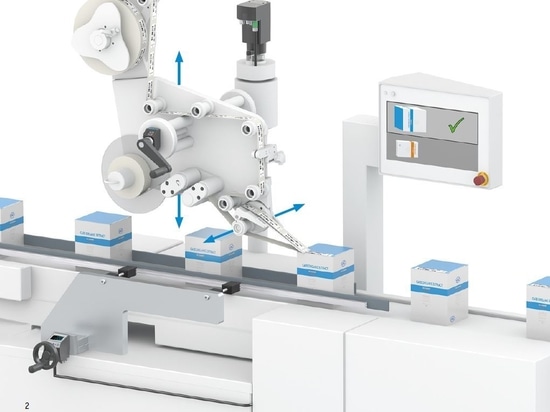
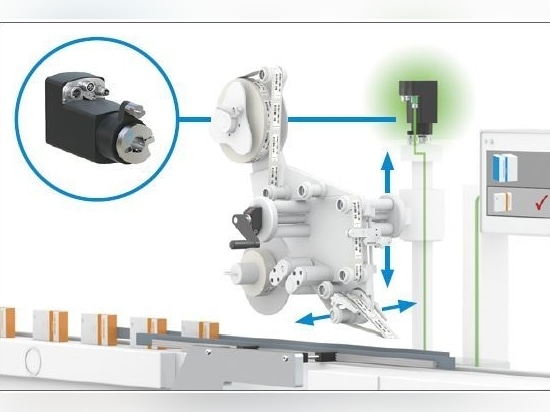
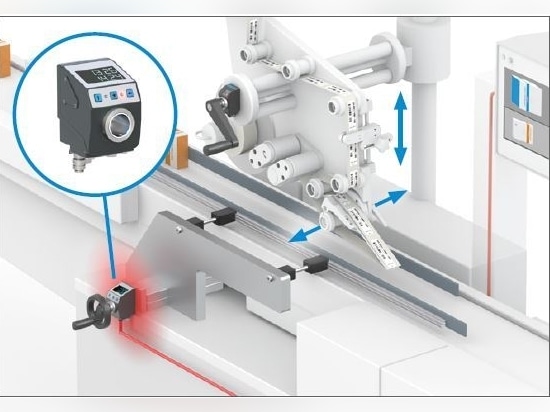
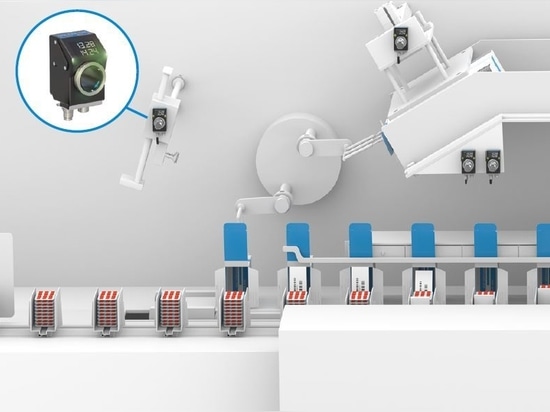
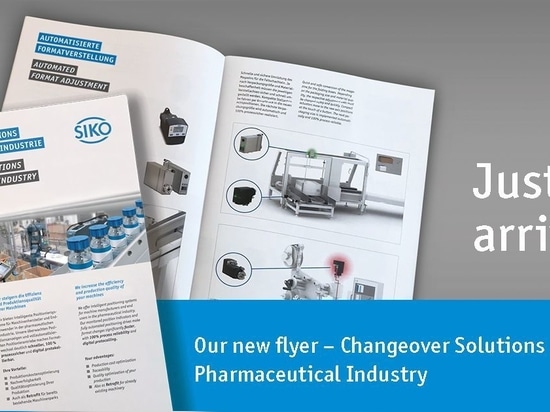