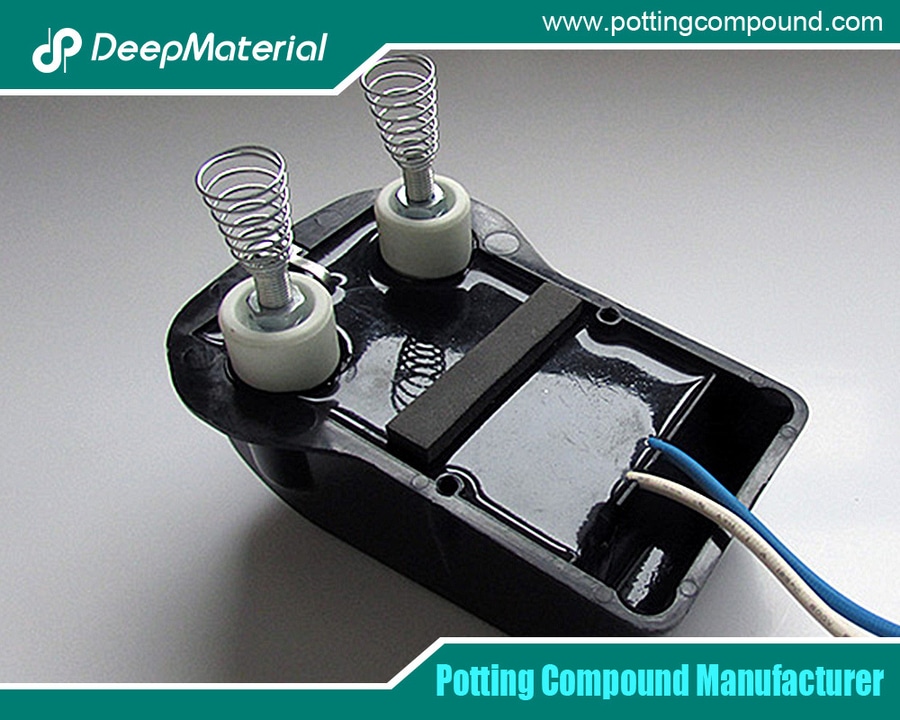
Voir la traduction automatique
Ceci est une traduction automatique. Pour voir le texte original en anglais cliquez ici
#Actualités du secteur
Composé d'empotage pour l'électronique : Un guide complet
Meilleure colle adhésive pour potting compound pour les fabricants d'électronique
Les composés de remplissage jouent un rôle crucial dans la protection et l'amélioration des composants électroniques. Ces matériaux, souvent appelés encapsulants, offrent divers avantages, notamment l'isolation, la protection contre les risques environnementaux et le soutien mécanique. Dans cet article, nous allons explorer le monde des composés d'enrobage pour l'électronique, en discutant de leurs types, de leurs applications, de leurs avantages et de leurs critères de sélection.
Qu'est-ce qu'un composé d'enrobage ?
Les composés d'enrobage encapsulent les composants électroniques et leur confèrent une couche protectrice. Ces composés sont généralement appliqués sous forme liquide, qui durcit ensuite pour créer une coque solide et durable autour des composants. La fonction première des composés d'enrobage est de protéger les assemblages électroniques de l'humidité, de la poussière, des produits chimiques et des chocs mécaniques, garantissant ainsi la longévité et la fiabilité de l'appareil.
Types de composés d'enrobage
Il existe différents types de composés d'enrobage, chacun ayant des propriétés uniques qui le rendent adapté à des applications spécifiques. Les types de composés d'enrobage les plus courants sont les suivants :
Les enrobés époxydiques
Les résines époxy sont parmi les composés d'enrobage les plus utilisés en raison de leur excellente résistance mécanique, chimique et thermique. Elles offrent une liaison solide avec divers substrats, ce qui les rend idéales pour les applications nécessitant une durabilité et une protection dans des environnements difficiles. Les composés d'enrobage époxy sont souvent utilisés dans l'électronique automobile, les commandes industrielles et les alimentations électriques.
Avantages :
Résistance mécanique élevée
Excellente résistance chimique
Bonne stabilité thermique
Forte adhérence à différents substrats
Inconvénients :
Temps de durcissement plus long
Il peut être cassant dans certaines formulations
Enrobés de polyuréthane
Les composés d'enrobage en polyuréthane sont connus pour leur flexibilité et leur ténacité. Ils offrent une excellente résistance à l'humidité et sont souvent utilisés dans des applications où les vibrations et les cycles thermiques posent problème. Les composés de polyuréthane sont couramment utilisés dans l'électronique grand public, l'éclairage LED et les applications automobiles.
Avantages :
Flexibles et résistants
Bonne résistance à l'humidité
Convient aux environnements sujets aux vibrations
Durcissement plus rapide que l'époxy
Inconvénients :
Résistance chimique inférieure à celle de l'époxy
Il peut ne pas convenir aux applications à haute température
Composés d'enrobage à base de silicone
Les composés d'enrobage à base de silicone sont appréciés pour leur stabilité thermique et leur flexibilité exceptionnelles. Ils peuvent résister à des températures extrêmes et sont souvent utilisés dans des applications où les fluctuations de température sont typiques. Les composés de silicone sont également connus pour leurs excellentes propriétés diélectriques, ce qui les rend idéaux pour les applications à haute tension.
Avantages :
Excellente stabilité thermique
Grande flexibilité
Bonnes propriétés diélectriques
Résistance à l'humidité et aux produits chimiques
Inconvénients :
Coût plus élevé que les autres composés d'enrobage
Temps de durcissement plus long
Composés d'enrobage acryliques
Les composés d'empotage acryliques offrent un équilibre entre flexibilité et dureté, ce qui les rend adaptés à un large éventail d'applications. Ils durcissent rapidement et sont faciles à appliquer. Ils sont souvent utilisés dans l'électronique automobile, les capteurs et les appareils grand public.
Ils sont souvent utilisés dans l'électronique automobile, les capteurs et les appareils grand public :
Durcissement rapide
Bon équilibre entre flexibilité et dureté
Résistant aux UV
Facile à appliquer
Inconvénients :
Faible résistance aux produits chimiques
Il peut ne pas convenir aux environnements à haute température
Applications des composés d'enrobage
Les composés d'enrobage sont utilisés dans une variété d'applications dans différents secteurs. Leur capacité à protéger et à améliorer les composants électroniques les rend indispensables dans les domaines suivants :
Électronique automobile
Les composants électroniques sont exposés à des environnements difficiles dans l'industrie automobile, notamment à des températures extrêmes, à l'humidité et aux vibrations. Les composés de remplissage protègent ces composants, garantissant leur fiabilité et leur longévité. Les applications comprennent les unités de contrôle du moteur, les capteurs et les systèmes d'éclairage.
Électronique grand public
Les composés de remplissage sont couramment utilisés dans l'électronique grand public pour protéger les composants sensibles de l'humidité, de la poussière et des dommages mécaniques. On les trouve souvent dans les smartphones, les tablettes, les appareils portables et les éclairages LED.
Contrôles industriels
Les environnements industriels sont souvent difficiles, avec une exposition aux produits chimiques, à l'humidité et aux contraintes mécaniques. Les commandes industrielles utilisent des composés d'enrobage pour protéger les composants électroniques sensibles de ces risques, assurant ainsi un fonctionnement continu et réduisant les temps d'arrêt.
Dispositifs médicaux
Les appareils médicaux exigent des niveaux élevés de fiabilité et de protection. Les composés d'enrobage sont utilisés dans l'électronique médicale pour protéger les composants de l'humidité, des processus de stérilisation et des chocs mécaniques. Les applications comprennent les équipements d'imagerie, les appareils de diagnostic et les systèmes de surveillance des patients.
Aérospatiale et défense
Les composants électroniques des applications aérospatiales et de défense sont soumis à des conditions extrêmes, notamment des températures élevées, des vibrations et des radiations. Les composés d'enrobage fournissent la protection nécessaire, garantissant la fonctionnalité et la fiabilité des systèmes critiques.
Avantages de l'utilisation des composés d'enrobage
Les composés d'enrobage dans l'électronique offrent plusieurs avantages, ce qui les rend essentiels à la conception et à la fabrication des produits électroniques modernes. Ces avantages sont les suivants
Protection de l'environnement
Les composés d'enrobage constituent une barrière solide contre les facteurs environnementaux tels que l'humidité, la poussière, les produits chimiques et les fluctuations de température. Cette protection est cruciale pour assurer la longévité et la fiabilité des composants électroniques, en particulier dans les environnements difficiles.
Support mécanique
Les composés de remplissage offrent un support mécanique aux composants électroniques, les protégeant des dommages physiques dus aux vibrations, aux chocs ou aux impacts. Ce support est essentiel dans les applications où les composants électroniques sont constamment en mouvement ou soumis à des contraintes.
Isolation électrique
L'une des principales fonctions des composés d'enrobage est d'assurer l'isolation électrique. En encapsulant les composants, les composés d'enrobage empêchent les courts-circuits et les défaillances électriques, garantissant ainsi un fonctionnement sûr de l'appareil.
Gestion thermique
Certains composés d'enrobage, tels que le silicone et l'époxy, ont une excellente conductivité thermique, ce qui permet de dissiper la chaleur générée par les composants électroniques. Cette gestion thermique est essentielle pour éviter la surchauffe et garantir le fonctionnement efficace de l'appareil.
Fiabilité améliorée
Les composés de remplissage améliorent considérablement la fiabilité des appareils électroniques en offrant une protection contre les facteurs environnementaux, les contraintes mécaniques et les défaillances électriques. Une fiabilité accrue se traduit par une diminution des pannes, une réduction de la maintenance et une durée de vie plus longue.
Choisir le bon composé d'enrobage
Le choix d'un composé d'enrobage adapté à votre application est essentiel pour atteindre le niveau de protection et de performance souhaité. Plusieurs facteurs doivent être pris en compte lors de la sélection d'un composé d'enrobage, notamment
Environnement de fonctionnement
L'environnement d'exploitation joue un rôle important dans la détermination du type de pâte à modeler à utiliser. Des facteurs tels que la plage de température, l'humidité, l'exposition aux produits chimiques et les contraintes mécaniques doivent être pris en compte lors de la sélection d'un composé.
Plage de température : les composés à base de silicone ou d'époxy sont recommandés pour les environnements à haute température en raison de leur stabilité thermique.
Humidité : les composés de polyuréthane sont idéaux pour les applications où la résistance à l'humidité est une priorité.
Exposition aux produits chimiques : les composés époxy offrent une excellente résistance aux produits chimiques et conviennent aux environnements chimiques difficiles.
Propriétés mécaniques
Les propriétés mécaniques du composé d'enrobage, telles que la dureté, la flexibilité et la résistance à la traction, doivent correspondre aux exigences de l'application.
Dureté : pour les applications nécessitant une protection rigide, les composés époxy sont idéaux.
Flexibilité : les composés de polyuréthane et de silicone sont flexibles, ce qui les rend adaptés aux applications soumises à des vibrations ou à des cycles thermiques.
Propriétés électriques
Les propriétés électriques du composé d'enrobage, telles que la rigidité diélectrique et la résistance d'isolation, sont cruciales pour les applications impliquant des tensions élevées ou des composants électroniques sensibles.
Rigidité diélectrique : les composés à base de silicone sont connus pour leurs excellentes propriétés diélectriques, ce qui les rend adaptés aux applications à haute tension.
Résistance à l'isolation : les composés époxydiques assurent une isolation solide, évitant ainsi les défaillances électriques.
Temps de durcissement
Le temps de durcissement du composé d'enrobage peut avoir un impact sur le processus de production. En fonction de l'application, un temps de durcissement plus rapide ou plus lent peut être préféré.
Durcissement rapide : les composés acryliques et polyuréthanes durcissent rapidement, ce qui les rend adaptés à une production en grande quantité.
Durcissement lent : les composés époxy et silicone peuvent nécessiter des temps de durcissement plus longs, ce qui peut s'avérer nécessaire pour des applications spécifiques nécessitant une liaison plus forte.
Considérations relatives au coût
Le coût est toujours un facteur à prendre en compte lors de la sélection des matériaux. Si les composés d'enrobage de qualité supérieure peuvent offrir de meilleures performances, ils sont également plus coûteux. Il est essentiel de trouver un équilibre entre les exigences de performance et les contraintes budgétaires.
Processus d'application des composés d'enrobage
Le processus d'application des composés d'enrobage est une étape essentielle pour garantir la protection et les performances des composants électroniques. Le processus comprend généralement les étapes suivantes :
Préparation
Avant d'appliquer la pâte d'enrobage, les composants électroniques et le boîtier doivent être soigneusement nettoyés pour éliminer les contaminants, tels que la poussière, les huiles ou l'humidité. Un bon nettoyage garantit une bonne adhérence et prévient les problèmes potentiels tels que les bulles ou les vides.
Mélange
Si le produit d'enrobage est un système à deux composants (par exemple, époxy ou polyuréthane), les composants doivent être soigneusement mélangés conformément aux instructions du fabricant. Un mélange précis est essentiel pour s'assurer que le composé durcit correctement et atteint les propriétés souhaitées.
Distribution
Le composé d'enrobage mélangé est ensuite déposé dans l'assemblage électronique à l'aide d'une seringue, d'un distributeur ou d'un équipement automatisé. Le processus de distribution doit être effectué avec soin afin d'éviter la formation de bulles d'air ou de vides, qui peuvent compromettre la protection et les performances du composé d'enrobage.
Durcissement
Après la distribution, le produit d'enrobage doit être durci conformément aux recommandations du fabricant. Selon le type de composé utilisé, le durcissement peut se faire à température ambiante ou à chaud. Un durcissement correct garantit que le composé possède toutes les propriétés mécaniques, thermiques et électriques.
Inspection
Une fois que le composé d'enrobage a complètement durci, l'assemblage doit être inspecté pour détecter les défauts, tels que les bulles d'air, les vides ou une couverture incomplète. Tout problème doit être traité rapidement afin de garantir la protection et les performances des composants électroniques.
Défis liés à l'enrobage des composants électroniques
Bien que les composés d'enrobage offrent de nombreux avantages, leur utilisation dans les applications électroniques pose des problèmes. Voici quelques-uns des défis les plus courants :
Bulles d'air et vides
Des bulles d'air et des vides peuvent se former au cours du processus de distribution ou de durcissement, compromettant la protection et les performances du composé d'enrobage. Pour minimiser ces problèmes, il est nécessaire d'appliquer des techniques de mélange, de dosage et de durcissement minutieuses.
Rétrécissement
Certains composés d'enrobage, en particulier les formulations époxy, peuvent se rétracter pendant le durcissement. Le rétrécissement peut entraîner des contraintes mécaniques sur les composants, ce qui risque de les endommager ou d'affecter leurs performances. Le choix d'un composé à faible retrait et le respect des procédures de durcissement appropriées peuvent contribuer à atténuer ce problème.
Inadéquation de la dilatation thermique
Les différences de dilatation thermique entre le composé d'enrobage et les composants électroniques peuvent entraîner des contraintes et des défaillances potentielles, en particulier dans les applications soumises à d'importantes fluctuations de température. Pour éviter ces problèmes, il est essentiel de choisir un composé d'enrobage dont le coefficient de dilatation thermique (CTE) est compatible.
Compatibilité avec les composants
Tous les composés d'enrobage ne sont pas compatibles avec tous les composants électroniques ou tous les types de substrats. Il est essentiel de s'assurer que le composé choisi ne réagit pas négativement avec les matériaux utilisés dans l'assemblage, par exemple en corrodant les métaux ou en dégradant les plastiques.
Retrait et réusinage
Une fois qu'un composé d'enrobage a durci, il peut être difficile, voire impossible, de l'enlever, ce qui complique les travaux de reprise ou de réparation. Dans les applications où l'on prévoit des retouches, il peut être utile de choisir un composé qui permet un retrait plus facile, comme un composé à base de silicone.
Innovations et tendances futures dans les composés d'enrobage
Le domaine des composés d'enrobage pour l'électronique est en constante évolution, poussé par la nécessité d'améliorer les performances, la durabilité environnementale et la compatibilité avec les technologies émergentes. Parmi les tendances et les innovations actuelles, on peut citer
Composés respectueux de l'environnement
Les préoccupations environnementales étant de plus en plus fortes, la demande de composés d'enrobage moins nocifs pour l'environnement s'accroît. Cela inclut le développement de résines biosourcées et de composés à teneur réduite en composés organiques volatils (COV).
Gestion thermique avancée
Avec l'essor de l'électronique de haute puissance, comme les véhicules électriques et les systèmes d'énergie renouvelable, il y a un besoin croissant de composés d'enrobage avec des propriétés de gestion thermique avancées. Les innovations en matière de matériaux thermoconducteurs contribuent à répondre à cette demande.
Composés d'enrobage intelligents
Les chercheurs étudient le développement de composés d'enrobage "intelligents" capables de surveiller les composants électroniques en temps réel. Ces composés pourraient inclure des capteurs qui détectent les changements de température, d'humidité ou d'autres facteurs environnementaux, ce qui permettrait une maintenance proactive et la prévention des pannes.
Les nanotechnologies
L'incorporation de nanomatériaux dans les composés d'enrobage est une tendance émergente qui offre la possibilité d'améliorer les propriétés mécaniques, thermiques et électriques. La nanotechnologie pourrait permettre de mettre au point des composés d'enrobage présentant des caractéristiques de performance supérieures, telles qu'une conductivité thermique accrue ou une résistance diélectrique améliorée.
Conclusion
Les composés d'enrobage pour l'électronique sont un élément essentiel de la protection et de la performance des appareils électroniques modernes. Avec une large gamme de matériaux disponibles, y compris l'époxy, le polyuréthane, le silicone et l'acrylique, il est possible de trouver un composé approprié pour presque toutes les applications. Les fabricants et les ingénieurs peuvent garantir la longévité, la fiabilité et l'efficacité de leurs assemblages électroniques en comprenant les propriétés, les applications et les critères de sélection des composés d'enrobage. Au fur et à mesure que la technologie évolue, les matériaux et les méthodes utilisés pour l'encapsulage évoluent également, ce qui permet de réaliser des innovations et des progrès encore plus importants dans le domaine de la protection électronique.
Pour en savoir plus sur le choix du meilleur composé d'empotage pour l'électronique : un guide complet, vous pouvez visiter le site DeepMaterial à l'adresse https://www.pottingcompound.com/ pour plus d'informations.