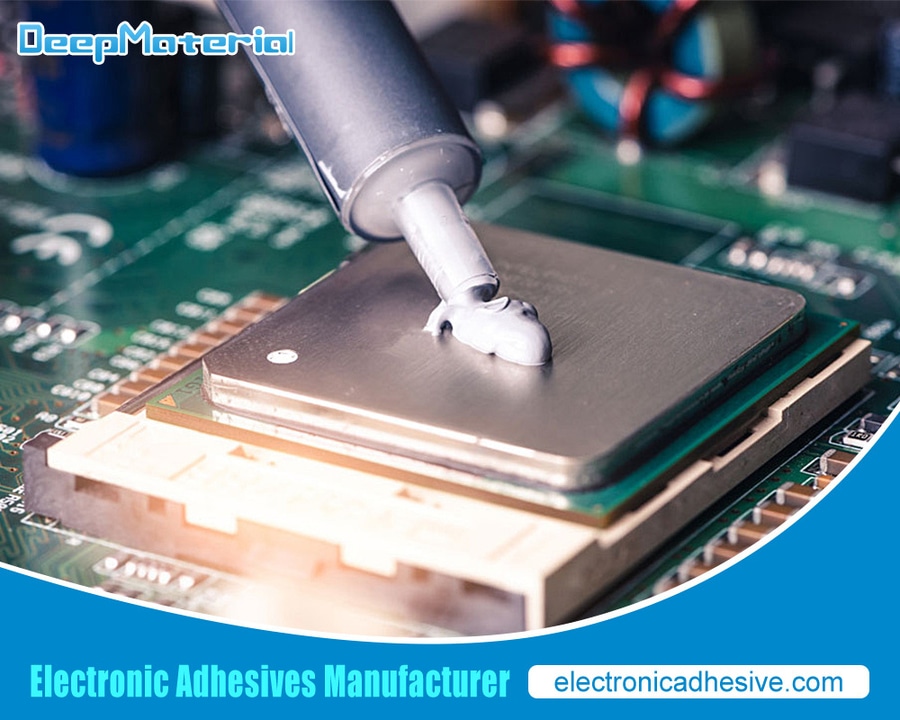
Voir la traduction automatique
Ceci est une traduction automatique. Pour voir le texte original en anglais cliquez ici
#Actualités du secteur
Amélioration de la fiabilité électronique : Le rôle de l'époxy non conductrice
Meilleure colle électronique améliorante Fabricant de colle électronique améliorante
La fiabilité est primordiale dans la fabrication électronique. Pour que les composants électroniques restent opérationnels dans diverses conditions, il faut prêter une attention méticuleuse aux détails de l'assemblage et des matériaux. L'époxy non conductrice apparaît comme un acteur essentiel dans ce paysage, offrant un mélange d'isolation, d'adhérence et de protection. Cet article se penche sur l'importance de l'époxy non conducteur dans l'électronique, en explorant ses propriétés, ses applications et ses contributions à la fiabilité des dispositifs électroniques.
Comprendre l'époxy non conductrice
L'époxy non conductrice est une résine époxy spécialisée conçue pour isoler les composants électroniques tout en offrant de solides propriétés d'adhérence. Composée d'une matrice polymère remplie de particules isolantes telles que la céramique ou la silice, la résine époxy non conductrice forme une barrière solide contre les courants électriques, l'humidité et d'autres facteurs environnementaux. Sa faible conductivité électrique garantit qu'il n'interfère pas avec les performances des circuits électroniques sensibles.
Principales caractéristiques et avantages
Isolation : L'époxy non conducteur crée une couche protectrice qui isole les composants électroniques, les protégeant des courts-circuits électriques et d'autres dommages potentiels.
Adhésion : Ses fortes propriétés d'adhérence permettent un collage sûr entre divers substrats, notamment les métaux, les plastiques et les céramiques, ce qui garantit un assemblage stable des dispositifs électroniques.
Résistance chimique : Résistant à une large gamme de produits chimiques, l'époxy non conducteur offre une protection à long terme contre les substances corrosives, améliorant ainsi la durabilité des assemblages électroniques.
Stabilité thermique : Grâce à son excellente stabilité thermique, il résiste aux fluctuations de température et conserve ses propriétés isolantes même dans des environnements difficiles.
Polyvalence : l'époxy non conductrice convient à diverses applications, notamment l'encapsulation, l'encapsulage, le collage et l'étanchéité dans des secteurs allant de l'automobile et de l'aérospatiale aux télécommunications et à l'électronique grand public.
Applications
L'époxy non conductrice est largement utilisée dans diverses applications électroniques, notamment :
Les cartes de circuits imprimés (PCB) : Ils encapsulent et enrobent les composants électroniques sur les circuits imprimés, offrant une isolation et un support mécanique.
Semi-conducteurs : L'époxy non conducteur encapsule les dispositifs semi-conducteurs délicats, les protégeant de l'humidité et des contraintes mécaniques.
Capteurs et instruments : Il est utilisé pour coller et sceller les capteurs et les dispositifs d'instrumentation, garantissant des performances fiables dans des conditions difficiles.
Eclairage LED : L'époxy non conducteur est utilisé dans l'encapsulation des LED pour améliorer la gestion thermique et protéger les composants des LED des facteurs environnementaux.
Considérations de sélection :
Lors du choix d'une résine époxy non conductrice pour des applications électroniques, plusieurs facteurs doivent être pris en compte :
Propriétés électriques : vérifier les capacités d'isolation électrique et la rigidité diélectrique de l'époxy pour s'assurer de sa compatibilité avec les exigences électroniques spécifiques.
Conductivité thermique : Évaluer la conductivité thermique de l'époxy pour éviter la surchauffe des composants enfermés, en particulier dans les applications à haute puissance.
Compatibilité chimique : confirmer la compatibilité avec les matériaux environnants et les conditions environnementales afin d'éviter toute dégradation ou défaillance au fil du temps.
Temps de durcissement et processus : Tenir compte du mécanisme de durcissement et des exigences de traitement pour optimiser l'efficacité de la production et les performances du produit.
Conformité réglementaire : Assurez-vous que l'époxy choisie est conforme aux normes et réglementations industrielles régissant les matériaux et composants électroniques.
Applications dans la fabrication électronique
L'époxy non conductrice pour l'électronique change la donne dans la fabrication électronique moderne, offrant une myriade d'avantages à différents stades de la production. Voici comment elle révolutionne l'industrie :
Agent de liaison polyvalent :
Dans l'assemblage des circuits imprimés, l'époxy non conductrice est un agent de liaison fiable pour les composants montés en surface.
Il garantit un placement sûr des composants tout en assurant une isolation électrique essentielle, en évitant les courts-circuits et en garantissant des performances optimales.
Encapsulation protectrice :
Les composants électroniques sensibles tels que les circuits intégrés et les capteurs nécessitent une protection solide.
L'époxy non conducteur agit comme une barrière protectrice, protégeant ces composants des contraintes mécaniques et des contaminants environnementaux, garantissant ainsi longévité et fiabilité.
Stabilité thermique :
La gestion de la chaleur est cruciale dans la fabrication de produits électroniques pour éviter la surchauffe et garantir des performances optimales.
La stabilité thermique de l'époxy non conducteur en fait un produit idéal pour les applications d'enrobage. Dans ces applications, il dissipe efficacement la chaleur générée par les composants électroniques, préservant ainsi leur efficacité et prolongeant leur durée de vie.
Durabilité accrue :
L'électronique est confrontée à divers défis environnementaux, des fluctuations de température à l'exposition à l'humidité.
L'époxy non conductrice améliore la durabilité en offrant une barrière résistante contre la pénétration de l'humidité, la corrosion et d'autres facteurs environnementaux, garantissant ainsi la longévité des appareils électroniques.
Processus de production rationalisés :
La facilité d'application et les propriétés de durcissement de l'époxy non conducteur permettent de rationaliser les processus de fabrication, réduisant ainsi les délais et les coûts de production.
Sa compatibilité avec les systèmes de distribution automatisés améliore encore l'efficacité, en permettant une application précise, même dans les environnements de production à haut volume.
Amélioration de la fiabilité
L'utilisation d'époxy non conductrice améliore considérablement la fiabilité des appareils électroniques. La prévention des courts-circuits électriques et des courants de fuite minimise le risque de dysfonctionnements ou de dommages causés par des circuits non intentionnels.
Prévention des courts-circuits électriques : L'époxy non conducteur agit comme une barrière, réduisant le risque de courts-circuits involontaires ou de dysfonctionnements.
Minimisation des courants de fuite : Un scellement efficace des composants électroniques élimine les risques de courants de fuite, ce qui garantit des performances stables et constantes.
Durabilité améliorée : L'application d'une résine époxy non conductrice permet aux appareils électroniques de résister aux facteurs environnementaux tels que les variations de température et l'humidité, ce qui prolonge leur durée de vie.
Confiance accrue dans les produits : Les fabricants peuvent livrer des produits électroniques avec une confiance accrue, sachant que le risque de dysfonctionnements ou de dommages dus à des problèmes électriques est considérablement réduit.
Applications polyvalentes : L'époxy non conducteur est utile dans divers assemblages électroniques, de l'électronique grand public à l'équipement industriel, offrant une solution fiable dans différents secteurs.
Solution rentable : L'investissement dans l'époxy non conducteur s'avère rentable à long terme en réduisant le besoin de réparations ou de remplacements dus à des défaillances électriques.
Progrès et innovations
L'époxy non conducteur pour l'électronique a fait l'objet de progrès et d'innovations remarquables, motivés par la nécessité de disposer d'appareils électroniques plus efficaces et plus fiables. À mesure que la technologie progresse, la demande de matériaux capables de résister à des exigences de plus en plus strictes s'intensifie. Voici un aperçu de l'évolution de l'époxy non conducteur et des innovations passionnantes qui se profilent à l'horizon :
Principales avancées
Amélioration de la formulation : Les fabricants affinent continuellement les formulations pour améliorer les propriétés telles que la conductivité thermique, la force d'adhérence et le temps de durcissement. Ces perfectionnements garantissent que l'époxy non conducteur peut répondre aux exigences en constante évolution de l'électronique moderne.
Conductivité thermique améliorée : Les dernières formulations présentent une conductivité thermique supérieure, dissipant la chaleur plus efficacement et garantissant des performances optimales même dans des environnements à haute température. Cette avancée est cruciale pour le maintien de la longévité et de la fiabilité des appareils électroniques.
Force d'adhérence accrue : L'amélioration de la force d'adhérence garantit que l'époxy non conducteur forme des liaisons solides avec divers substrats, y compris les métaux, les plastiques et les céramiques. Cette amélioration contribue à la durabilité et à la stabilité globales des assemblages électroniques.
Temps de durcissement réduit : Des temps de durcissement plus rapides permettent de rationaliser les processus de fabrication, de réduire les coûts de production et d'améliorer l'efficacité. Des développements récents ont conduit à des formulations d'époxy non conductrices qui durcissent rapidement sans compromettre les performances ou la fiabilité.
Innovations à l'horizon :
Matériaux nanocomposites : Les matériaux nanocomposites représentent une avancée significative dans la technologie des époxy non conducteurs. Intégrant des renforts à l'échelle nanométrique, ces matériaux offrent des propriétés mécaniques, thermiques et électriques inégalées. Ils ont le potentiel de révolutionner la conception des appareils électroniques en permettant une plus grande miniaturisation et une meilleure fiabilité.
Propriétés sur mesure : les progrès futurs dans le domaine des époxy non conducteurs visent à adapter les propriétés du matériau aux exigences spécifiques de l'application. Cette personnalisation pourrait impliquer l'optimisation des formulations pour des conditions de fonctionnement particulières, telles que des températures extrêmes ou des environnements corrosifs, ce qui élargirait encore la polyvalence de ces matériaux.
Conclusion
Dans le paysage dynamique de la fabrication électronique, le rôle de l'époxy non conducteur ne peut être surestimé. Son mélange unique d'isolation, d'adhérence et de protection contribue de manière significative à la fiabilité et à la longévité des appareils électroniques. De l'assemblage des circuits imprimés à l'encapsulation des composants, l'époxy non conducteur est un catalyseur essentiel de l'innovation, garantissant que les produits électroniques répondent aux exigences d'un monde de plus en plus interconnecté. Alors que les progrès continuent à faire évoluer les matériaux et les processus, l'époxy non conducteur reste un allié indéfectible dans la poursuite de l'excellence électronique.
Pour en savoir plus sur l'amélioration de la fiabilité électronique : le rôle de l'époxy non conducteur, vous pouvez visiter le site DeepMaterial à l'adresse https://www.electronicadhesive.com/ pour plus d'informations.