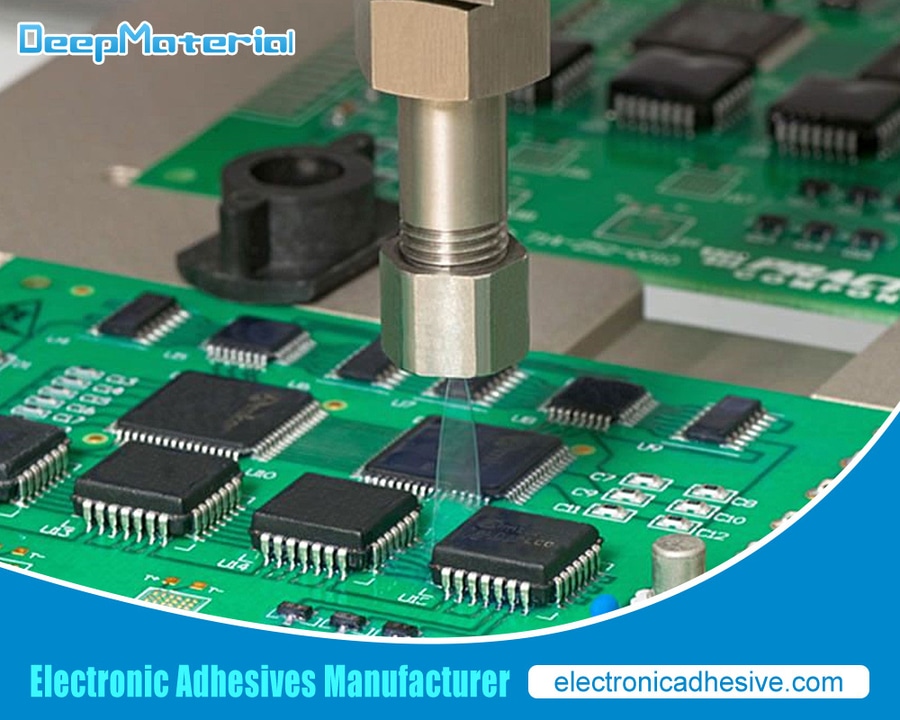
Voir la traduction automatique
Ceci est une traduction automatique. Pour voir le texte original en anglais cliquez ici
#Actualités du secteur
Comparaison des solutions adhésives industrielles : Epoxies vs. Acryliques vs. Silicones
Meilleur comparatif des colles industrielles Fabricant de colles industrielles
Les adhésifs industriels sont indispensables dans de nombreux secteurs, car ils constituent l'élément de base d'une myriade d'applications. Ces adhésifs sont méticuleusement conçus pour résister aux exigences rigoureuses des environnements industriels, garantissant des liaisons robustes et durables entre divers matériaux. Le choix d'une solution adhésive appropriée est primordial pour obtenir des performances et une durabilité optimales dans l'application envisagée.
Explorer les attributs et les utilisations des époxydes
Les époxydes constituent une catégorie de premier ordre d'adhésifs industriels, qui se distinguent par leur résistance et leur élasticité remarquables. Composés de deux éléments principaux, la résine et le durcisseur, les époxydes déclenchent une réaction chimique lors du mélange, qui aboutit à une liaison extrêmement solide. Leurs capacités d'adhésion supérieures facilitent le collage efficace d'un large éventail de matériaux, notamment les métaux, les plastiques, les céramiques et les composites.
La résistance des époxydes à la chaleur, aux produits chimiques et à l'humidité en fait un choix optimal pour les scénarios exigeant une durabilité et une fiabilité élevées. Leur application s'étend à diverses industries telles que l'aérospatiale, l'automobile, la construction et l'électronique. Dans l'industrie aérospatiale, par exemple, les époxydes jouent un rôle essentiel dans le collage des matériaux composites, ce qui permet d'obtenir des structures à la fois légères et capables de résister aux conditions de vol extrêmes.
Dans le secteur automobile, les époxydes sont utilisés pour coller les composants métalliques, produisant des pièces robustes et durables capables de supporter les rigueurs de la conduite. Dans l'ensemble, les époxydes sont un composant essentiel dans de nombreux processus industriels, grâce à leur résistance, leur durabilité et leur adaptabilité exceptionnelles. Elles constituent une solution de collage fiable pour un large éventail de matériaux dans des applications où des performances supérieures sont indispensables.
Les acryliques dans les adhésifs industriels : Avantages et limites
Les adhésifs acryliques sont largement utilisés dans l'industrie en raison de leur adaptabilité et de leur facilité d'utilisation. Ils sont réputés pour leur capacité à durcir rapidement, ce qui facilite le collage rapide et efficace des matériaux. Ces adhésifs font preuve d'une capacité louable à adhérer à un large éventail de matériaux, y compris les métaux, les plastiques, le verre et le bois. Par conséquent, les adhésifs acryliques se sont imposés comme une option privilégiée dans une myriade d'applications, allant de la fabrication automobile aux projets de construction.
L'un des principaux avantages des adhésifs acryliques réside dans leur résistance exceptionnelle aux chocs, aux vibrations et à l'épreuve du temps, ce qui les rend particulièrement adaptés aux scénarios exigeant flexibilité et endurance. Ces applications incluent le secteur aérospatial et la fabrication d'appareils électroniques. Néanmoins, il est impératif de reconnaître que les adhésifs acryliques peuvent présenter une résistance limitée aux températures élevées et aux environnements chimiques agressifs par rapport à d'autres formulations d'adhésifs.
Malgré ces contraintes, les adhésifs acryliques continuent d'être adoptés pour de nombreuses applications industrielles en raison de leur polyvalence inhérente et de leur processus d'application simple. Ils représentent une solution de collage fiable et efficace pour un large éventail de matériaux, ce qui confirme leur caractère indispensable dans divers domaines industriels.
Silicones : Une solution polyvalente pour le collage industriel
Les adhésifs silicones, qui se distinguent par leurs caractéristiques exceptionnelles, ont gagné en popularité dans le paysage des adhésifs industriels. Distincts des autres adhésifs, les silicones se distinguent par leur résistance à la température, leur souplesse et leurs capacités d'isolation électrique, ce qui leur confère une remarquable polyvalence applicable à un large éventail d'utilisations industrielles.
L'une des principales caractéristiques des silicones est leur tolérance exceptionnelle aux variations de température extrêmes, allant de -60°C à 300°C. Cet attribut en fait un choix exemplaire pour des secteurs tels que l'automobile, l'aérospatiale et l'électronique, où l'exposition à des conditions thermiques élevées est fréquente. En outre, les silicones présentent une résistance remarquable à l'humidité, aux rayons ultraviolets et aux expositions chimiques, ce qui les rend particulièrement adaptés aux applications en extérieur et aux environnements soumis à des conditions difficiles.
Comparaison entre les époxydes, les acryliques et les silicones : Principales différences
Les époxys, les acryliques et les silicones représentent trois catégories de matériaux fondamentalement différentes, chacune se distinguant par sa composition chimique, ses propriétés et son utilité dans diverses applications. Les époxydes sont réputés pour leur résistance et leur résilience inégalées, ce qui les rend exceptionnellement adaptés aux scénarios exigeant des capacités de charge importantes.
Elles sont largement utilisées dans les secteurs de la construction, de l'automobile et de l'aérospatiale pour les tâches de collage et d'étanchéité. En outre, leurs qualités exceptionnelles d'isolation électrique en font un choix privilégié pour la fabrication de composants électroniques.
Les acryliques se caractérisent par leur temps de durcissement rapide et leur flexibilité remarquable, ce qui en fait une solution optimale pour les projets nécessitant un assemblage ou une adaptabilité rapides. Ils jouent un rôle essentiel dans la production de marchandises en plastique, y compris les jouets, la signalisation et les articles de présentation. L'industrie automobile utilise les acryliques pour fabriquer des lentilles de phares et des couvercles de feux arrière, bénéficiant de leur clarté optique supérieure.
Les silicones se distinguent par leur résistance exceptionnelle aux fluctuations de température et leurs capacités d'isolation électrique, ce qui les rend idéaux pour les applications soumises à des températures extrêmes ou nécessitant une protection électrique. La fabrication de composants électroniques, tels que les puces électroniques et les circuits imprimés, fait souvent appel aux silicones en raison de ces propriétés. En outre, leur remarquable résistance aux intempéries est avantageuse dans le secteur de la construction pour l'étanchéité des fenêtres et des portes.
En résumé, les époxydes, les acryliques et les silicones possèdent chacun des propriétés distinctes qui les adaptent à des applications spécifiques. Il est essentiel de bien comprendre les différences entre ces matériaux pour choisir celui qui convient le mieux à une application donnée.
Solidité et durabilité : Choisir la solution adhésive optimale
En matière de résistance et de durabilité, les époxydes s'imposent souvent comme l'option privilégiée. Ils offrent des performances de collage supérieures et sont capables de supporter des charges et des contraintes importantes, ce qui en fait le candidat idéal pour les applications nécessitant un support robuste. Les acryliques offrent également une résistance et une durabilité respectables, bien qu'ils n'atteignent pas le même niveau de solidité que les époxydes dans certains cas. Inversement, les silicones présentent une résistance modérée mais se distinguent remarquablement par leur flexibilité et leur capacité à supporter des variations de température extrêmes.
Facilité d'utilisation : Analyse du processus d'application et de polymérisation
La simplicité d'utilisation d'une solution adhésive est fortement influencée par les exigences particulières de l'application en question. Les époxydes nécessitent généralement un mélange précis de la résine et du durcisseur et se caractérisent par des périodes de durcissement plus longues.
À l'inverse, les acryliques présentent l'avantage de durcir rapidement et d'être faciles à appliquer. De même, les silicones sont reconnus pour leur facilité d'application et leur rapidité de durcissement, ce qui en fait un excellent choix pour les projets exigeant un assemblage rapide ou des réparations rapides.
Conclusion
En résumé, il est essentiel de bien comprendre les caractéristiques et les utilisations des époxydes, des acryliques et des silicones pour identifier la solution adhésive industrielle la mieux adaptée à votre application. Grâce à une évaluation comparative de leurs avantages distincts en termes de solidité et de durabilité, de résistance aux températures et aux produits chimiques, de facilité d'application et de rentabilité, vous pourrez choisir en toute connaissance de cause l'adhésif qui présente le meilleur rapport qualité-prix pour vos besoins spécifiques.
Pour en savoir plus sur la comparaison des solutions adhésives industrielles : époxies vs. acryliques vs. silicones, vous pouvez visiter le site DeepMaterial à l'adresse https://www.electronicadhesive.com/ pour plus d'informations.