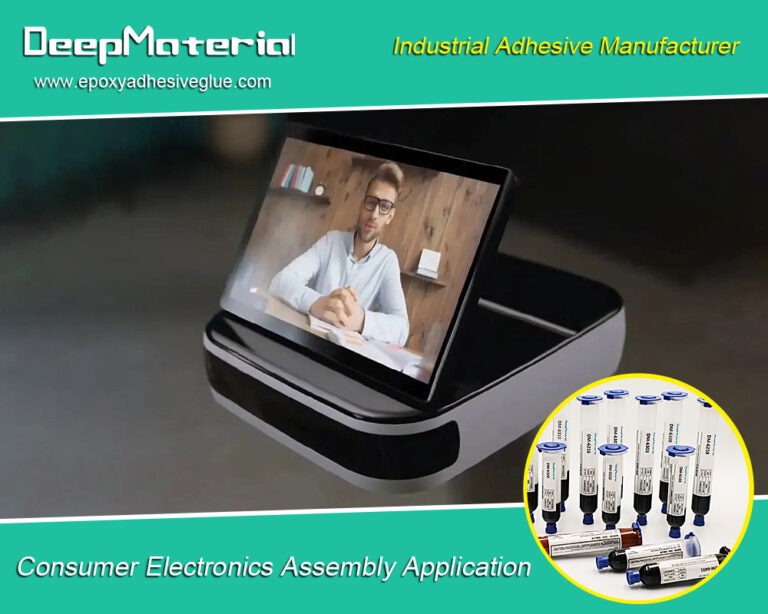
Voir la traduction automatique
Ceci est une traduction automatique. Pour voir le texte original en anglais cliquez ici
#Actualités du secteur
Les revêtements non conducteurs pour l'électronique peuvent-ils être utilisés pour des applications automobiles ou aérospatiales ?
Meilleur revêtement non-conducteur Colle adhésive pour l'électronique Fabricant
Quel que soit le secteur d'activité, il est absolument vital de protéger les composants électroniques délicats de l'usure extérieure. Les revêtements non conducteurs font de cette protection un impératif absolu pour les pièces soumises à des environnements difficiles, comme dans les secteurs de l'automobile et de l'aérospatiale.
Ils créent un bouclier contre l'humidité, les produits chimiques, les températures extrêmes et tout ce qui peut ternir leur qualité de fabrication ou nuire à leurs performances ! C'est cette couche supplémentaire de protection qui garantit la durabilité, la fiabilité et un fonctionnement optimal.
Avantages de l'utilisation de revêtements non conducteurs dans les industries automobile et aérospatiale
Les revêtements non conducteurs sont une bénédiction déguisée pour les industries automobile et aérospatiale. Tout d'abord, ils augmentent la durée de vie des unités électriques en formant une couche étanche à l'humidité, aux produits chimiques et aux éléments, en particulier dans les scénarios de fortes vibrations ou de changements de température. Les connexions sont ainsi protégées des courts-circuits ou de la corrosion, ce qui se traduit par des performances irréprochables à chaque fois !
En outre, l'utilisation de ces revêtements permet d'économiser l'argent qui aurait autrement été dépensé pour la maintenance ou les réparations ultérieures - un excellent moyen de contrôler les coûts sans compromettre la qualité. Et comme si cela ne suffisait pas, la réduction du nombre de remplacements est également synonyme de durabilité accrue dans les processus de production industrielle.
Les défis de l'électronique dans les environnements difficiles
Les composants électroniques utilisés dans les secteurs de l'automobile et de l'aérospatiale sont soumis à une véritable gageure. Du froid extrême à la chaleur torride, non seulement les composants se dilatent et se contractent - ce qui entraîne souvent des fissures de fatigue ou des ruptures sous contrainte - mais ils peuvent également être confrontés à des problèmes de contrôle de l'humidité, tels que la condensation, qui peut entraîner de la corrosion et des défaillances électriques.
Il faut également gérer le risque chimique, en particulier lorsqu'il s'agit de carburants, de lubrifiants ou d'autres substances potentiellement dangereuses ; il peut s'agir d'une dégradation subtile des pièces avant qu'elle ne se manifeste pleinement. N'oubliez pas non plus les vibrations !
Tous ces moteurs qui tournent à plein régime et les mouvements de transport font des ravages sur les composants électroniques si l'on n'y prend pas garde, et les chocs soudains dus aux impacts font que les composants électroniques délicats risquent de ne plus jamais se retrouver en un seul morceau.
Comment les revêtements non conducteurs protègent l'électronique des facteurs environnementaux
Les revêtements non conducteurs forment un bouclier solide autour des composants électroniques, les protégeant des dangers des facteurs environnementaux. Ils agissent comme de fidèles chevaliers pour protéger contre l'humidité ou les produits chimiques qui pourraient s'infiltrer et endommager les connexions électriques délicates.
Non seulement cette couche d'étanchéité peut stopper la corrosion ou les courts-circuits, mais elle agit également comme un isolant, régulant magistralement les températures extrêmes en réduisant le transfert de chaleur et en ajoutant une isolation contre les froids les plus intenses.
En outre, les revêtements non conducteurs offrent des propriétés d'absorption des chocs, c'est-à-dire qu'ils amortissent les vibrations et les secousses susceptibles de provoquer des défaillances mécaniques ou d'empêcher toute déconnexion due à une manipulation brutale.
Types de revêtements non conducteurs disponibles pour l'électronique
Lorsqu'il s'agit de protéger l'électronique des températures extrêmes, de l'humidité et des chocs dans les applications automobiles ou aérospatiales, plusieurs choix s'offrent à vous.
Les revêtements à base de silicone offrent une protection souple qui peut repousser les dommages chimiques et résister aux variations de température ainsi qu'aux mouvements de cliquetis. Les époxydes sont parfaits pour adhérer solidement aux objets. Ils résistent exceptionnellement bien à la chaleur et aux contraintes dues aux vibrations, ce qui les rend populaires dans les véhicules de l'ingénierie aéronautique.
Le polyuréthane présente une incroyable résistance à l'abrasion. Il s'agit donc d'un choix évident lorsque l'on recherche quelque chose d'élastique mais de durable. Il est parfait pour faire face à l'environnement difficile que l'on trouve dans une voiture ou un avion !
Mais supposons que la perfection absolue soit ce qui compte le plus. Dans ce cas, le revêtement au pérylène est votre compagnon : il est résistant à l'humidité et constitue une protection totalement étanche contre les composés d'autopsie, les flux temporels et les déchets de plomberie, ce qui les rend parfaits pour les niveaux les plus élevés d'électrodéfense dans les avions !
Facteurs à prendre en compte lors de la sélection d'un revêtement non conducteur pour des applications automobiles ou aérospatiales
Lors de la sélection d'un revêtement non conducteur pour les voitures ou les avions, il convient de prendre en compte un certain nombre d'éléments. Tout se résume à l'environnement auquel les pièces électriques seront exposées : les variations de température, les niveaux d'humidité, les produits chimiques et les vibrations ou les chocs doivent être pris en compte lors du choix du bon produit, afin qu'il puisse résister à ces situations et protéger vos composants électriques.
En outre, vous devez vous assurer que le matériau est compatible avec ce qui existe déjà dans ces systèmes ; sinon, vous perdez de l'argent : les essais de compatibilité devraient vous indiquer si ce revêtement réagira mal avec tout ce qui se trouve à l'intérieur.
De plus, il faut toujours penser aux méthodes d'application ; certains revêtements peuvent nécessiter un revêtement par pulvérisation, tandis que d'autres peuvent nécessiter un revêtement par immersion ou même un dépôt sous vide, en fonction de l'étendue de la zone à couvrir ou de la profondeur de la couche de protection souhaitée !
En fin de compte, le coût - à la fois à court terme, comme les coûts initiaux et l'équipement nécessaire, et à plus long terme, comme les coûts d'entretien - doit également être pris en considération.
En d'autres termes, faites d'abord vos recherches avant de choisir, car l'équilibre entre le coût et la performance vous permet d'en avoir pour votre argent.
Méthodes d'application des revêtements non conducteurs sur l'électronique
Les revêtements non conducteurs peuvent être appliqués à l'électronique par divers moyens, de la pulvérisation au pistolet ou au moyen d'un système automatisé à l'application par immersion, en passant par le dépôt sous vide, plus sophistiqué.
La peinture par pulvérisation est un choix très tendance, car elle recouvre tout d'une couche uniforme, quelle que soit la complexité de la forme de la surface. Le revêtement par immersion permet d'obtenir une uniformité et une précision, mais pour les composants délicats ou les structures complexes, il risque de ne pas faire l'affaire.
Si vous optez plutôt pour l'aspiration de cette couche, vous êtes sûr d'obtenir une épaisseur précise, quelles que soient les spécifications de votre équipement - pour autant qu'elles répondent à des critères précis tels que les niveaux de complexité et les exigences en matière de volume de production.
Il convient donc d'examiner attentivement chaque méthode avant d'en choisir une, en fonction de la tâche électronique que vous avez à accomplir, et de faire un choix judicieux.
Derniers mots
Le domaine des revêtements non conducteurs pour l'électronique, qui doit supporter les conditions les plus difficiles, est de plus en plus avancé jour après jour. La recherche et le développement ne cessent de revitaliser ces systèmes de protection, promettant des performances accrues ainsi qu'une durabilité plus longue.
Pour s'assurer que ce niveau de protection reste le plus élevé possible, de nouvelles technologies et de nouveaux matériaux sont constamment à l'étude, comme les nanotechnologies pour améliorer les barrières et la résistance à l'humidité, aux produits chimiques ou même aux températures extrêmes ! Si ces recherches aboutissent, cela pourrait signifier une défense prolongée pour l'électronique utilisée dans l'aviation et l'automobile.
En outre, l'efficacité des processus de revêtement connaît actuellement des améliorations significatives en raison des progrès réalisés dans leurs applications. Par exemple, les pulvérisateurs robotisés sont en plein développement pour garantir que les formes ou les surfaces complexes sont couvertes de manière précise et uniforme à chaque fois, ce qui permet de raccourcir les délais des procédures de revêtement tout en les rendant moins coûteuses !
Pour en savoir plus sur le choix du meilleur revêtement non conducteur pour l'électronique, vous pouvez consulter le site DeepMaterial à l'adresse https://www.epoxyadhesiveglue.com/category/epoxy-adhesives-glue/.