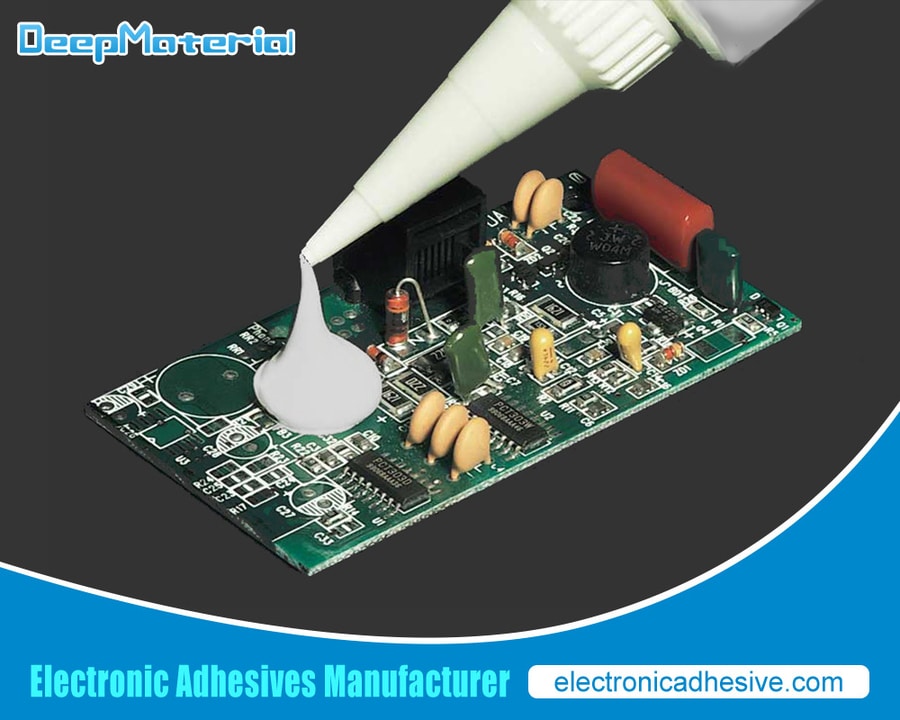
Voir la traduction automatique
Ceci est une traduction automatique. Pour voir le texte original en anglais cliquez ici
#Actualités du secteur
Le rôle du revêtement non conducteur pour l'électronique dans la prévention des défaillances électriques
Meilleur revêtement non conducteur pour les colles électroniques Fabricant de colle adhésive
Le revêtement non conducteur pour l'électronique, également appelé revêtement isolant ou revêtement diélectrique, est une couche protectrice qui empêche le flux d'électricité entre les composants. Il sert de barrière contre les courts-circuits électriques potentiels et autres dysfonctionnements susceptibles d'entraîner des défaillances catastrophiques du système.
Dans cet article de blog, nous allons nous pencher sur le rôle essentiel que jouent les revêtements non conducteurs dans la protection des appareils électroniques contre les défaillances électriques. Nous explorerons leur fonction, leur importance dans diverses applications et la manière dont ils contribuent à la longévité et à la fiabilité des systèmes électroniques.
Que vous soyez un passionné d'électronique, un étudiant en ingénierie ou un professionnel expérimenté dans ce domaine, ce guide complet vous apportera des informations précieuses sur le rôle méconnu des revêtements non conducteurs dans la prévention des défaillances électriques.
Comprendre les défaillances électriques en électronique
Les défaillances électriques dans l'électronique peuvent être causées par une variété de facteurs. L'une des causes les plus courantes est l'humidité, qui peut s'infiltrer dans les composants électroniques et provoquer des courts-circuits ou de la corrosion. La poussière et d'autres contaminants peuvent également s'accumuler à la surface des appareils électroniques et nuire à leur bon fonctionnement. En outre, les pannes électriques peuvent être dues à des dommages physiques, comme la chute de l'appareil ou son exposition à des températures extrêmes.
Ces défaillances électriques peuvent avoir un impact significatif sur les appareils électroniques. Elles peuvent entraîner des dysfonctionnements, une baisse des performances, voire une panne complète de l'appareil. Cela peut entraîner des réparations ou des remplacements coûteux, ainsi que des temps d'arrêt pour les entreprises qui dépendent de ces appareils pour leur fonctionnement.
Introduction au revêtement non conducteur pour l'électronique
Le revêtement non conducteur pour l'électronique est une couche protectrice appliquée à la surface des appareils électroniques. Il est conçu pour prévenir les défaillances électriques en constituant une barrière contre l'humidité, la poussière et d'autres contaminants. Ce revêtement est généralement constitué d'un matériau non conducteur, tel que le silicone ou l'acrylique, qui ne laisse pas passer l'électricité.
Le revêtement non conducteur crée une barrière protectrice entre les composants électroniques et l'environnement extérieur. Il empêche l'humidité de s'infiltrer dans l'appareil et de provoquer des courts-circuits ou de la corrosion. Il repousse également la poussière et les autres contaminants, ce qui permet à l'appareil de rester propre et à l'abri des interférences.
Comment le revêtement non conducteur prévient les défaillances électriques
Le revêtement non conducteur joue un rôle crucial dans la prévention des défaillances électriques des appareils électroniques. Il protège les appareils de l'humidité, de la poussière et d'autres contaminants susceptibles de provoquer des dysfonctionnements ou des dommages. En créant une barrière entre les composants électroniques et l'environnement extérieur, le revêtement garantit un fonctionnement fiable et efficace des appareils.
L'un des principaux moyens utilisés par les revêtements non conducteurs pour prévenir les défaillances électriques consiste à repousser l'humidité. L'humidité peut être une cause majeure de pannes électriques, car elle peut provoquer des courts-circuits ou de la corrosion. Le revêtement non conducteur crée une barrière étanche qui empêche l'humidité de s'infiltrer dans l'appareil et d'entrer en contact avec les composants électroniques.
En plus de repousser l'humidité, le revêtement non conducteur repousse également la poussière et les autres contaminants. La poussière peut s'accumuler à la surface des appareils électroniques et nuire à leur bon fonctionnement. En empêchant la poussière de se déposer sur l'appareil, le revêtement garantit que l'appareil fonctionne de manière optimale.
Types de revêtements non conducteurs pour l'électronique
Il existe plusieurs types de revêtements non conducteurs pour l'électronique. Chaque type a ses propres avantages et inconvénients, et le choix du revêtement dépend des exigences spécifiques de l'application.
Un type courant de revêtement non conducteur est le revêtement à base de silicone. La silicone est connue pour son excellente résistance à l'eau et sa durabilité, ce qui en fait un choix idéal pour protéger les appareils électroniques de l'humidité. Toutefois, les revêtements à base de silicone peuvent être difficiles à appliquer uniformément et nécessiter plusieurs couches pour une protection optimale.
Un autre type de revêtement non conducteur est le revêtement à base d'acrylique. Les revêtements acryliques sont connus pour leur excellente adhérence et leur flexibilité, ce qui les rend adaptés à un large éventail d'applications. Ils sont également faciles à appliquer et offrent une bonne protection contre l'humidité et la poussière. Toutefois, les revêtements acryliques peuvent ne pas être aussi durables que les revêtements en silicone et peuvent nécessiter une réapplication plus fréquente.
Les revêtements à base d'époxy sont une autre option pour les revêtements non conducteurs. Les revêtements époxy sont connus pour leur excellente adhérence et leur résistance chimique, ce qui les rend adaptés aux environnements difficiles. Ils offrent une bonne protection contre l'humidité, la poussière et d'autres contaminants. Toutefois, les revêtements époxydiques peuvent être plus difficiles à appliquer et nécessiter un équipement spécialisé.
Avantages de l'utilisation d'un revêtement non conducteur pour l'électronique
L'utilisation d'un revêtement non conducteur pour l'électronique présente plusieurs avantages. L'un des principaux avantages est qu'il peut prolonger la durée de vie des appareils électroniques. En protégeant les appareils de l'humidité, de la poussière et d'autres contaminants, le revêtement garantit un fonctionnement fiable et efficace pendant une période plus longue. Les entreprises peuvent ainsi réaliser des économies, car elles évitent des réparations ou des remplacements coûteux.
Un autre avantage de l'utilisation d'un revêtement non conducteur est qu'il peut améliorer les performances des appareils électroniques. En empêchant l'humidité et la poussière d'interférer avec le fonctionnement de l'appareil, le revêtement garantit un fonctionnement optimal. Cela peut être particulièrement important pour les appareils utilisés dans des applications critiques, comme les équipements médicaux ou les systèmes aérospatiaux.
Le revêtement non conducteur offre également un avantage esthétique en permettant aux appareils électroniques de rester propres et exempts d'empreintes digitales ou de taches. Cela peut être particulièrement important pour les appareils utilisés dans des applications grand public, comme les smartphones ou les tablettes. Le revêtement peut contribuer à préserver l'apparence de l'appareil et à améliorer l'expérience de l'utilisateur.
Processus d'application du revêtement non conducteur pour l'électronique
Le processus d'application d'un revêtement non conducteur pour l'électronique comporte généralement plusieurs étapes. La première étape consiste à préparer la surface de l'appareil électronique en la nettoyant soigneusement. Cela permet au revêtement d'adhérer correctement à la surface et d'assurer une protection optimale.
Une fois la surface nettoyée, l'étape suivante consiste à appliquer le revêtement. Plusieurs méthodes peuvent être utilisées à cet effet, telles que la pulvérisation, le brossage ou le trempage. La méthode spécifique dépend du type de revêtement ainsi que de la taille et de la forme de l'appareil.
Une fois le revêtement appliqué, il faut le laisser sécher ou durcir. Cela prend généralement un certain temps, en fonction du type de revêtement et des conditions environnementales. Il est important de suivre les instructions du fabricant en matière de séchage ou de durcissement afin de garantir une protection optimale du revêtement.
Réflexions finales
Le revêtement non conducteur pour l'électronique joue un rôle crucial dans la protection des appareils électroniques contre les défaillances électriques. Il empêche l'humidité, la poussière et d'autres contaminants d'interférer avec le fonctionnement des appareils, garantissant ainsi leur fiabilité et leur efficacité. En prolongeant la durée de vie des appareils électroniques et en améliorant leurs performances, le revêtement non conducteur constitue une solution rentable pour les entreprises comme pour les consommateurs.
Pour en savoir plus sur le rôle du revêtement non conducteur pour l'électronique dans la prévention des défaillances électriques, vous pouvez visiter le site DeepMaterial à l'adresse https://www.electronicadhesive.com/about/ pour plus d'informations.