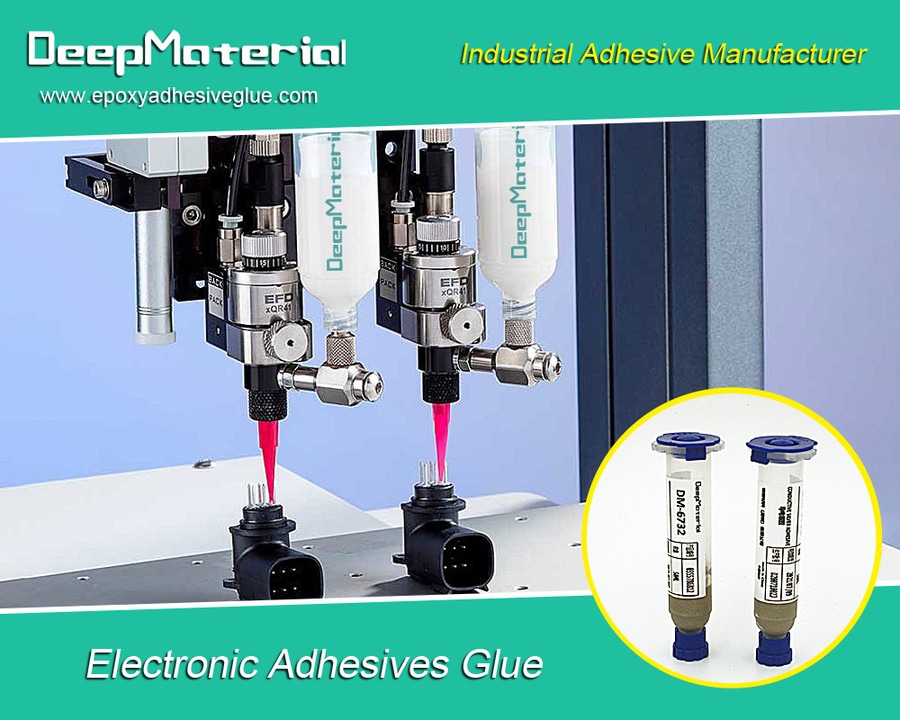
Voir la traduction automatique
Ceci est une traduction automatique. Pour voir le texte original en anglais cliquez ici
#Actualités du secteur
Epoxy en une partie vs époxy en deux parties -- Quelle est la meilleure colle époxy la plus forte pour coller du plastique abs sur du métal ?
Colle époxy la plus forte pour plastique ABS sur métal Fabricant
Les époxydes se distinguent par leurs performances et leurs applications.
Si vous êtes à la recherche d'un matériau polyvalent, vous n'avez pas besoin de chercher plus loin que les époxys.
Les époxydes sont utilisés depuis les années 1950, mais ils deviennent de plus en plus importants en raison de leur flexibilité inépuisable et de leurs caractéristiques de haute performance. Les époxydes sont les matériaux polymères les plus couramment utilisés pour les mastics, les adhésifs, les revêtements, les encapsulations, les enrobages et les imprégnations. Ils sont disponibles sous forme de liquides semi-durcis, de pâtes, de films et de solides et sont imperméables à l'humidité, à l'huile et à divers solvants.
Meilleur fabricant d'adhésifs électroniques (17)
Ils sont polyvalents dans leurs applications et leurs performances. Leurs caractéristiques les plus recherchées sont leur grande force d'adhérence et leur compatibilité avec divers substrats, des plastiques non traités aux élastomères. La seule chose qu'ils ne peuvent pas faire, c'est se lier au plastique. De nombreuses personnes commettent une erreur dans ce domaine. Si l'on parvenait à joindre le plastique, on obtiendrait quelque chose de tout à fait exclusif
Les époxydes sont également solides en termes de résistance au cisaillement et à la traction, mais leur résistance au pelage est faible. Il est toutefois possible d'améliorer la résistance au pelage en modifiant la formulation à l'aide d'un polymère plus robuste ou de charges différentes.
Personnalisation des époxys avec des charges
Les époxydes peuvent être modifiés avec des charges, des pigments et d'autres résines afin d'obtenir la gamme la plus variée de viscosités, d'effets et de propriétés physiques. Les charges sont généralement des substances inorganiques. Certaines substances inorganiques telles que le cuivre ou l'argent permettent d'utiliser l'époxy pour transférer l'électricité. Les charges d'oxyde facilitent la conduction de la chaleur. Les charges de fibre de verre offrent une grande résistance et peuvent supporter des micro-ballons. Elles assurent également une isolation thermique et électrique de faible densité. "On peut mettre n'importe quel matériau dans une résine époxy. Par exemple, il est possible de mettre de l'aluminium ou de l'acier inoxydable dans de l'époxy. Voici l'astuce. Si vous mélangez la charge de métal à une résine époxy, elle se transforme comme un métal.
Diverses charges sont aujourd'hui capables d'assurer la flexibilité et l'élongation. Il est courant que l'époxy ordinaire soit fragile. En cas de flexion, il ne dépasse généralement pas 10 % avant de se fissurer. L'ajout d'uréthane et d'acrylique permet d'améliorer l'élongation et la flexibilité. Cet aspect est crucial dans un contexte d'assemblage. De nombreux assembleurs souhaitent que la colle devienne aussi flexible que les substrats sur lesquels ils la collent.
Les assembleurs qui souhaitent ajouter des charges à leur époxy doivent opter pour une version monocomposante. Les charges ajoutées à une époxy monocomposante peuvent rendre le produit trop lourd. Selon les experts, l'époxy monocomposant peut être partiellement chargé. "En général, les versions les plus chargées sont les modèles à deux composants. Les versions monocomposantes peuvent devenir trop épaisses.
Applications de l'époxy
Les époxydes sont utilisés pour coller le bois et les métaux dans des applications structurelles très exigeantes. Parmi les applications de collage, on peut citer les portes et les capots d'automobiles, les composites aérospatiaux, les batteries, les composants électroniques, les rouleaux de peinture, les équipements sportifs et la quincaillerie. Les époxydes font également partie des plastiques les plus couramment utilisés dans le secteur de l'électronique. Elles sont utilisées à des fins d'intégration, comme pièces moulées, et pour la fabrication de composants laminés pour les cartes de circuits imprimés. "Les époxydes sont utilisés par divers fabricants de boîtiers électriques comme composés d'enrobage pour réduire les vibrations dues aux chocs. Les époxy à deux composants étant très élastiques, ils conviennent parfaitement à l'enrobage des pièces. L'époxy peut absorber les vibrations et les chocs. Toutefois, il peut également être modifié pour devenir conducteur électrique.
Deux composants ou un seul : quelle est la différence ?
Avant qu'un assembleur ne commence à réfléchir au type d'époxy à choisir - un composant ou l'autre - il doit d'abord connaître les principales différences entre les deux types d'époxy.
Les époxydes monocomposants peuvent être utilisés directement à partir du tube. Elles ne nécessitent ni mélange, ni dosage, ni dégazage. En revanche, elles nécessitent de la chaleur pour durcir. Les modèles monocomposants ont un initiateur, l'élément chauffant qui est contenu dans la résine. L'époxy nécessite un four ou un dispositif de chauffage pour obtenir une polymérisation complète. Les temps de polymérisation typiques sont de 30 à 60 minutes à 350-400 F. La résistance de la manipulation peut être augmentée rapidement par une polymérisation par induction. Le temps de polymérisation est généralement de 6 secondes à 325-425 F. Cependant, il est essentiel de suivre la fixation par induction pour permettre à l'époxy de cicatriser complètement. Les époxydes durcissant à la lumière ultraviolette sont disponibles en version monocomposant.
Les époxydes à deux composants sont les plus populaires. Tout d'abord, l'utilisateur doit mélanger la résine avec un durcisseur époxy. Les durcisseurs déclenchent la polymérisation nécessaire au durcissement. Si les deux sont combinés mécaniquement ou manuellement, la réaction exothermique se produit lorsque les molécules commencent à se réticuler.
Les versions à deux composants sont un peu plus résistantes que leurs homologues à un composant en raison de leurs propriétés de durcissement uniques. "Il y a des réactions chimiques entre la résine et le durcisseur, ce qui donne un produit plus important que l'un ou l'autre pris isolément. Les époxydes à deux composants sont durcis à la température ambiante ou à des températures plus élevées. En fonction de l'agent de durcissement utilisé, elles peuvent être fixées dans les 5 à 8 heures. Les époxydes les plus populaires se solidifient en deux ou trois heures à température ambiante. Un additif de catalyseurs peut être ajouté pour accélérer la réaction entre la résine et le durcisseur.
Toutes les résines époxydes doivent durcir pendant cinq à sept jours à température ambiante avant d'être testées.
Choisir le bon type
Les époxydes à deux composants permettent aux assembleurs d'assembler presque tout. "Lorsque vous touchez quelque chose à l'aide de deux composants, vous créez une puissante réaction chimique. C'est pourquoi vous êtes susceptible de posséder de meilleures propriétés physiques. Au fil du temps, les époxydes à un composant se sont améliorés.
Les époxydes monocomposants conviennent bien aux chaînes d'assemblage ou à d'autres zones où les utilisateurs placent une goutte d'époxy sur un composant du processus d'assemblage où deux composants d'un assemblage sont assemblés. La pièce assemblée est ensuite soumise à une source de chaleur pour le processus de durcissement. Les époxydes monocomposants sont plus pratiques à utiliser dans une installation de fabrication d'origine, car il n'est pas nécessaire de les mélanger. Le mélange et le dosage étant supprimés, le nombre de rejets peut être réduit en raison d'un mauvais rapport entre la résine et le durcisseur. La société utilisait de l'époxy à deux composants pour assembler des pièces peintes. Les pièces peintes sont soumises à un processus de séchage au four. Après avoir observé notre approche, nous avons modifié la formule de l'époxy à deux composants en une époxy à un composant. Comme le processus d'assemblage comportait déjà une étape de séchage au four de la peinture, le chauffage permet de durcir l'époxy en même temps. Cela a permis à l'entreprise d'éviter de mélanger deux pièces.
Selon les faits, le choix de l'un ou l'autre dépend de l'application particulière. "L'avantage d'une résine époxy monocomposante est qu'il n'est pas nécessaire de la mélanger avec d'autres composants. Si vous le placez dans la machine de distribution, il n'a pas besoin d'être rincé. L'inconvénient est qu'il faut chauffer le produit pour le durcir. L'avantage de l'époxy à 2 composants est qu'il durcit à température ambiante, ce qui signifie qu'il n'est pas nécessaire de le chauffer. L'inconvénient est qu'il faut la mélanger. Par conséquent, si vous avez un objet qui doit être chauffé ultérieurement pour en faire un autre usage, vous pouvez opter pour une résine époxy à un seul composant si vous le pouvez.
Meilleur fabricant d'adhésifs électroniques (12)
Pour plus d'informations sur l'époxy à un composant par rapport à l'époxy à deux composants - quel est le meilleur adhésif époxy le plus fort pour coller le plastique abs au métal, vous pouvez visiter DeepMaterial à https://www.deepmaterialcn.com/news/one-part-epoxy-vs-two-part-epoxy.html pour plus d'informations.