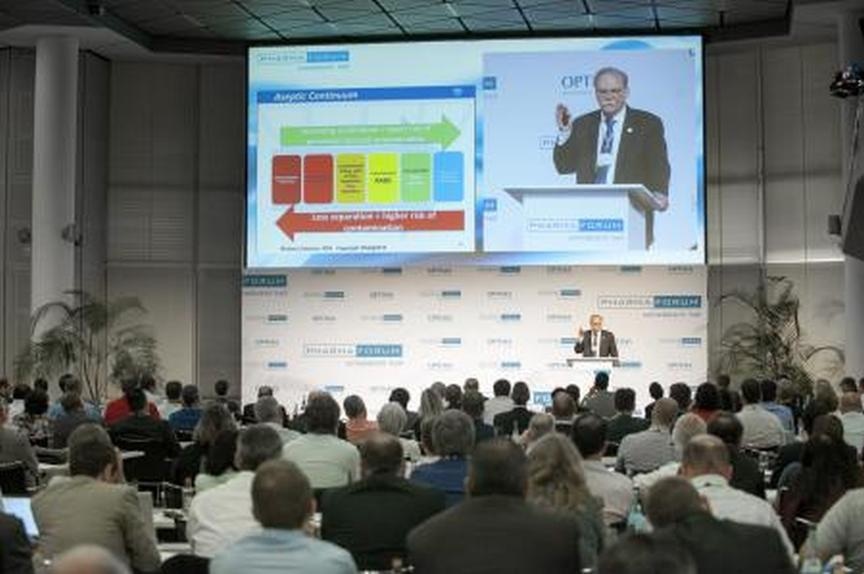
#Actualités du secteur
OPTIMA Annual Report – Another Increase in Revenue in 2016
OPTIMA Packaging Machines are in Great Demand
The 2016 business year ended with revenue of 340 Million Euro for the OPTIMA packaging group GmbH (Schwaebisch Hall). This surpassed the previous outstanding revenue in 2015 of 330 Million Euro. More than 80% of the OPTIMA packaging group’s revenue is generated abroad. Optima employs 2,150 people worldwide including 1,800 in Germany. The total number of employees represents a 100 person increase over the previous year. Optima is scheduled to invest approximately 50 Million Euro in expansion projects at the headquarters in Schwaebisch Hall.
In 2016 Optima generated an increase in revenue of 5% in the European market. However, the North American market had a slight decline. Hans Buehler, Optima’s Chief Executive Officer, commented: “Year after year major projects influence the country-specific revenue development. Therefore, those numbers need to be viewed as a moment in time. Optima’s revenue is in line with German industry standards. Estimates of the VDMA (Verband Deutscher Maschinen- und Anlagebau e.V. - Association of German Machine and Plant Manufacturing e.V.) forecasts an increase of 3% to 6.47 Billion Euro for the German packaging machine industry (source: VDMA and Federal Office of Statistics).
Optima’s generation of a 120 Million Euro revenue surplus over the past five years along with the positive industry outlook encourages Optima to invest. Within the next five year’s new buildings will be erected and existing space in Schwaebisch Hall expanded. “Several divisions will profit from this investment. Central administration, the logistics department, parts manufacturing and the Optima Pharma division are included in the building projects. This will prompt more efficient processes for the entire company, for example more effective internal logistics and will also create room for additional growth,” explained Hans Buehler. The approval process for these projects is currently under way.
Approximately 1,550 of the 2,150 employees worldwide work in Schwaebisch Hall. Optima has 13 locations with a total of 350 employees abroad. Especially in Germany new job opportunities were created including 50 positions in Schwaebisch Hall. Optima has more than 155 trainees worldwide with the majority of them located in Schwaebisch Hall.
Job Satisfaction and More
“In the last several years Optima implemented many new initiatives designed to promote a family-friendly workplace and a focus on health and wellness,” said Hans Buehler. Optima employees benefit from a flextime model, systematic human resource development, an engagement process with retirees and employees during family leave, wellness days and fitness events. Additional measures like the introduction of a company health management plan are in preparation.
In August 2016 Optima received the “berufundfamilie” (job and family) certificate for its family and life-phase personnel human resource development. The news magazine “Focus” considered Optima among the “Top National Employers” this year. Among the machine manufacturing companies Optima ranked within the top 20. The comparison is based on data from more than 100,000 employees.
2016 - A Year of Exciting Events
In July 2016, R+E Automation Technology (Fellbach) became part of the Optima group. R+E Automation Technology manufactures conveyor solutions and specialty machinery. The addition of this company provides Optima with a fourth location in Germany. Optima Pharma in Mornshausen (located near Marburg) is specialized in the manufacturing of pharmaceutical freeze dryers. METALL+PLASTIC in Radolfzell produces isolators and additional applications for the pharmaceutical industry for sterile applications. Schwaebisch Hall represents all four divisions: Optima Consumer, Optima Nonwovens, Optima Life Science and Optima pharma. The group has 13 subsidiaries abroad.
In 2016 Optima participated in the creation of the Virtual Reality (VR) Center that is managed by the Packaging Valley Germany e.V. in Schwaebisch Hall. The VR Center supplies meeting rooms and training capabilities for customers on virtual models which can include all details of a machine project before the machine is even built. Virtual reality, with all its capabilities, is considered the key technology of the future. Optima believes that the VR Center will promote new innovations and new developments and will provide an even more efficient method to work with customers.
More than 200 international visitors from 25 countries visited the Pharma Forum in Schwaebisch Hall. The two-day event takes place every third year by invitation from Optima Pharma. Outside of individual company boundaries, experts from the pharmaceutical industry share news about industry-specific subjects. In the past year, Optima participated in more than 50 shows worldwide.
Technology - The Future Starts Now
Optima will debut its “Mission Total Care” initiative at Interpack 2017 in Dusseldorf, the world’s premier show for the packaging industry. This initiative showcases Optima’s leadership in digitalization in the machine building industry. “Mission Total Care” illustrates the complete life cycle of machine equipment beginning with the innovative training concept that takes place at the VR Center before the machine installation, to the new service benefits and machine retrofitting. “Mission Total Care” also highlights all of the achievements and products that have created new efficiency opportunities in the production and service areas through digitalization. Today’s users are accustomed to intuitive and comprehensive device operation. New machine-interfaces (HMIs) even take it a step further as they can be adapted to the industrial environment and enhanced with essential “Mixed-Reality Features”.
At Interpack 2017 Optima will present its pioneering work on “Project-Zero”. This future-oriented technology will ring in a new era in production flexibility. The operator can preset the design and data and the machine will accomplish the rest. The different packages will be produced “inline”.
The importance of machine flexibility is increasing in general within the market. Life Science now offers modular and scalable systems that allow a smooth transfer from the R&D machine to the production system for state-of-the-art wound dressing. New and mostly very expensive, highly active and at the same time sensitive agents in the pharmaceutical industry also demand flexible technology. Therefore, Optima Pharma developed the MultiUse machine specifically for this type of application. This machine allows efficient small batch processing for specialized pharmaceutical safety and sterile requirements.
At the same time, the demand for turnkey projects is increasing at all of Optima’s divisions. These machine lines can include all type of tasks and start, for example, with the automatic de-palletizing of coffee capsules and end with palletizing of the finished product. Optima Consumer is the only manufacturer of complete lines for beverage capsule packaging worldwide.
Optima has Industrie 4.0 solutions with its TCAM and OPAL digital systems. The OPAL software (Optima Process Automation Library) connects the ERP level (Enterprise Resource Planning - superordinate economical processes) with the manufacturing level. The data is uploaded into the production management system and transferred into the plant’s production control center. In addition detailed processes analysis are possible. The TCAM (Total Care Asset Management) enables detailed process analysis by continuously recording the machine’s condition and service needs early. This reduces unplanned downtime. TCAM also relays all important information from the machine digitally, from enlarged drawings to video tutorials.
Optima offers a diverse and exceptionally wide range machine and technology portfolio with solutions for the packaging and manufacturing processes of the future.
Here for Others - Ready to Help
Social responsibility is very important at Optima. A storm in the summer of 2016 caused severe damage to villages near Schwaebisch Hall. Optima employees from different departments took the initiative and volunteered to help. The employees were exempt from work with pay and supported by Optima with materials and tools. A fundraising campaign organized by the employees was matched by Optima’s management and resulted in raising 65,000 Euro. The donation was used to help rebuild the town of Braunsbach. Another example of social responsibility is the bone marrow donation program organized by Optima and the DKMS (Tubingen). The bone marrow typecasting is executed at Optima and financed by the company. All of the five Optima bone marrow donors played a significant role in saving lives.
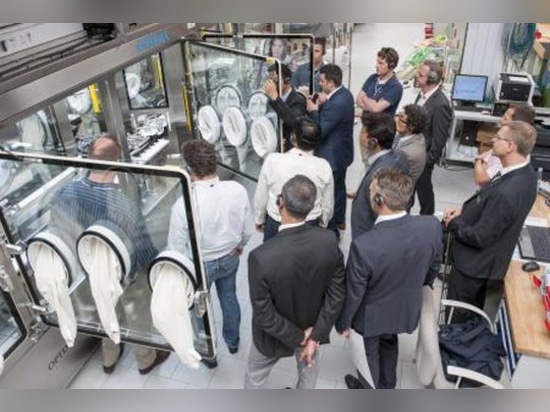
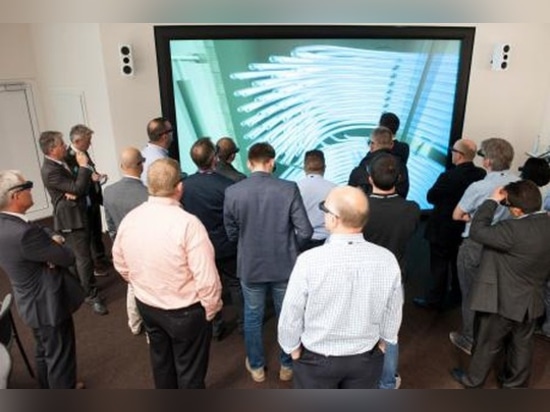
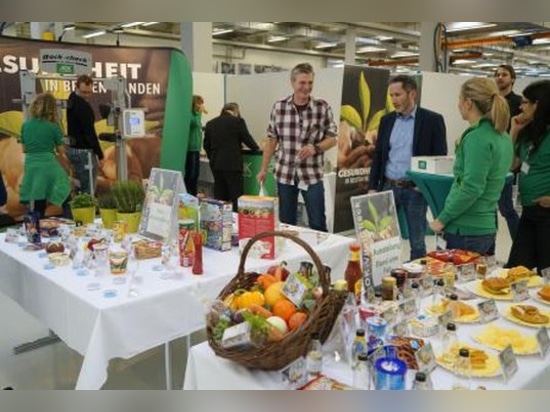