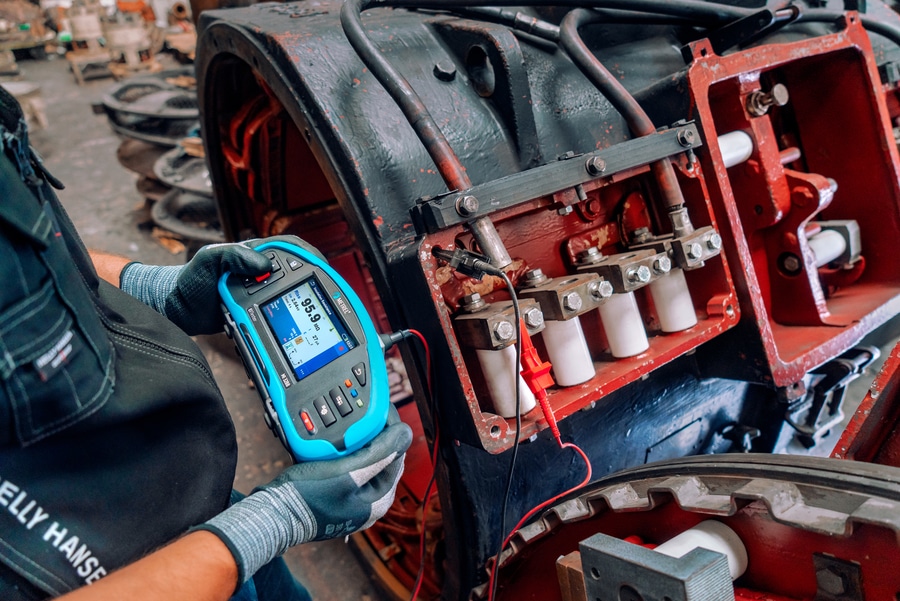
Voir la traduction automatique
Ceci est une traduction automatique. Pour voir le texte original en anglais cliquez ici
#Livres blancs
Test du stator du générateur
MI 3288 Testeur d'isolation de la terre
Les matériaux d'isolation des fils électriques d'aujourd'hui ont beaucoup évolué depuis l'époque de la soie et de la gutta-percha (latex naturel), qui devaient paradoxalement être maintenues humides pour adhérer au fil et ne pas se détacher. Ils ont des propriétés diélectriques incomparablement meilleures, sont moins chers et plus durables, et peuvent être fabriqués dans n'importe quelle forme. Néanmoins, ils ne sont pas à l'abri de la dégradation par des éléments tels que les températures élevées et (très) basses, les rayons UV, la surtension, l'humidité et les forces mécaniques.
Étant donné les graves conséquences d'une défaillance des matériaux, l'analyse de l'isolation est l'une des méthodes de base pour évaluer le bon fonctionnement de pratiquement toute machine, appareil, installation ou système électrique. Cependant, les exigences, les lignes directrices et les normes diffèrent considérablement d'un pays à l'autre. Les générateurs et autres (grandes) machines électriques rotatives sont des exemples distincts, car l'isolation est soumise à des contraintes plus importantes que dans d'autres applications, en particulier à des températures élevées et à des forces mécaniques. Cependant, elle reste sensible à des éléments à première vue banals comme l'humidité, qui, si les conditions sont réunies, peut faire des ravages et endommager irrémédiablement la machine.
Humidité, température et isolation
Quel que soit le matériau isolant utilisé, le principal effet de l'humidité est (outre la dégradation physique du matériau par divers processus chimiques) la création de lignes de fuite conductrices qui entraînent une forte diminution de la rigidité diélectrique et, par conséquent, une augmentation de la probabilité de claquage (diélectrique). Dans le cas des générateurs, l'humidité de l'air peut être aspirée à l'intérieur de la machine par les orifices de refroidissement ou par des fissures discrètes dans le cas des générateurs dotés d'un système de refroidissement en circuit fermé (système de refroidissement par liquide).
Les fluctuations de température à l'intérieur de la machine provoquent la condensation de l'humidité sous forme liquide et son infiltration dans l'isolation des enroulements. S'il n'existe aucun moyen de sécher les enroulements ou si personne n'a vérifié la qualité de l'isolation, la machine peut avoir une durée de vie très courte. Mais l'humidité peut pénétrer dans la machine même lorsqu'elle n'est pas en service, c'est-à-dire dans des conditions de stockage inappropriées, exposée au soleil et à d'autres influences environnementales néfastes. Une telle machine doit être inspectée minutieusement avant d'être mise en service et c'est exactement ce qu'un inspecteur de la sécurité électrique affilié à Metrel a dû faire pour un générateur de 100 kW soupçonné d'être affecté par l'humidité en raison des conditions de stockage.
Sorti de l'entrepôt, mais pas encore en service
Un générateur de 100 kW (triphasé, 50 Hz, 400 V / 195 A, 1000 tr/min) a été utilisé pendant une dizaine d'années dans une microcentrale hydroélectrique (turbine Francis), jusqu'à ce que la centrale soit démantelée en raison de problèmes d'écoulement de l'eau. Le générateur a ensuite été stocké dans un entrepôt plutôt délabré, non loin de l'ancienne centrale, mais à proximité d'un petit étang, avec d'autres machines électriques, dont plusieurs grands moteurs électriques. Ces derniers, dont le stator (armature) et le rotor étaient mal isolés, ont dû être réparés, et l'on soupçonnait que le générateur, qui était sur le point d'être installé dans une nouvelle centrale électrique (hydroélectrique), pouvait présenter des problèmes similaires.
Essais PI, DAR et DD
Le générateur a été transporté dans l'atelier de réparation d'un fabricant de transformateurs. Des quantités élevées d'interférences électromagnétiques telles que celles que l'on peut trouver dans cet environnement et dans des environnements similaires peuvent poser des problèmes lors des tests et des mesures, mais le testeur d'isolation de la terre MI 3288 utilisé par l'inspecteur est équipé de fils d'essai blindés qui atténuent considérablement ce problème. En outre, il dispose de bornes d'entrée protégées et les cordons de test sont fournis avec des cordons de connexion appropriés - élimination des courants de fuite potentiels résultant de la contamination de surface et de l'humidité et susceptibles d'influencer la précision des mesures.
Avant de s'engager dans une mesure/analyse de la résistance d'isolement, il convient toutefois de réfléchir à la résistance minimale souhaitée pour la machine/le système en question. Une bonne règle empirique est d'avoir au moins 1 MΩ de résistance pour chaque kV. Toutefois, ce chiffre (1 MΩ) n'est valable qu'à température ambiante (20 °C). À des températures plus élevées, les exigences augmentent très rapidement - pour chaque tranche de 10 °C, la résistance requise augmente de plus de 50 % (machines rotatives de classe B). Par exemple, à 40 °C, la résistance doit être d'au moins 2,5 MΩ pour chaque kV (nominal).
La relation entre l'humidité et les changements de résistance n'est pas aussi simple et varie considérablement en fonction des différents matériaux d'isolation, mais on peut tout de même affirmer que toute humidité réduit la résistance d'isolation. Quoi qu'il en soit, l'inspecteur a connecté les enroulements du rotor et du stator du générateur au testeur d'isolation de la terre MI 3288 et a pris trois mesures distinctes pour chacun d'entre eux : la méthode de l'augmentation du temps/indice de polarisation (PI), le rapport d'absorption diélectrique (DAR) et l'essai de décharge diélectrique. Parmi ces trois mesures, le meilleur choix pour évaluer les dommages causés par l'humidité à l'isolation est le test de décharge diélectrique (DD).
L'objet testé est maintenu sous haute tension pendant une période prolongée, généralement entre 10 et 30 minutes. La tension est ensuite coupée et le courant de décharge est mesuré. Les courants (de décharge) mesurés par le générateur étaient, comme on l'avait initialement prévu, très élevés, tout comme (évidemment) le résultat du test de décharge diélectrique, supérieur à 5 (une bonne valeur est généralement inférieure à 2).
Le générateur a donc été révisé ; le rotor a été démonté et nettoyé en profondeur, de même que le stator. Les deux ont été contrôlés visuellement pour vérifier qu'ils n'étaient pas endommagés et ont été stockés dans une pièce chauffée à atmosphère contrôlée pour sécher complètement. Après l'assemblage, le générateur a de nouveau été évalué à l'aide du testeur d'isolation de la terre MI 3288 et a obtenu d'excellents résultats - l'isolation a été jugée bonne et le générateur a été mis en service dans la nouvelle centrale électrique.