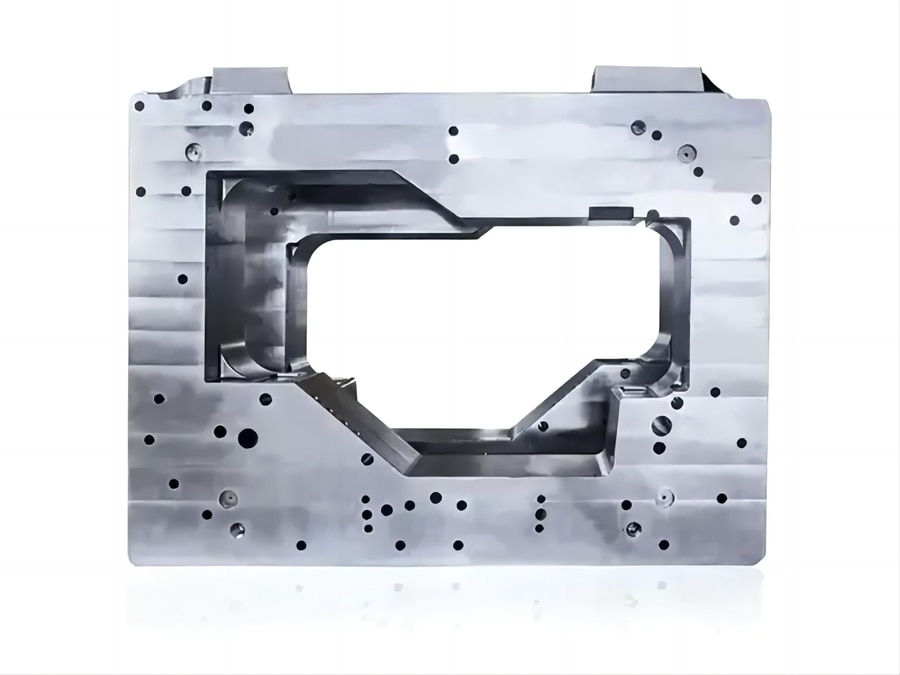
#Actualités du secteur
Avantages d'une base de moule pour véhicule à nouvelle énergie
Avantages d'une base de moule pour véhicule à nouvelle énergie
Une base de moule pour véhicule à énergie nouvelle est une base de moulage qui peut être utilisée pour mouler et assembler toutes les pièces qui composent un véhicule à énergie complètement nouvelle. Il s'agit d'un processus unique qui permet d'économiser de l'énergie et de l'argent dans le processus de production, et constitue également un excellent moyen de réduire le poids.
Ce type de moule est utilisé pour produire une large gamme de pièces moulées par injection de plastique dans l'industrie automobile, notamment des pare-chocs, des supports, des boîtiers de batterie, des capots de moteur et des poutres structurelles. Il présente de nombreux avantages par rapport aux moules métalliques traditionnels et est très flexible pour une variété d'applications.
De plus, son temps de cycle est relativement court (60 à 180 secondes), ce qui permet de prendre en charge des volumes de production moyens à élevés avec une finition post-moulage minimale. Il est disponible pour tous les types de pièces les plus courants et convient particulièrement aux produits qui nécessitent un haut degré de précision et de flexibilité dans leur conception.
Grâce à cette technologie, Kejia peut produire une gamme de formes et de finitions de carrosserie de véhicules électriques différentes à un volume très élevé. Cela signifie qu'elle peut offrir des délais d'exécution rapides, réduisant ainsi les coûts de production et augmentant les marges pour ses clients.
L'utilisation de pièces en plastique pour les véhicules électriques peut contribuer à réduire la quantité de métal nécessaire à la production du véhicule, ce qui peut réduire le poids total du véhicule et augmenter le rendement énergétique. Cela peut contribuer à augmenter l’autonomie du véhicule électrique et à réduire le coût de fonctionnement de la voiture.
Le SMC est un nouveau type de matériau développé spécifiquement pour les véhicules électriques. Ses propriétés légères, solides et résistantes à la corrosion sont idéales pour de nombreuses pièces nécessaires dans un véhicule à énergie nouvelle.
En conséquence, il est devenu un choix très populaire parmi les fabricants de véhicules électriques. Il peut être moulé dans une variété de formes complexes qui permettent de gagner du poids et de réduire le nombre de pièces devant être soudées ensemble lors de la fabrication.
Ce matériau peut être moulé sous différentes formes et possède d'excellentes caractéristiques d'isolation thermique, antidérapantes et anticorrosion. Il est également durable et facilement recyclable, ce qui en fait un choix parfait pour les véhicules à énergies nouvelles.
Un autre avantage du SMC est qu’il peut être transformé en sections très fines, ce qui constitue une caractéristique importante pour les composants EV. Il peut également être conçu pour répondre à des exigences spécifiques, telles que l'exigence d'un haut niveau de précision et de stabilité dimensionnelle.
Il est possible de mouler les pièces SMC dans la forme exacte des composants intérieurs d'un véhicule électrique, ce qui en fait un excellent choix pour créer des pièces intérieures personnalisées qui peuvent être facilement installées dans la voiture. Ces pièces SMC peuvent également être produites en grandes quantités et avoir un prix très bas, ce qui constitue un facteur important pour les fabricants de véhicules électriques.
Plusieurs alliages SMC différents sont utilisés pour le moule SMC, et chacun possède ses propres caractéristiques uniques. Certains alliages SMC ont une résistance plus élevée et un taux d’absorption d’eau plus faible que d’autres. Il est également possible de mélanger et d'associer des plis avec différents types de renfort fibreux, aidant ainsi les concepteurs à optimiser la pièce en termes de performances mécaniques ainsi que de moulabilité, de coût et de poids.