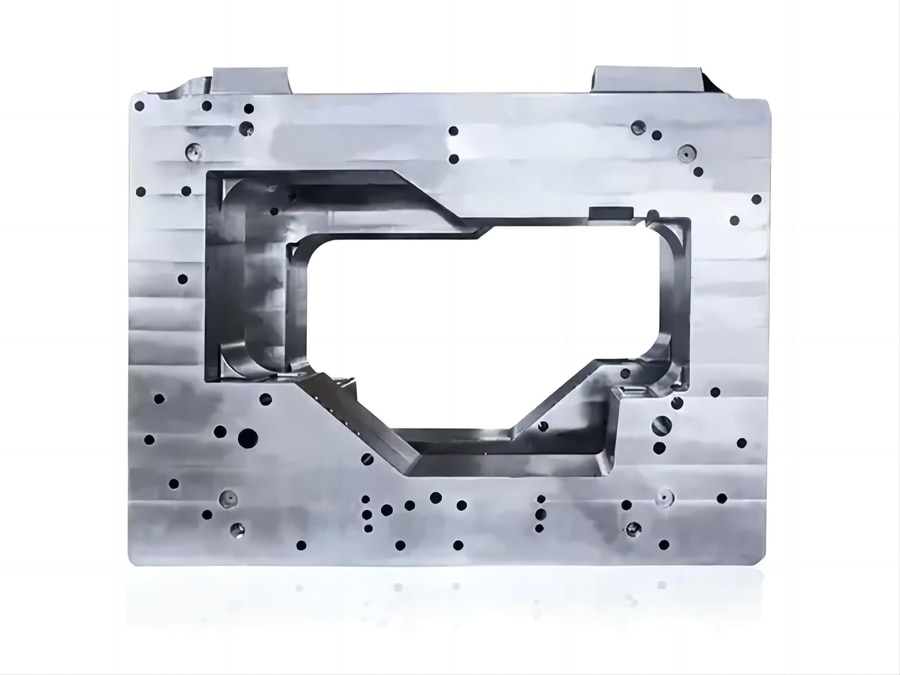
#Actualités du secteur
La base du moule automobile se compose de deux composants principaux
La base du moule automobile se compose de deux composants principaux
Base de moule automobile
La base de moule automobile se compose de deux composants principaux : le moule d'injection (plaque A) et le moule d'éjection (plaque B). Les opérateurs de machines de moulage injectent de la résine plastique fondue dans les images de cavité de la plaque A ; la pièce en plastique obtenue refroidit et durcit ensuite avant d'être retirée de la plaque B.
Le système de canaux du moule à injection dirige la résine plastique fondue du cylindre de la machine de moulage par injection vers les images de la cavité. Ceci est réalisé grâce à une douille d'injection, qui se ferme hermétiquement contre la buse du cylindre d'injection et dirige le plastique fondu vers ces cavités. En plus d'une carotte, le système de canaux peut également comprendre une ouverture (porte de tunnel) dans la surface du moule sur la ligne de joint qui permet à la résine plastique fondue de s'écouler librement à travers le canal.
Ces carottes constituent un élément essentiel du processus de moulage par injection ; ils permettent à la résine plastique fondue de s'écouler dans l'image de la cavité à travers des canaux usinés dans les faces des plaques A et B. Contrairement au corps d'injection et à la carotte d'injection, ces systèmes de canaux sont froids ; ils ne sont pas conçus pour être chauffés.
Les moules à injection constituent la méthode la plus courante de fabrication de pièces en plastique pour l’industrie automobile. Ils sont évolutifs et peuvent produire de nombreuses pièces en un seul cycle de moulage, ce qui en fait un choix idéal pour les applications de production de masse.
Ils peuvent être utilisés pour fabriquer des pièces automobiles extérieures et intérieures, ce qui aide les constructeurs à réduire le poids de leurs véhicules. Ils peuvent également être utilisés pour créer des éléments décoratifs, tels que des grilles, des poignées de porte et des bouches d'aération.
L’utilisation de plastiques pour ces pièces automobiles constitue une stratégie efficace pour contribuer à réduire le poids total d’un véhicule et à améliorer le rendement énergétique. De plus, de nombreux plastiques sont capables de résister à des conditions météorologiques extrêmes et à des terrains difficiles, ce qui peut être un défi pour les métaux.
Un autre avantage important des plastiques destinés aux pièces automobiles est leur faible coût. Les plastiques moulés par injection sont généralement beaucoup moins chers que leurs homologues métalliques, ce qui permet aux fabricants de réduire les coûts de production. De plus, ils peuvent être personnalisés pour répondre à une exigence esthétique spécifique, ce qui est utile pour améliorer l’apparence d’un véhicule.
Lors de la conception et de la production d'un composant en plastique pour une application automobile, il est essentiel de s'associer à un mouleur par injection expérimenté qui comprend les exigences uniques de l'application. Ils peuvent tirer parti de leur expertise en matière de matériaux pour garantir que le composant répond aux spécifications réglementaires et fonctionne comme prévu, tout en offrant des informations précieuses sur l'industrie automobile.
Le bon matériau est la clé du succès de toute conception de pièce automobile en plastique. Les mouleurs par injection peuvent vous conseiller sur le meilleur type de polymère à utiliser en fonction de la résistance de leur matériau, de leur stabilité dimensionnelle et de leurs propriétés de résistance à la chaleur.
Ils peuvent également fournir des recommandations sur la manière d'optimiser la conception afin d'atteindre les fonctionnalités souhaitées et les objectifs de performances pour chaque application. Ceci est particulièrement important pour les composants complexes et volumineux, tels que ceux que l’on trouve dans le compartiment moteur d’un véhicule.