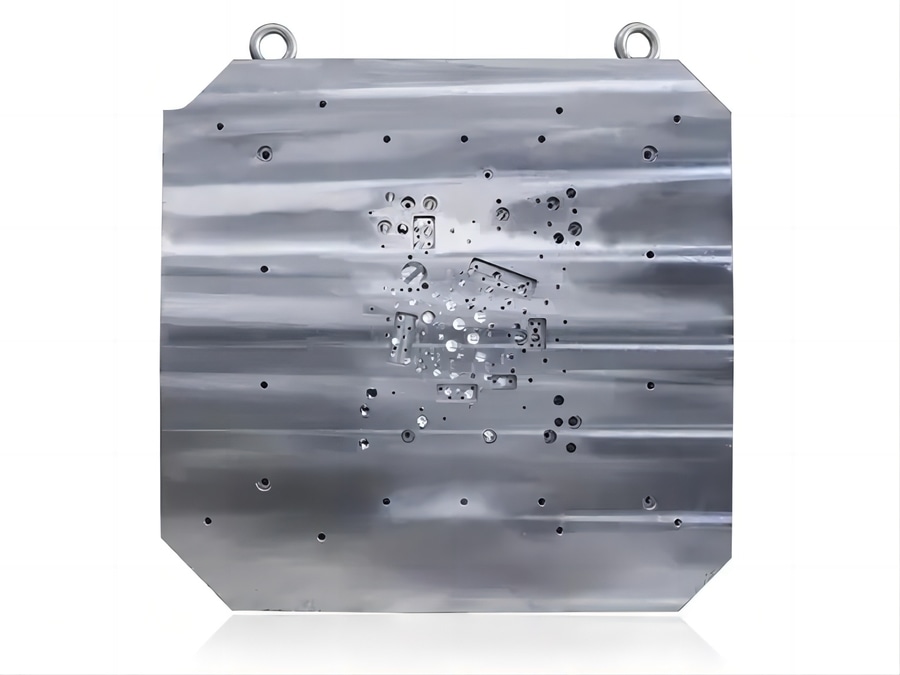
#Actualités du secteur
Quels sont les défis et les inconvénients potentiels associés à l’utilisation de cadres de moulage en alliage dans les moteurs à trois cylindres des voitures à carburant, et comment les fabricants peuvent-ils résoudre ces problèmes pour tirer pleinem
Quels sont les défis et les inconvénients potentiels associés à l’utilisation de cadres de moulage en alliage dans les moteurs à trois cylindres des voitures à carburant, et comment les fabricants peuvent-ils résoudre ces problèmes pour tirer pleinem
L'adoption de cadres moulés en alliage dans la construction de moteurs trois cylindres pour voitures à carburant offre de nombreux avantages, comme indiqué précédemment. Cependant, cette technologie innovante comporte également son lot de défis et d’inconvénients potentiels qui doivent être résolus pour tirer pleinement parti de ses avantages. Explorons ces problèmes en détail :
Dilatation thermique et contraction :
Les alliages d'aluminium ont un coefficient de dilatation thermique plus élevé que les cadres traditionnels en fonte ou en acier. À mesure que le moteur chauffe pendant le fonctionnement, les cadres de moulage en alliage peuvent se dilater, entraînant des problèmes potentiels tels qu'un jeu accru entre les composants du moteur correspondants et d'éventuels points de fuite. De même, pendant les périodes de refroidissement, les châssis peuvent se contracter, ce qui peut introduire des contraintes sur la structure du moteur.
Pour atténuer ces défis, les fabricants doivent soigneusement réfléchir à la conception et à la sélection des matériaux des cadres de moulage en alliage. Des solutions techniques telles que des barrières thermiques, des matériaux de joint appropriés et des tolérances d'usinage précises peuvent aider à résoudre les problèmes de dilatation thermique et à garantir la fiabilité à long terme du moteur.
Compatibilité des matériaux et usure :
Lorsque des cadres moulés en alliage sont utilisés avec d'autres composants de moteur fabriqués à partir de matériaux différents, il existe un risque de corrosion galvanique, également connue sous le nom de corrosion de métaux différents. La corrosion galvanique se produit lorsque deux métaux différents sont en contact l'un avec l'autre et qu'un électrolyte (par exemple, de l'huile moteur) est présent, entraînant une dégradation accélérée du matériau.
Pour lutter contre la corrosion galvanique, les fabricants peuvent utiliser des revêtements ou des anodes sacrificielles pour protéger les cadres de moulage en alliage. De plus, une sélection minutieuse des matériaux pour les autres composants du moteur et la mise en œuvre de mesures d'isolation appropriées peuvent minimiser le risque de corrosion galvanique et garantir la longévité du moteur.
Intégrité structurelle et fatigue :
Les alliages d'aluminium ont des propriétés matérielles différentes de celles de la fonte ou de l'acier, ce qui peut avoir un impact sur l'intégrité structurelle et la résistance à la fatigue des cadres de moulage en alliage. Les composants du moteur, en particulier ceux soumis à des conditions de contraintes élevées, doivent résister à des cycles de chargement répétitifs sans défaillance.
Pour améliorer l'intégrité structurelle et la résistance à la fatigue, les fabricants peuvent effectuer une analyse par éléments finis (FEA) détaillée et utiliser des outils de simulation avancés pendant la phase de conception. Cette approche leur permet d'optimiser la géométrie et la répartition de l'épaisseur du cadre, garantissant qu'il répond aux propriétés mécaniques requises et reste durable tout au long de sa durée de vie opérationnelle.
Considérations relatives aux coûts :
Le coût de fabrication des cadres de moulage en alliage peut être plus élevé que celui des matériaux traditionnels, tels que la fonte. L'augmentation des coûts peut avoir un impact direct sur le coût de production global du véhicule, affectant potentiellement sa compétitivité sur le marché.
Les fabricants peuvent explorer les opportunités d’optimiser le processus de moulage des alliages et d’augmenter l’efficacité de la production afin de réduire les coûts. De plus, les progrès dans la technologie des matériaux pourraient conduire au développement d’alliages d’aluminium plus rentables sans compromettre les performances, ce qui les rendrait plus viables pour une production de masse.
Recyclage et impact environnemental :
Si les alliages d’aluminium sont recyclables, le processus de recyclage nécessite des apports énergétiques importants. Alors que l’industrie automobile poursuit sa quête de durabilité et de réduction de son impact environnemental, il devient crucial de s’attaquer au processus de recyclage à forte intensité énergétique.
Pour relever ce défi, les fabricants peuvent investir dans des pratiques de fabrication durables et explorer des systèmes de recyclage en boucle fermée. Ces systèmes favoriseraient la collecte et la réutilisation des déchets d'aluminium générés au cours du processus de fabrication, réduisant ainsi la dépendance à l'égard des matières premières primaires et réduisant l'empreinte environnementale globale.
En conclusion, l’adoption de cadres moulés en alliage dans les moteurs à trois cylindres des voitures à carburant présente une voie prometteuse pour améliorer les performances, le rendement énergétique et la dynamique globale du véhicule. Cependant, les fabricants doivent soigneusement relever les défis associés à la dilatation thermique, à la compatibilité des matériaux, à l'intégrité structurelle, aux considérations de coûts et au recyclage afin de maximiser les avantages de cette technologie tout en garantissant une fiabilité et une durabilité à long terme. Ce faisant, l’industrie automobile peut poursuivre sa quête d’innovation et d’efficacité à l’ère des véhicules économes en carburant et respectueux de l’environnement.