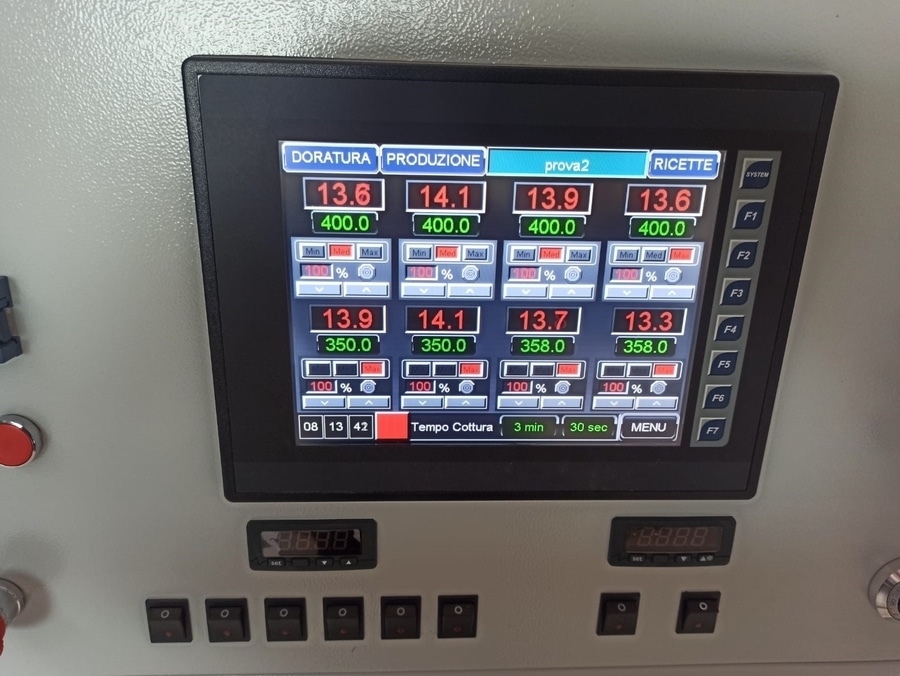
Voir la traduction automatique
Ceci est une traduction automatique. Pour voir le texte original en anglais cliquez ici
#Actualités du secteur
Four à pizza industriel utilisant la technologie Horner Automation
Il s'agit d'un projet gratifiant mais difficile, dont la mise en œuvre a pris plusieurs mois. Un four industriel sert avant tout à cuire de grandes quantités d'aliments par lots, mais il peut également être utilisé pour de plus petites quantités d'aliments.
Introduction
Ce projet de four industriel s'est déroulé à Massa, en Italie. Il s'agit d'un projet gratifiant, mais difficile, dont la mise en œuvre a pris plusieurs mois. Un four industriel sert avant tout à cuire une grande quantité d'aliments par lots, mais il peut également être utilisé pour des quantités plus faibles. Pour ce faire, les fours industriels doivent pouvoir contrôler plusieurs températures simultanément à l'aide de différents interrupteurs et commandes.
Objectifs du projet
L'un des aspects les plus intéressants de ce projet est qu'il y avait une grande variété d'objectifs à atteindre pour que le projet soit considéré comme une réussite.
Le premier objectif du projet était de mettre à jour le matériel existant sur les fours. La principale amélioration matérielle consistait à remplacer les commandes de température existantes sur les fours. Chaque taille de four comporte un nombre différent de commandes de température qui devaient être remplacées.
Le deuxième objectif du projet était de mettre à jour le logiciel utilisé par le client afin d'en améliorer la fonctionnalité et la flexibilité. Il s'agissait notamment de permettre à l'utilisateur d'enregistrer une recette. Cela signifie qu'un ensemble particulier de paramètres et d'instructions peut être sauvegardé et que l'utilisateur peut les réutiliser chaque fois qu'il en a besoin, plutôt que de devoir recréer la recette au début de chaque utilisation.
L'objectif principal de l'entreprise était d'augmenter la production avec le four amélioré et donc de maximiser les ventes.
Défis à relever
Le principal défi du projet consistait à atteindre les objectifs susmentionnés tout en respectant les réglementations industrielles. Dans chaque cas, les réglementations sont fixées par le client. En effet, chaque client a ses propres besoins.
Horner comprend à quel point il est important d'être flexible pour servir ses clients. Le respect des réglementations en matière de chauffage en est un exemple. Horner peut être flexible grâce à la large gamme de fonctionnalités que l'on trouve dans chaque contrôleur.
Dans le cas de l'OCS, il peut contrôler la température en plusieurs points différents d'une machine. Le technicien peut créer un fichier .csv d'enregistrement des données. Ce fichier peut être lu par le client, qui peut ainsi voir comment la température a été contrôlée dans le four pendant le processus de chauffage, ce qui lui permet de certifier sa propre production.
Dans ce cas, les données stockées sont les températures. Le protocole Modbus TCP permet au client de récupérer des données en temps réel pour sa base de données interne. WebMI facilite le contrôle du four grâce à la communication avec l'OCS et permet de voir si l'opérateur fait ce qu'il faut. Si l'opérateur ne fait pas ce qu'il faut, il peut passer outre, charger une recette différente et continuer à surveiller la production.
Détails techniques de la mise en œuvre
Grâce à l'enregistrement des données, aux recettes au format .csv, à Modbus TCP et à WebMI, le four est conforme à la norme Industry 4.0.
La communication Scada sur Ethernet avec le protocole Modbus TCP est une exigence pour de nombreux clients. Modbus RTU est utilisé pour contrôler les OI et les variateurs de fréquence. Ceci est important car Scada est un gestionnaire de système qui peut permettre à une usine d'être surveillée à distance, généralement sur Intranet. Le protocole Modbus TCP est l'un des protocoles de communication disponibles sur les progiciels SCADA. Le protocole Modbus RTU est, dans ce cas, utilisé pour contrôler les E/S à distance du four et les variateurs de fréquence.
Une large gamme de contrôleurs Horner Automation a été utilisée dans le cadre de ce projet. Par exemple, les XL6, EXL6e, XL7e, EXL10e et SmartMods.
La valeur de Horner dans cette application
La raison principale pour laquelle une telle gamme de contrôleurs était nécessaire était due aux différentes tailles d'écran des fours. Les contrôleurs ont également été utilisés en raison de leur large gamme d'E/S. Par exemple, le XL7e possède deux ports Ethernet, tout comme l'EXL10e. Cela signifie que les contrôleurs ont des capacités HTTP (Envision RV), FTP (Envision FX) et WebMI.
Les fonctions de communication sont une autre caractéristique utile du contrôleur. Par exemple, les EXL6e, XL7e et EXL10e disposent tous de ports RS-232 et RS-485, de protocoles PLC /Drive. Ils disposent également de ports USB et d'entrées/sorties RTU/Modbus/Maître/Esclave/Série ASCII.
La programmation Cscape utilisée pour réaliser ce projet était une programmation ladder avancée. L'autre logiciel Horner utilisé dans le cadre du projet était WebMI.
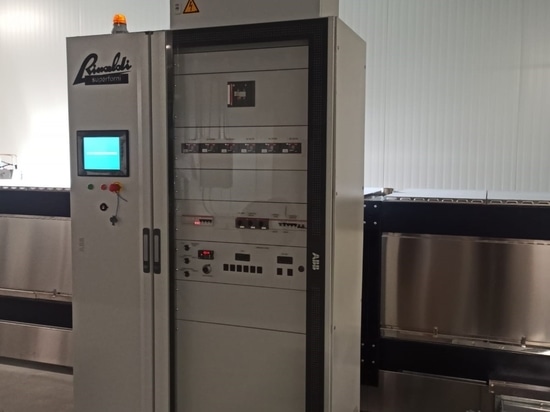
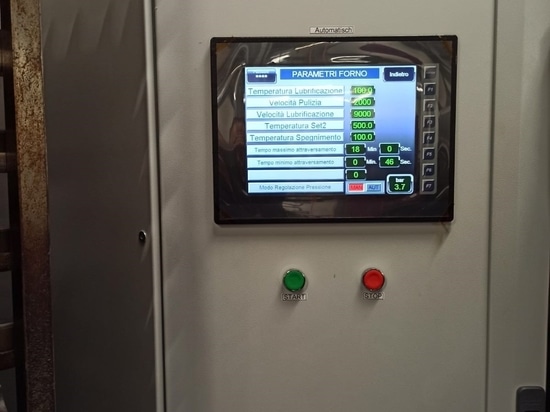

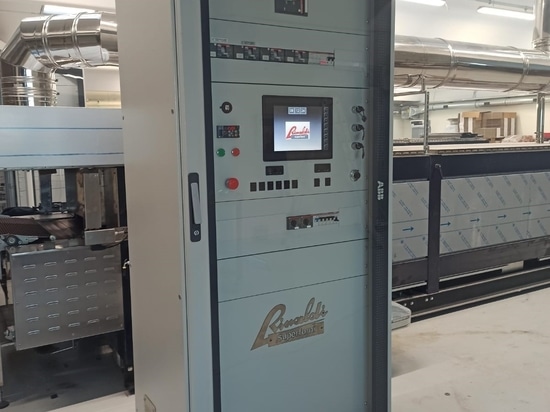