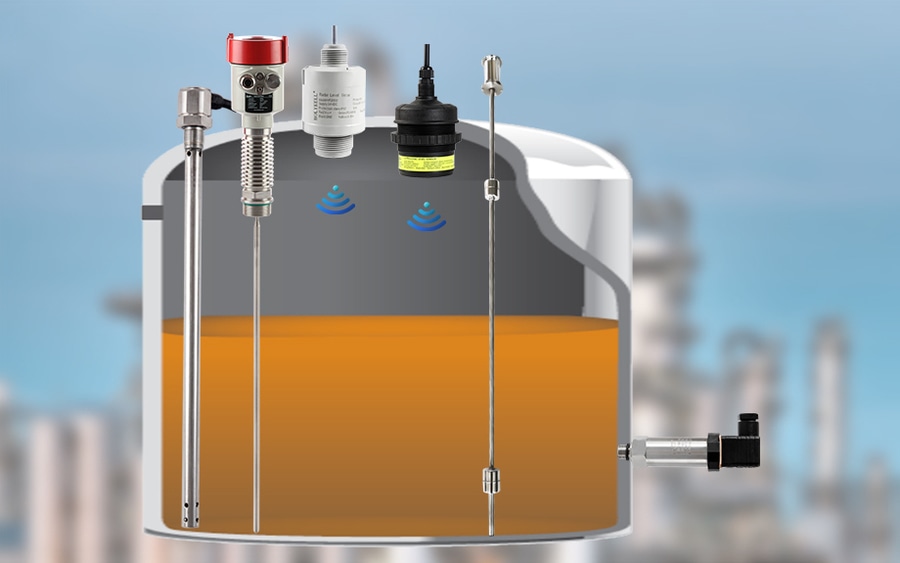
Voir la traduction automatique
Ceci est une traduction automatique. Pour voir le texte original en anglais cliquez ici
#Actualités du secteur
Technologies de mesure de niveau pour l'industrie du raffinage
Capteur de niveau de pression submersible
L'industrie du raffinage subit d'importantes transformations, les raffineries existantes se modernisant pour rester compétitives. Les usines de raffinage visent à accroître l'efficacité énergétique, à maximiser la production et à améliorer la qualité des produits. Cependant, les raffineries sont confrontées à divers défis au cours de cette transition, notamment la nécessité d'améliorer l'efficacité énergétique, de réduire les coûts d'exploitation et de maintenance, et de garantir la sécurité tout en respectant des réglementations environnementales strictes. Ces défis sont également présents dans les nouvelles raffineries, qui sont confrontées à la complexité de l'intégration de l'automatisation pour traiter le pétrole brut lourd ou à haute teneur en soufre, moins cher.
Dans les opérations de raffinage, la précision de la mesure et du contrôle des niveaux est cruciale. Avec des taux de production quotidiens pouvant atteindre 100 000 barils, les raffineries peuvent avoir plus de 1 000 points de mesure de niveau. Les méthodes traditionnelles, telles que les systèmes à flotteur, sont sujettes à des imprécisions dues aux variations de densité et de température des différents pétroles bruts, qui affectent la fiabilité de ces mesures. Ces fluctuations peuvent compromettre le processus de contrôle et avoir un impact négatif sur la productivité des raffineries et la qualité des produits. C'est pourquoi les raffineries s'orientent vers des technologies plus précises et nécessitant moins de maintenance pour garantir des mesures exactes et améliorer le contrôle global des processus.
Dans cet article, nous examinerons cinq technologies avancées de mesure de niveau adaptées à l'industrie du raffinage : Radar, Ultrasons, Pression différentielle, Magnétostrictif et Capacitif. Chaque technologie présente des avantages et des limites qui lui sont propres, ce qui la rend adaptée à différentes applications en fonction des exigences de performance, des conditions de fonctionnement et des contraintes d'installation.
1. Transmetteurs de niveau à radar à ondes guidées (GWR)
Principe de fonctionnement :
Les transmetteurs de niveau à radar à ondes guidées (GWR), également connus sous le nom de réflectométrie dans le domaine temporel (TDR) ou de transmetteurs de niveau à radar à impulsions micro-ondes (MIR), permettent de mesurer le niveau en continu. L'appareil envoie des impulsions micro-ondes de faible puissance le long d'une sonde, qui se déplace à la vitesse de la lumière. Les impulsions sont réfléchies à l'interface liquide-air et le délai entre l'émission et la réception est utilisé pour calculer la distance jusqu'à la surface du liquide.
Avantages :
Précision et fiabilité : Fournit des mesures précises dans des applications difficiles telles que la mesure des interfaces liquide-liquide (par exemple, l'interface huile-eau) et à travers la mousse.
Insensible aux changements de milieu : Les variations de densité, de constante diélectrique ou de conductivité du liquide n'affectent pas la précision de la mesure.
Peu de maintenance : Dépourvus de pièces mobiles, les dispositifs GWR nécessitent une maintenance minimale et peuvent être facilement intégrés dans les systèmes existants.
Limites :
Considérations relatives à l'installation : Le choix du type de sonde et la hauteur d'installation peuvent limiter les performances, en particulier dans les applications avec des produits épais ou collants.
2. Transmetteurs de niveau radar sans contact
Principe de fonctionnement :
Les transmetteurs de niveau radar sans contact envoient des signaux à travers la vapeur pour mesurer la distance de surface. Ce type de transmetteur est idéal pour mesurer les liquides visqueux, collants et agités dans les réservoirs avec mélangeurs ou agitateurs, car il isole complètement le capteur du produit à mesurer.
Avantages :
Pas de contact physique : Convient aux milieux dangereux ou corrosifs, car le capteur n'entre pas en contact avec le produit à mesurer.
Maintenance minimale : Comme le dispositif n'interagit pas avec le liquide, il n'y a pas de pièces mobiles susceptibles de s'user, ce qui réduit les coûts de maintenance.
Limites :
Difficultés d'installation : Une ligne de visée claire vers la surface est nécessaire pour une mesure précise. Les surfaces rugueuses ou turbulentes peuvent réduire la précision, et la mousse ou l'agitation de la surface peut entraîner une perte de signal.
3. Transmetteurs de niveau à ultrasons
Principe de fonctionnement :
Les transmetteurs de niveau à ultrasons utilisent des ondes sonores pour mesurer la distance à la surface du liquide. Une impulsion est émise par le transmetteur et le temps de réflexion de l'impulsion est utilisé pour déterminer le niveau.
Avantages :
Installation et configuration faciles : Simple à installer et à configurer, il convient à diverses applications, y compris les réservoirs et les silos.
Mesure sans contact : Élimine la nécessité d'un contact direct avec le fluide du procédé, ce qui réduit la maintenance.
Limites :
Sensibilité à la température : Les variations de la température du procédé peuvent affecter la vitesse du son, ce qui nécessite une compensation de la température pour une mesure précise.
Conditions de surface : La mousse, la vapeur ou les surfaces turbulentes peuvent interférer avec les ondes ultrasoniques, réduisant ainsi la précision de la mesure.
4. Transmetteur de pression Mesure de niveau
Principe de fonctionnement :
Les transmetteurs de pression mesurent indirectement le niveau de liquide en mesurant la pression exercée par la colonne de liquide. Dans les conteneurs ouverts, la pression au fond du conteneur correspond à la hauteur de la colonne de liquide. Pour les conteneurs pressurisés, des transmetteurs de pression différentielle sont utilisés pour compenser la pression interne.
Avantages :
Polyvalent : convient à une large gamme de types de liquides, y compris les boues, et fonctionne efficacement dans des environnements à haute pression et à haute température.
Rentable : L'une des technologies de mesure de niveau les plus abordables, idéale pour les applications standard.
Limites :
Variation de la densité : Les transmetteurs de pression sont affectés par les variations de densité du fluide, ce qui peut avoir un impact sur la précision de la mesure.
Ne convient pas aux liquides corrosifs ou visqueux : Des matériaux ou des revêtements spéciaux peuvent être nécessaires, ce qui peut accroître la complexité de la maintenance.
5. Transmetteurs de niveau capacitifs
Principe de fonctionnement :
Les capteurs de niveau capacitifs mesurent les changements de capacité provoqués par la présence d'un liquide entre deux électrodes conductrices. Lorsque le niveau du liquide change, la capacité change également, ce qui permet de mesurer le niveau avec précision.
Avantages :
Idéal pour les petits réservoirs et les applications à faible volume : Les capteurs capacitifs sont très efficaces pour mesurer le niveau dans des réservoirs petits ou étroits où d'autres technologies ne pourraient pas être utilisées.
Sans contact : Convient aux liquides propres qui ne présentent pas un niveau élevé de particules ou de mousse.
Limites :
Susceptible de s'accumuler : Si le liquide est visqueux ou collant, l'accumulation sur le capteur peut affecter la précision.
Limité à des milieux spécifiques : Convient mieux aux liquides non corrosifs et propres ; n'est pas idéal pour les substances très turbulentes ou sujettes à la mousse
Conclusion :
Dans l'industrie du raffinage, une mesure de niveau précise est essentielle pour maintenir la sécurité, l'efficacité et la qualité des produits. Bien que chacune de ces cinq technologies offre des avantages distincts, le choix de la bonne solution de mesure de niveau dépend de l'application spécifique, des conditions opérationnelles et du type de fluide mesuré. En s'appuyant sur des technologies avancées telles que les capteurs radar, ultrasoniques, de pression différentielle, magnétostrictifs et capacitifs, les raffineries peuvent garantir des mesures de niveau plus fiables et plus précises, ce qui permet d'améliorer le contrôle opérationnel et de réduire les coûts de maintenance.