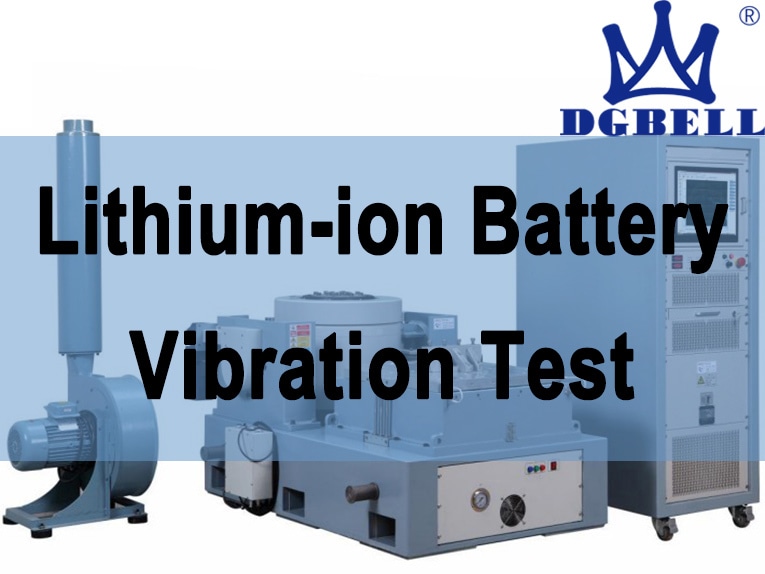
Voir la traduction automatique
Ceci est une traduction automatique. Pour voir le texte original en anglais cliquez ici
#Actualités du secteur
Test de vibration de la batterie lithium-ion
Test de vibration de la batterie lithium-ion
Les batteries au lithium-ion présentent des risques pour la sécurité dans l'aviation civile et le transport routier, ainsi que dans les transports et les appareils ménagers. Afin de trouver des solutions à ces problèmes, l'impact des vibrations mécaniques sur les performances et l'emballement thermique des batteries lithium-ion dans des conditions de basse tension a été étudié. Dans des conditions de basse tension, les vibrations mécaniques provoquent une augmentation de la température d'emballement thermique des batteries lithium-ion et un changement significatif du temps d'arrêt des soupapes de sécurité.
Les vibrations mécaniques à basse fréquence et de grande amplitude accélèrent le processus de court-circuit des batteries, tandis que les vibrations à haute fréquence augmentent la température d'allumage et le volume d'échappement des batteries au lithium. Pour les batteries lithium-ion 18650, la température à laquelle la soupape de sécurité s'ouvre est comprise entre 140 et 150 ℃. Lorsque la soupape de sécurité s'ouvre, l'intensité de la libération de gaz est relativement élevée, et le signal de gaz peut être une variable clé pour l'avertissement de sécurité des piles au lithium. Après une vibration à basse tension, la capacité de décharge des batteries au lithium-ion est inférieure à celle de la batterie d'origine, et la vitesse de décharge est plus rapide que celle de la batterie d'origine
1 Type de défaillance des batteries lithium-ion
En tant que "cœur" d'une voiture, les batteries lithium-ion déterminent la distance parcourue par la voiture. Le système de batterie lithium-ion se compose de quatre éléments principaux : les modules de batterie (cellule unique, série, parallèle), le système de gestion de la batterie (BMS), le système de gestion thermique et les composants électriques et mécaniques. La fonction principale du système de gestion de la batterie est de surveiller la tension, le courant et la température de la batterie en temps réel par le biais de capteurs, d'actionneurs, de puces de contrôle principales, etc. Cependant, en raison du vieillissement interne et de la dégradation de chaque batterie individuelle dans le bloc-batterie, ainsi que de la corrosion du circuit pendant le processus de regroupement des batteries, un mauvais fonctionnement pendant l'utilisation peut entraîner des facteurs externes anormaux tels que la surcharge et la décharge. L'effet combiné de ces facteurs internes et externes entraîne des défaillances internes et externes de la batterie. Les défaillances internes des batteries lithium-ion peuvent être classées en plusieurs catégories : surcharge, décharge excessive, court-circuit interne et emballement thermique.
Les défaillances internes sont causées par le dysfonctionnement du BMS et du capteur lui-même, qui empêche le capteur de fonctionner correctement. D'autre part, elles sont causées par des réactions électrochimiques et des courts-circuits internes dans la structure interne de la batterie, ce qui entraîne un phénomène de dendrite de lithium. Cependant, le danger des défaillances externes des batteries lithium-ion est généralement plus grand que celui des défaillances internes. Les défaillances externes peuvent déclencher une réaction en chaîne de défaillances internes, conduisant finalement à un échauffement incontrôlé. Les défaillances des capteurs sont souvent celles qui passent le plus facilement inaperçues, mais elles peuvent avoir de graves conséquences.
Le BMS s'appuie sur des capteurs pour réaliser des fonctions telles que le contrôle équilibré, le diagnostic des défaillances et l'estimation de l'état de charge (SOC). Si le capteur subit des déviations, dérive ou cesse de fonctionner, il ne peut pas obtenir de données en temps réel et émettre des jugements précis et raisonnables sur l'état actuel de la batterie. Cela peut non seulement réduire les performances, mais aussi provoquer des accidents de sécurité majeurs. Cependant, en raison de la grande dissimulation des capteurs, le diagnostic est difficile, ce qui est également le point central et la difficulté de la recherche actuelle sur les capteurs.
Le BMS gère des ensembles de batteries composés de centaines, voire de milliers de batteries individuelles. En raison des caractéristiques similaires des défaillances des cellules de batterie, des défaillances des capteurs et des défaillances des connecteurs, ainsi que du fait que de nombreuses défaillances sont essentiellement petites et hautement dissimulées, il est difficile de les identifier rapidement. Par conséquent, le BMS produit parfois des erreurs de diagnostic et de fonctionnement. Il est essentiel pour la sécurité des voitures de détecter rapidement et de diagnostiquer avec précision les défaillances multiples de la batterie. Le processus de diagnostic des pannes de batterie peut être grossièrement divisé en quatre aspects : détection des pannes, classification des pannes, localisation des pannes et isolation des pannes. Le traitement des données des batteries joue un rôle fondamental dans le diagnostic des pannes de batterie, et l'efficacité du débruitage peut être vérifiée efficacement en incorporant des méthodes de filtrage morphologique mathématique.
2 Problèmes liés aux méthodes de diagnostic pour la mesure de la tension
(1) Dans les applications pratiques, les systèmes de gestion de la batterie ne peuvent mesurer que la tension aux bornes de chaque batterie individuelle du groupe de batteries. Pour que la valeur de mesure de la tension comprenne la tension aux bornes individuelles et la tension sur les connecteurs, des lignes de mesure supplémentaires doivent être ajoutées, ce qui augmente indubitablement la complexité de l'équipement. Si, au début de la conception du système de gestion de la batterie, la tension collectée comprend la tension aux bornes et la tension sur le connecteur, le système de gestion de la batterie sera incapable d'obtenir avec précision la tension aux bornes de la batterie, et donc incapable de contrôler et de gérer efficacement la charge et la décharge de la batterie, qui est sujette à des défauts de surcharge et de décharge
(2) Les variations de tension causées par les variations de la résistance interne de la batterie sont similaires aux variations de tension lors des défauts de connexion. Les deux étant du même ordre de grandeur, les méthodes de diagnostic basées sur les signaux de tension sont également confrontées au défi de faire la distinction entre les défauts de connexion et les défauts avec augmentation de la résistance interne de la batterie.
(3) Lorsqu'un léger relâchement de la connexion se produit dans le bloc-batterie, l'augmentation de la résistance de contact est très faible. Si le courant de travail de la batterie est faible, un tel défaut de connexion n'entraînera pas de changements significatifs dans le signal de tension. Par conséquent, la méthode de diagnostic basée sur le signal de tension mentionnée ci-dessus peut ne pas être en mesure de détecter un léger relâchement précoce de la connexion.
3 Impact des vibrations
Effectuer des essais de charge et de décharge à la pression atmosphérique sur des batteries soumises à un traitement vibratoire à basse tension, afin de démontrer les changements dans les performances de charge et de décharge des batteries au lithium après le transport aérien. Les résultats ont montré qu'après un traitement par fréquence de vibration à 60 Hz et 80 Hz dans un environnement à basse tension, l'effet de charge était inférieur à celui de la batterie d'origine, et que le traitement à 60 Hz avait l'impact le plus significatif sur la capacité des batteries au lithium ;
Les autres fréquences de vibration accélèrent toutes la vitesse de charge, et la variation est significative à 120 Hz. Au cours du processus de décharge, la courbe de la batterie lithium-ion soumise à un traitement vibratoire de 120 Hz présente l'écart le plus important, tandis que la courbe soumise à une fréquence de 200 Hz présente l'écart le plus faible. Les autres écarts vont de petits à grands, notamment à 60 Hz, 80 Hz, 180 Hz, 160 Hz, 140 Hz et 100 Hz.
On a constaté qu'il n'y avait pas de corrélation positive entre la fréquence des vibrations et la situation de décharge, ce qui peut indiquer que les dommages causés à la structure par les vibrations sont liés à la réactivité de la structure de la batterie à la fréquence et à l'amplitude. Certaines fréquences et amplitudes de vibration endommagent davantage la structure des piles au lithium 18650.
La comparaison globale des courbes de charge et de décharge montre que la capacité de décharge de toutes les piles ayant subi des vibrations est inférieure à celle de la pile d'origine, et que la vitesse de décharge est plus rapide que celle de la pile d'origine. Cela peut indiquer que la capacité et la performance de décharge de la batterie seront endommagées par les vibrations mécaniques.
En fait, après avoir été soumis à des vibrations mécaniques, le degré de contact entre les électrodes positives et négatives dans l'électrolyte des batteries lithium-ion change, ce qui entraîne une modification de la zone de contact entre l'électrode et la solution électrolytique, qui entrave le transfert des ions lithium vers l'électrode négative pendant la charge et la décharge, et réduit donc la quantité de lithium incorporée dans l'électrode négative.
4 Conclusion
Cet article propose une méthode de diagnostic des défauts pour les connexions des batteries lithium-ion basée sur les signaux de vibration mécanique et aboutit aux conclusions suivantes. L'utilisation de différentes plaques de céramique piézoélectrique pour générer une excitation vibratoire, mesurer la réponse vibratoire et extraire les caractéristiques temps-fréquence du signal de réponse permet de classer efficacement les modes de défaillance des connexions monopoint et multipoint. Les travaux futurs permettront d'optimiser la disposition des plaques de céramique piézoélectrique, de collecter les signaux de vibration provenant de l'environnement du véhicule et de rendre cette méthode adaptée au diagnostic des défauts de connexion des batteries lithium-ion dans les véhicules