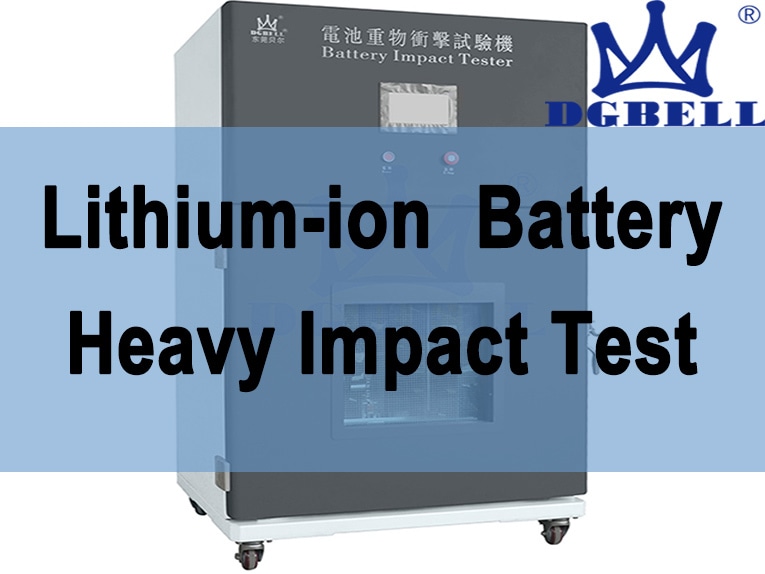
Voir la traduction automatique
Ceci est une traduction automatique. Pour voir le texte original en anglais cliquez ici
#Actualités du secteur
Batterie lithium-ion Test d'impact lourd
Batterie lithium-ion Test d'impact lourd
Les batteries lithium-ion sont devenues l'une des principales sources d'énergie pour les produits électroniques portables tels que les communications mobiles et les ordinateurs portables, en raison de leur énergie spécifique élevée et de leur haute tension. Cependant, dans des conditions abusives telles que le chauffage, la surcharge, la surdécharge, le court-circuit, les vibrations, la compression, etc., les batteries lithium-ion peuvent provoquer des incidents tels que des incendies, des explosions et même des blessures, ce qui a entraîné le rappel d'un grand nombre de batteries lithium-ion.
Par conséquent, l'amélioration des performances de sécurité des batteries lithium-ion est devenue une question clé dans leur développement. À l'heure actuelle, de nombreux pays ou instituts d'essai ont mis au point des méthodes d'essai de sécurité pour les batteries lithium-ion. Les batteries lithium-ion doivent passer des tests de sécurité afin de réduire les risques liés à leur utilisation. Les normes internationales relatives à la sécurité des batteries lithium-ion comprennent principalement IEC 62133, IEC 62281, UL 1642, UL 2054, UN 38.3, etc.
Dans les normes susmentionnées, le test d'impact d'objet lourd est un projet qui simule le court-circuit interne des batteries lithium-ion. Dans cet article, des tests d'impact d'objets lourds ont été réalisés sur différents modèles de batteries lithium-ion conformément aux exigences de la norme. Les résultats des tests ont été comparés et analysés en démontant la batterie après l'expérience.
1 Test
1.1 Équipement et environnement d'essai
L'instrument d'essai est la chambre d'essai d'impact antidéflagrante DGBELL. La température ambiante pendant l'expérience a toujours été maintenue à (20 ± 5) ℃.
1.2 Échantillons d'essai
Les échantillons de batteries lithium-ion utilisés dans cette expérience sont les suivants : batterie lithium-ion cylindrique 18650 ; Batterie carrée à coque en aluminium ; Batterie carrée lithium-ion polymère
1.3 Méthodes d'essai
Placez des batteries lithium-ion de différentes formes sur une surface plane, placez une tige de fer de 15,8 mm de diamètre horizontalement au centre de la batterie, et laissez un marteau de 9,1 kg tomber d'une hauteur de (610 ± 15) m sur la batterie. Les batteries carrées doivent également être tournées de 90° le long de l'axe long pour résister aux impacts lourds sur les surfaces larges et étroites. La température à la surface de la batterie pendant l'expérience est contrôlée par un thermocouple fixé à la surface de la batterie.
2 Résultats
2.1 Batteries lithium-ion 18650
Après avoir été frappée par un objet lourd, la surface de la batterie présente une profonde bosse, qui est principalement due à la compression de la tige de fer placée sur la surface de la batterie après avoir été frappée par un marteau lourd. De la rouille est apparue à la surface du pôle positif de la batterie, principalement en raison de l'ouverture de la soupape de décharge interne pendant le test d'impact, ce qui a provoqué l'écoulement d'une partie de l'électrolyte. L'électrolyte a produit des substances corrosives au contact de l'air, ce qui a entraîné la corrosion du capuchon du pôle positif.
Après avoir démonté le boîtier de la batterie, des fissures sont apparues à la surface des cellules de la batterie. Ces fissures sont principalement dues à l'extension et à la déformation des électrodes causées par la tige de fer qui comprime la batterie. L'élément de batterie a été déplié et l'électrode ainsi que le film d'ouverture se sont brisés à l'endroit où la tige de fer a été comprimée. Les matériaux de revêtement des électrodes positives et négatives se sont détachés.
2.2 Batterie carrée
(1) Batterie à coque en aluminium
Pour les batteries lithium-ion carrées, il existe généralement deux formes d'emballage : la coque en aluminium et l'aluminium-plastique.
La batterie présente également des bosses dues à la compression de la tige de fer et est devenue très mince au milieu. Après avoir démonté la coque en aluminium, on peut voir que les cellules internes de la batterie ont été divisées en deux moitiés. En dépliant l'élément de batterie, on constate que le revêtement du matériau de la batterie s'est décollé et que les électrodes sont plissées. Cela est dû à l'impact de la tige de fer sur l'intérieur de la batterie, qui génère une force d'écrasement dans le sens du plan. En outre, la grande dureté de la coque en aluminium empêche l'extension de la cellule de la batterie dans la direction horizontale, ce qui entraîne la formation de plis sur les électrodes.
Après le test de la surface étroite de la batterie carrée, la direction de la surface étroite de la batterie a été complètement comprimée et déformée. Après avoir démonté le boîtier de la batterie, on a constaté que les cellules internes de la batterie présentaient de graves fractures. En dépliant l'électrode, on a découvert que la matière active était tombée et que le diaphragme s'était rompu.
(2) Batteries lithium-ion-polymère
Pour les batteries lithium-ion-polymère emballées dans une coque en aluminium. Les résultats de l'épreuve de batterie sont similaires à ceux des batteries emballées dans une coque en aluminium. Cependant, en raison de l'étanchéité thermique de la coque en aluminium-plastique, les éléments internes de la batterie sont exposés à des forces externes après l'épreuve de la batterie. Deuxièmement, en raison de la faible épaisseur de la batterie emballée dans une coque en aluminium-plastique, celle-ci a été divisée en deux parties sous l'effet de l'impact externe.
2.3 Analyse des résultats des essais
Les résultats des essais ci-dessus montrent que l'essai d'impact sur objet lourd peut simuler le court-circuit interne des batteries lithium-ion. Dans l'essai d'impact d'objet lourd, la batterie a été soumise à des forces externes, ce qui a entraîné une déformation du boîtier de la batterie. La déformation de l'élément de la batterie entraîne une tension sur les électrodes et le séparateur. Sous l'action de cette tension, le matériau de l'électrode se détache et le diaphragme se rompt en raison de sa minceur, ce qui entraîne une conduction électronique directe entre les matériaux des électrodes positives et négatives, ou un contact entre le collecteur en cuivre (aluminium) et le matériau de l'électrode positive (négative) (c'est-à-dire un court-circuit interne), ce qui provoque localement un courant de décharge important et une chaleur ohmique.
Les courts-circuits internes se produisant à plusieurs endroits, la chaleur générée provoque d'autres réactions secondaires, telles que la décomposition de l'électrode et de l'électrolyte. Au cours de l'expérience, la température de la batterie a augmenté de manière significative. Pour le modèle de batterie lithium-ion 18650, un court-circuit interne a généré une quantité importante de gaz, provoquant une augmentation de la pression interne. Après avoir atteint une certaine valeur, la soupape de sûreté de la batterie s'est ouverte pour libérer le gaz acide, ce qui a permis d'éviter les accidents de sécurité. L'épaisseur des batteries lithium-ion carrées est relativement faible. En cas d'impact externe, la batterie peut se rompre ou se diviser en deux. Lorsqu'un court-circuit interne se produit, les composants internes de la batterie sont directement exposés à l'air et réagissent.
3 Conclusion
Les essais d'impact d'objets lourds sur différents types de batteries lithium-ion individuelles montrent que cette méthode d'essai peut simuler efficacement la situation de courts-circuits internes dans les batteries. L'analyse du démontage de différents types de batteries a révélé une rupture des électrodes et du diaphragme à l'intérieur des batteries, ce qui a entraîné des courts-circuits internes à l'intérieur des batteries. L'analyse et la compréhension de ce phénomène expérimental aideront davantage les fabricants de batteries à comprendre les normes d'essai des batteries, ce qui permettra d'améliorer la qualité des produits des batteries lithium-ion et de renforcer leur sécurité.