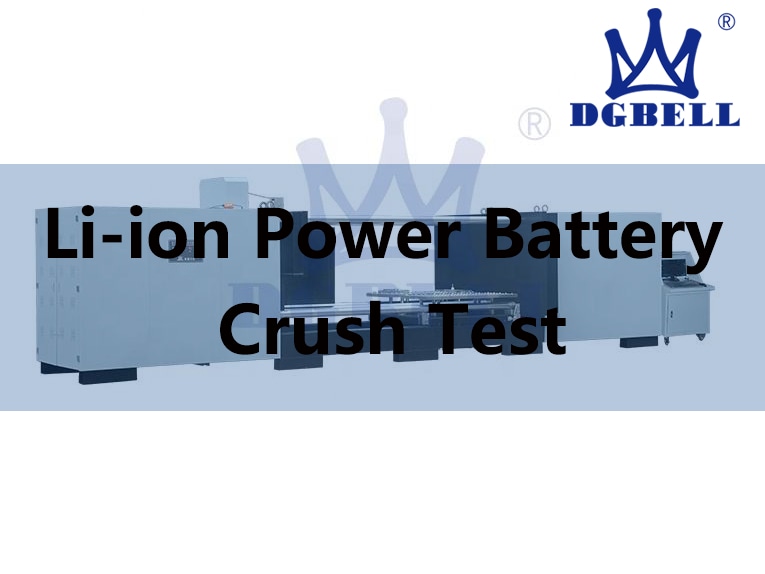
Voir la traduction automatique
Ceci est une traduction automatique. Pour voir le texte original en anglais cliquez ici
#Actualités du secteur
Test d'écrasement d'une batterie Li-ion - Partie 1
Test d'écrasement d'une batterie Li-ion - Partie 1
Guidés et soutenus par les politiques, les véhicules électriques sont entrés dans une période de développement rapide. Le gouvernement et les principaux fabricants de moteurs ont formulé des plans de développement correspondants pour les véhicules électriques. À l'avenir, les véhicules électriques remplaceront progressivement les véhicules à carburant traditionnels. Cependant, après une série de collisions, d'incendies et même d'explosions de véhicules électriques, la sécurité des véhicules électriques a été remise en question. Le véhicule électrique utilise principalement la batterie comme source d'énergie, ce qui entraîne une série de problèmes tels que le bloc-batterie, le faisceau de câbles haute et basse tension et la protection de l'extrémité de la charge. Cependant, en raison des caractéristiques de la haute tension intégrée et de l'énergie électrique élevée, la disposition de la batterie d'alimentation sur le véhicule et la protection contre les collisions doivent faire l'objet d'une attention particulière.
Les lois et réglementations existantes prévoient des normes de détection correspondantes pour les abus mécaniques des blocs-batteries. Cependant, dans des conditions routières réelles, les formes d'accidents automobiles sont différentes, et il existe un risque que les batteries soient écrasées après la collision des véhicules, entraînant un incendie et une explosion. Il est donc nécessaire d'étudier la sécurité des batteries en cas de collision.
Certains chercheurs ont étudié la sécurité des batteries à partir des composants utilisés dans les batteries, tels que les matériaux des électrodes, les séparateurs et les composants de l'électrolyte. Il existe également une série d'études expérimentales sur la batterie, telles que l'indentation, la flexion en trois points, l'acupuncture et les essais de chute de poids, afin d'explorer la réponse mécanique de la batterie sous charge. L'analyse de simulation de la structure de la batterie et de la performance en cas de collision des véhicules à énergie nouvelle est également réalisée, afin de fournir des orientations pour la conception de la sécurité structurelle des véhicules équipés de batteries d'alimentation.
Dans cet article, un certain type de batterie lithium-ion est pris comme objet de recherche, et le test d'extrusion est effectué dans différentes directions de la cellule. La collecte des données relatives à la pression d'extrusion, à la température et à la tension permet de déterminer la direction dans laquelle la résistance à l'extrusion de la cellule est la plus faible. Ensuite, la tolérance aux dommages causés par l'extrusion de la cellule est déterminée par l'analyse de différentes conditions de chargement. Ensuite, la capacité d'anti-extrusion des modules dans différentes directions est analysée.
1.Emballement thermique des batteries d'alimentation
Si l'on prend l'exemple des batteries lithium-ion, leur principal mécanisme de fonctionnement implique la délithiation et l'insertion de lithium dans les matériaux de la cathode et de l'anode, ainsi que la transmission et la diffusion d'ions lithium dans l'électrolyte (masse) et les matériaux du diaphragme. La plupart des problèmes de sécurité des piles électriques sont directement liés à la composition des matériaux de la pile. En raison d'abus mécaniques, tels que la surchauffe de la batterie, la surcharge, la décharge, l'impact, l'extrusion, etc., des réactions chimiques se produiront entre les matériaux internes de la batterie, ce qui entraînera un échauffement excessif et, en fin de compte, des incendies et des explosions.
Après un accident de voiture, la structure de la batterie se déforme sous l'effet des chocs et de la compression, ce qui entraîne la défaillance des matériaux des composants internes, notamment la rupture du diaphragme ou la rupture des matériaux de la cathode et de l'anode, ce qui provoque un court-circuit interne ; le court-circuit interne génère une grande quantité de chaleur par effet Joule, ce qui entraîne la décomposition des matériaux de la batterie. Lorsque la température est comprise entre 80 ℃ et 120 ℃, l'interface électrolyte solide (SEI) se décompose en premier.
Lorsque la réaction de décomposition de la membrane SEI progresse dans une certaine mesure, une série de réactions chimiques ultérieures se produisent. L'emballement thermique d'une batterie lithium-ion peut être divisé en cinq étapes de réaction en fonction de l'augmentation de la température : Réaction de décomposition de la membrane SEI, réaction de l'électrode négative et de l'électrolyte, réaction de décomposition de la substance active positive, réaction de l'adhésif et réaction de décomposition de l'électrolyte. La réaction de génération de chaleur à l'intérieur de la batterie produira également une grande quantité de gaz, et la pression à l'intérieur de la structure augmentera et s'accumulera rapidement ; lorsque la pression atteindra la limite de support de la structure, un incendie et une explosion pourront se produire. Lorsqu'une seule batterie tombe en panne, elle se propage rapidement aux batteries adjacentes, ce qui entraîne la défaillance du système de batteries et des conséquences plus graves.
Lorsque la batterie d'alimentation est court-circuitée, la tension commence à chuter et la température à augmenter, de sorte que la température et la tension peuvent être utilisées comme base de jugement pour la défaillance de la batterie d'alimentation. Étant donné que la température après un court-circuit interne ne peut être transférée à la surface de la batterie que pendant un certain temps et qu'elle est fortement influencée par la température ambiante, la tension est un paramètre qui permet de juger relativement rapidement et précisément la défaillance du court-circuit de la batterie de puissance. La valeur critique de la défaillance de l'extrusion de ce type de batterie peut être déterminée par l'augmentation de la température et le début de la chute de tension.
La figure 1 montre les données de température et de tension recueillies au cours du processus d'emballement thermique de la cellule pressée lors du test. Dans les 0~36s, la cellule est pressée dans une certaine mesure, la tension est toujours stable à 4,14V, et la température de la batterie est de 26,2 ℃ ; Pendant 37-38s, la tension tombe à 2mV, et la température de la batterie augmente à 30,5 ℃ ; Lorsque la charge atteint 50 s, la tension mesurée est toujours de 2 mV, et la température augmente à 131 ℃. À ce moment, on observe qu'une grande quantité de fumée est émise par la cellule ; Pendant 50~51s, la température de la batterie passe de 131 ℃ à 614 ℃, puis l'incendie et l'explosion se produisent.
La figure 2 montre le phénomène de fumée, d'incendie et d'explosion lorsque la chaleur d'extrusion d'une pile unique est incontrôlée lors de l'essai.
2.Test d'écrasement de la batterie d'alimentation
La batterie d'alimentation est généralement placée sous le plancher du véhicule. En cas de collision frontale ou arrière, il y a suffisamment d'espace d'absorption d'énergie devant et derrière le véhicule, la déformation structurelle du plancher est faible et le bloc-batterie ne sera pas endommagé par l'extrusion ; toutefois, lorsque le véhicule est soumis à un impact latéral, l'espace d'absorption d'énergie latérale est faible et la force d'impact est transmise à la poutre du plancher, au canal central et à d'autres zones par le biais du seuil. Le bloc-batterie est facilement écrasé et endommagé, ce qui endommage les modules internes et le monomère. Par conséquent, il peut servir de base à la conception d'un agencement sûr des blocs-batteries et à l'évaluation des défaillances dans la simulation afin de déterminer la tolérance aux dommages dus à l'extrusion des cellules individuelles en testant et en étudiant les dommages et les défaillances des cellules et des modules de la batterie dans des conditions d'extrusion.