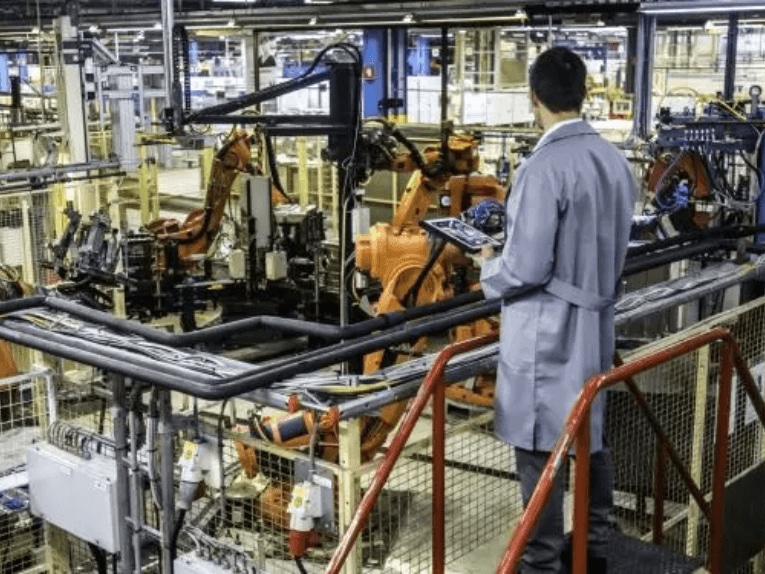
Voir la traduction automatique
Ceci est une traduction automatique. Pour voir le texte original en anglais cliquez ici
#Livres blancs
7 Les défis de la robotique industrielle
Coûts, inflexibilité, problèmes de sécurité, compétences de la main-d'œuvre, formation de la main-d'œuvre, gestion des flux de travail, dernières avancées.
Du simple bras robotique à la mise en œuvre généralisée, les robots industriels ont dû relever de nombreux défis, notamment des prix élevés et un matériel complexe. Les premiers exemples étaient entravés par leur infrastructure, devant s'appuyer sur des éléments tels que des chenilles, des rails ou des aimants. Ils dépendaient également de l'alimentation par batterie, ce qui limitait considérablement leur portée et leurs performances.
Au cours des deux dernières décennies, l'impulsion de l'industrie 4.0 a fait avancer les développements à un rythme beaucoup plus rapide. Cela ne veut pas dire que tout ira pour le mieux à partir de maintenant - et de nombreux défis en matière de robotique industrielle subsistent. Ces sept d'entre eux sont les plus courants :
Coûts
Les coûts élevés de la mise en œuvre constituent l'un des principaux défis de l'installation de la robotique industrielle. Le processus d'intégration initial risque d'être long, ardu et coûteux. Les spécifications des nouvelles tâches peuvent nécessiter un réaménagement de l'espace de travail et une réaffectation des travailleurs robotisés. Même des modifications mineures apportées à une chaîne de fabrication peuvent nécessiter l'intervention d'un intégrateur spécialisé.
Essayer de mettre en œuvre de nouveaux systèmes robotiques avec les infrastructures et les technologies existantes n'est pas facile pour les grandes entreprises. Les PME de plus petite taille trouvent souvent les coûts injustifiables ou prohibitifs. En outre, les volumes de production et les niveaux de vente doivent être maintenus pendant la période de retour sur investissement prévue pour amortir l'investissement initial.
Manque de flexibilité
Ce manque de coordination constitue un autre défi dans le domaine de la robotique industrielle. Un seul fabricant fournira non seulement son propre matériel, mais aussi ses propres solutions logicielles. De nombreuses interfaces de programmation d'applications sont alors nécessaires pour assurer la coordination entre les différents appareils, et peuvent même nécessiter un logiciel personnalisé. Les technologies robotiques actuelles ne peuvent pas toujours être facilement réutilisées, ce qui limite les rôles potentiels des robots. Même les travailleurs à la chaîne compétents et expérimentés sont souvent incapables d'améliorer les processus de fabrication par ce biais.
Une plus grande flexibilité permettrait aux systèmes robotiques de faire face à des temps d'intégration et de réintégration plus rapides et à la réutilisation des robots. Elle pourrait également permettre de reconfigurer les lignes de fabrication et les cellules de travail, ainsi que d'assurer une production à forte mixité et à faible volume. L'empreinte énergétique d'une usine pourrait être réduite en fabriquant plusieurs produits à l'aide d'une seule ligne de production.
Préoccupations en matière de sécurité
Les nouvelles technologies exigent de nouvelles procédures, qui introduisent immédiatement de nouveaux risques de sécurité sur le lieu de travail. Les robots industriels ne font pas exception à la règle et la sécurité des robots fait l'objet de réglementations strictes et de sanctions sévères.
Avant d'intégrer un système de robot industriel, les fabricants doivent s'y préparer et être prêts à créer un environnement sûr pour les travailleurs, qui garantisse une conformité totale. L'investissement dans les robots industriels serait encouragé si les fabricants pouvaient trouver un équilibre optimal entre la sécurité, la polyvalence et la rapidité.
Compétences de la main-d'œuvre
Les opérateurs doivent également acquérir un nouveau niveau d'expertise. Les travailleurs ne savent généralement pas comment faire fonctionner de nouveaux types d'équipements et, dans le cas des robots mobiles, ils ne savent pas comment se comporter correctement autour d'eux. Ils se mettent souvent en travers de la trajectoire d'un robot ou ne savent pas très bien comment répartir les activités entre les humains et les travailleurs automatisés.
La technologie étant encore relativement nouvelle, il n'existe pas de formation académique intégrée comme c'est le cas pour les compétences plus anciennes. De nombreux employés auront donc besoin d'une formation et, dans l'intervalle, il faudra engager d'autres personnes qui possèdent déjà la formation, les certifications et l'expérience requises.
Formation de la main-d'œuvre
Les robots industriels sont destinés à améliorer les performances globales d'une installation. Cela signifie qu'ils doivent interagir avec les humains dans une relation de dépendance mutuelle. Tant que le personnel n'aura pas acquis les compétences nécessaires, l'installation sera beaucoup moins efficace et donc moins rentable. Une formation de base à la robotique sensibilisera les employés au comportement des systèmes robotiques et à la manière dont les humains doivent réagir. L'efficacité globale peut être améliorée en démontrant la codépendance des humains et de la robotique industrielle.
Cela peut être facilité par l'utilisation d'analyses avancées et de la collecte de données pour identifier les problèmes clés. Les opérateurs doivent collecter autant de données que possible, y compris la nature et le nombre de trajets effectués par les systèmes robotiques, les temps d'arrêt dus aux erreurs et aux bogues, les temps de charge des batteries et le temps passé au ralenti. Grâce à ces informations, les opérateurs peuvent ajuster les processus nécessaires pour cibler les problèmes spécifiques et accroître l'efficacité des robots.
Gestion des flux de travail
Les flux de production doivent être évalués afin de déterminer les gains qui pourraient être réalisés grâce à l'intégration de robots. Il s'agit notamment de calculer la vitesse et l'orientation de la présentation des pièces aux robots afin de garantir une productivité maximale, sans surcharger les systèmes existants. Les données anecdotiques et expérientielles fournies par les travailleurs peuvent être soumises à l'analyse des données afin d'améliorer le flux de travail et d'évaluer la manière dont leurs contributions affectent les processus de conception et d'intégration. Cela pourrait également permettre d'évaluer l'effet global sur les performances et les cycles de production, afin d'éliminer l'inefficacité.
Dernières avancées
Bien qu'ils puissent servir toutes sortes d'objectifs, les enjeux de la robotique industrielle sont relativement similaires. Avec tous les développements technologiques de l'industrie 4.0 qui soutiennent les systèmes robotiques modernes, bon nombre de ces défis sont en train d'être relevés.
Grâce à une meilleure formation, les gens comprendront mieux le fonctionnement des plateformes robotiques. À long terme, davantage de personnes acquerront les compétences requises et pourraient apprendre à développer leurs propres plateformes robotiques. Des solutions de programmation utilisant des environnements à source ouverte, ainsi que des solutions sans code ou à faible code, sont en cours d'élaboration.
Les développeurs de robots commencent à se concentrer davantage sur la connaissance de la situation, avec des réseaux sensoriels complexes qui améliorent considérablement l'intelligence des cobots. Ils seront en mesure de mieux comprendre leur environnement et d'apprendre à se comporter avec les humains, tout comme ces derniers apprendront à se comporter avec eux. Le résultat net est une amélioration des interactions robotiques qui augmente la productivité et réduit les coûts.