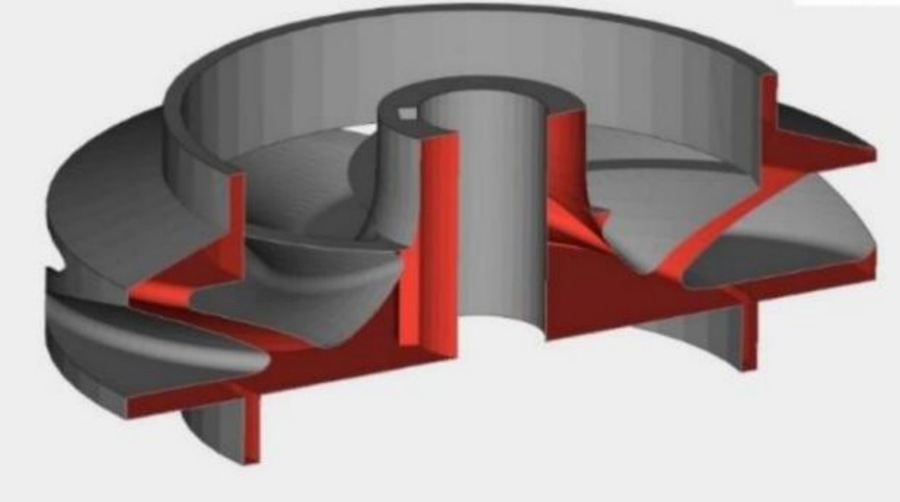
Voir la traduction automatique
Ceci est une traduction automatique. Pour voir le texte original en anglais cliquez ici
#Livres blancs
{{{sourceTextContent.title}}}
Étude de la fabrication d'une roue fermée en acier inoxydable 316L à l'aide d'une machine de fusion laser sur lit de poudre Eplus3D
{{{sourceTextContent.subTitle}}}
Nouvelles de l'entreprise
{{{sourceTextContent.description}}}
Yousef Alhorr1, Qusai Alkhalaf 2*
1PhD, président de l'Organisation du Golfe pour la recherche et le développement (GORD), QSTP, Doha, Qatar
2PhD, responsable des opérations du centre de fabrication additive. Organisation du Golfe pour la recherche et le développement (GORD-3D), QSTP, Doha, Qatar
Résumé : La fabrication de roues fermées au moyen de la technologie de fusion laser sur lit de poudre comporte des complexités inhérentes, exigeant une attention méticuleuse à la conception de la structure de support, à la détermination de l'angle de construction et à la densité d'énergie de la peau vers le bas pour garantir une production réussie. Cette étude explore l'utilisation de l'acier inoxydable 316L dans la fabrication de roues fermées à l'aide de la technologie LPBF. L'objectif est d'étudier l'impact des paramètres du processus et des angles de construction sur la qualité de fabrication des roues. En outre, elle étudie l'effet de la densité d'énergie sur la rugosité de la surface et les valeurs de dureté de la roue. L'étude examine des angles de construction de 0˚, 30˚ et 90˚ pour une roue fermée, révélant qu'un angle de construction de 30˚ permet d'obtenir des pièces imprimées réussies. De plus, pour obtenir des roues fermées sans défaut, il est impératif de maintenir la densité d'énergie de la peau vers le bas entre 80% et 100% de la densité d'énergie de la peau vers l'intérieur. La dureté maximale et la rugosité minimale de la surface ont été enregistrées à 233 HV et 12,79 µm, respectivement, lorsque la densité d'énergie était de 41,66 J/mm³ et 55,55 J/mm³ respectivement. La nouveauté de cette étude réside dans la fabrication de roues fermées en acier inoxydable 316L par fusion laser sur lit de poudre.
Mots-clés : fabrication additive ; fusion laser sur lit de poudre (LPBF) ; roue fermée ; fusion laser sélective (SLM)
1. Introduction
La roue constitue un élément indispensable dans les systèmes de pompage, jouant un rôle central dans la détermination de la capacité hydraulique et de l'efficacité du débit dans les turbomachines [1]. Distinguée par quatre classes géométriques, à savoir les roues ouvertes, fermées, semi-ouvertes et à vis, la roue fermée (CI) est particulièrement difficile à fabriquer en raison de ses caractéristiques internes complexes. Les méthodes traditionnelles consistent à assembler les roues à aubes fermées en segments, tels que l'enveloppe, le moyeu et les pales, en utilisant des techniques d'assemblage telles que le soudage, le brasage ou le rivetage. Cependant, ces approches introduisent des défauts et des distorsions, et s'avèrent inadéquates pour les applications exigeantes et à haute performance. Les techniques de fabrication telles que le moulage à la cire perdue, le fraisage intégral et l'usinage par décharge d'électrons (EDM) sont spécialisées mais prennent du temps, nécessitent une main-d'œuvre qualifiée et des installations spécialisées, ce qui augmente les coûts de fabrication globaux [2].
Face à ces défis, la fabrication additive (MA) apparaît comme une solution transformatrice pour les pièces uniques, offrant la possibilité d'atténuer les incertitudes liées aux délais et d'améliorer la flexibilité de la conception [3,4]. La fusion laser sur lit de poudre (LPBF), une technologie AM de premier plan, fait fondre sélectivement la poudre couche par couche à l'aide d'un laser, ce qui permet de produire des pièces de forme complexe avec une résolution élevée d'environ 50 micromètres [6-9]. Le LPBF a fait preuve d'un succès considérable dans l'impression de pièces complexes à partir d'un éventail de matériaux métalliques, y compris les aciers, les alliages de nickel, les alliages de titane et les alliages d'Inconel [10-11].
Bien que d'autres technologies telles que la méthode de dépôt par fusion (FDM) puissent être utilisées pour l'impression des roues, elles ne conviennent généralement qu'à des applications moins complexes [12]. En revanche, le LPBF avec impression métallique est indispensable pour obtenir des fonctionnalités de haute performance [13]. De nombreuses études soulignent l'application réussie du LPBF dans l'impression de roues ouvertes, comprenant des recherches sur les propriétés des matériaux, les prévisions de l'histoire thermique et l'optimisation des paramètres du processus [14-16]. De manière significative, le LPBF permet la fabrication de roues à partir de matériaux recyclés, ce qui accentue son potentiel en matière de pratiques de fabrication durables [17]. Malgré ces avancées, les défis persistants concernent la réalisation d'impressions 3D précises et sans défaut. La déformation géométrique, illustrée par des taches sombres et une liaison métallurgique sous-optimale entre les couches, contribue à des problèmes multiples, notamment des défaillances géométriques, des inexactitudes dimensionnelles, des structures incomplètes et des obstacles dans le processus d'impression [27]. En outre, les défauts de débris, résultant de la pression de recul de la vapeur de métal pendant l'impression, entraînent la rupture de la poudre non fusionnée ou du métal fondu et influencent l'état de fusion des couches successives, ce qui compromet finalement la résistance à la traction et la performance en fatigue de la pièce imprimée [28- 29].
L'acier inoxydable est largement considéré comme une excellente option pour l'impression par fusion sur lit de poudre laser. Une roue fermée en acier inoxydable a de nombreuses applications, notamment dans les systèmes de traitement des eaux usées. Les principales préoccupations liées à l'impression de l'acier inoxydable concernent la gestion de la densité d'énergie et l'optimisation de l'angle du matériau de support. La densité d'énergie est la mesure de l'énergie consommée par unité de volume au cours du processus de fusion de la couche. Plus précisément, la densité d'énergie est définie comme suit :
Dans l'équation, P (W) représente la puissance du laser, v désigne la vitesse de balayage (mm/s), h (μm) désigne la distance d'éclosion, z (μm) indique l'épaisseur de la couche, Les niveaux de faible énergie entraînent une porosité par manque de fusion, indiquant une énergie insuffisante pour une fusion complète de la poudre et entraînant des porosités irrégulières généralisées dans toute la pièce [31]. Les valeurs de densité énergétique élevées entraînent une sur-fusion, souvent appelée porosité en trou de serrure [32-34]. Dans cet état, les pistes fondues se fragmentent, entraînant une solidification non uniforme et des défauts dans la pièce finale. La région stable assure la fusion complète des pistes et la liaison des couches dans les limites de la densité d'énergie. La complexité de l'impression de la roue est essentielle dans la fusion laser sur lit de poudre, les métaux courants étant l'Inconel 625 et l'Inconel 718.
À la connaissance des auteurs, il existe une absence notable d'études concernant l'application de l'acier inoxydable 316L dans l'impression de roues fermées par fusion laser sur lit de poudre. Cette recherche vise donc à combler cette lacune en entreprenant la production d'une roue fermée par fusion laser sur lit de poudre. Notre principal objectif est d'analyser l'impact de variables telles que le matériau de support, l'angle de construction et la densité d'énergie de la peau inférieure sur le processus de fabrication de la roue fermée. En outre, nous voulons étudier l'effet de la densité d'énergie sur la rugosité et la dureté de la surface.
2. Méthode et travaux expérimentaux
La méthode et le travail expérimental appliqués ici pour étudier l'angle de la structure de support et les propriétés mécaniques finales de la roue sont illustrés à la figure 1. La méthode est divisée en trois phases. La première phase consiste à sélectionner l'angle approprié de la structure de support entre 0°, 30° et 90°. Une fois l'angle optimisé déterminé, la texture de la microstructure est examinée à l'aide d'un balayage MEB pour la phase 2. La phase III se concentre sur l'examen de l'effet de la densité d'énergie sur la rugosité et la dureté.
2.1 Conception de la roue
Deux tailles différentes de roues fermées ont été conçues : l'une d'un diamètre de 145 mm et l'autre d'un diamètre de 100 mm. La roue est divisée en trois sections principales le long de sa direction de construction : la base, la section médiane et la section des ailettes. Ces sections ont des structures complexes, y compris plusieurs géométries d'ailettes minces inclinées, ce qui rend la fabrication difficile. Comme la section transversale change le long de la hauteur de la roue, la zone balayée par le laser varie d'une couche à l'autre. La structure de la roue est illustrée à la figure 2.
2.2 Angle de construction et structure de support des roues fermées
Pour déterminer l'angle de construction optimal d'une roue fermée dans la chambre de construction de la machine LPBF, trois angles courants (90˚, 30˚ et 0˚) ont été sélectionnés afin d'évaluer leur impact sur le processus de fabrication. Le choix des supports dépend de la forme de la roue, avec des supports en forme de bloc, comme le montre la figure 3. De nombreuses études ont montré que l'utilisation de supports pleins ou en blocs permet d'améliorer les caractéristiques mécaniques des échantillons et la finition de la surface, en particulier pour les surfaces en surplomb. Ces supports facilitent la dissipation de la chaleur, optimisant ainsi les résultats. La figure 4 illustre la vue d'un support en bloc, avec des supports en arbre ajoutés pour faciliter le retrait. Le logiciel utilisé pour la préparation de la fabrication était MaterialsMagic pour la préparation des supports, et SolidWorks a été utilisé pour la conception.
2.3 Traitement LPBF
Les roues ont été fabriquées à l'aide d'une machine LPBF Eplus3D EP-M260, en utilisant de l'acier inoxydable 316L. La machine Eplus3D M260 est située au centre 3D de l'Organisation du Golfe pour la recherche et le développement (GORD 3D). La vue actuelle de la machine Eplus3D est présentée à la figure 5. Les roues ont été conçues avec des diamètres de 145 mm et 100 mm. L'impression d'une roue de 145 mm de diamètre à un angle de construction de 90˚ prend environ 103 heures et nécessite 4 393 couches d'une épaisseur de 30 µm. L'impression d'une roue de 145 mm de diamètre à un angle de construction de 30˚ prend 53 heures et nécessite 3 124 couches. Une roue de 100 mm de diamètre imprimée à un angle de construction de 0˚ prend environ 38 heures, avec 1 833 couches.
La sélection des paramètres d'impression des roues fermées est cruciale, la densité d'énergie étant un élément particulièrement important. La peau inférieure est située dans les trois premières couches au-dessus du matériau de support, ce qui peut potentiellement endommager la pièce pendant le processus d'impression. Il est donc essentiel de sélectionner parfaitement la densité d'énergie de la peau inférieure, car elle sert de pont entre le matériau de support et le cœur de la roue. La densité d'énergie de l'intérieur de la peau, quant à elle, concerne le cœur de la roue. D'après l'analyse de la littérature, la densité d'énergie de la peau inférieure devrait idéalement se situer entre 50 % et 80 % de la densité d'énergie de la peau intérieure. Dans la présente étude, deux cas sont envisagés pour la densité de la peau en aval : l'un où la densité énergétique de la peau en aval est égale à celle de la peau en amont, et l'autre où la densité énergétique de la peau en aval est fixée à 20 % de la densité énergétique de la peau en amont. La figure 6 présente la vue actuelle du processus d'impression. Le tableau 2 fournit des détails sur les paramètres du processus avec ces variations de densité d'énergie pour chaque phase.
2.4 Test de dureté
Les essais de microdureté Vickers ont été réalisés conformément à la norme ASTM E92-17 à l'aide d'une machine d'essai de microdureté Vickers. Un pénétrateur pyramidal à pointe de diamant a appliqué une force spécifiée (300 gf, 2,94 N) à la surface de l'échantillon pendant 10 secondes par indentation. Trois indentations ont été effectuées sur chaque échantillon, à l'exclusion de toute indentation à l'intérieur des pores. La valeur de dureté Vickers (HV) a été déterminée en mesurant les diagonales de chaque indentation en forme de diamant, dont la moyenne a été calculée à l'aide du logiciel de la machine.
2.5 Préparation de la surface et caractérisation microstructurale
Un échantillon de 5 mm d'épaisseur a été produit avec la roue. Les échantillons ont été abrasés à l'aide de disques abrasifs en carbure de silicium de différents niveaux de grosseur (200, 600, 800 et 1200 grains). Ces échantillons traités ont ensuite été examinés au microscope optique pour étudier les caractéristiques microstructurelles, notamment la poudre non fondue et les défauts. Ils ont ensuite été analysés à l'aide d'un MEB de bureau Phenom ProX pour étudier la sous-structure et la morphologie.
3. Résultats et discussion
3.1 Influence de l'angle de construction sur la construction de la roue
Les structures de support jouent un rôle essentiel dans la dissipation de la chaleur du bain de fusion, la réduction des contraintes thermiques et la compensation de la force de la lame de rechargement, qui exerce une pression dynamique contre le bord d'attaque de la couche. La conduction de la chaleur varie en fonction de la densité relative ; elle est nettement plus faible dans les couches de poudre à faible densité de tassement que dans les structures à support solide. Les différentes structures de support dissipent la chaleur à différents niveaux ; toutefois, une dissipation de chaleur plus importante, comme dans le cas des supports en blocs, rend l'enlèvement plus difficile. Les supports solides/blocs permettent d'obtenir des propriétés mécaniques et une finition de surface supérieures sur les surfaces en surplomb, bien qu'ils entraînent une augmentation des coûts liés aux matériaux, au temps d'impression et au post-traitement. Outre la dissipation de la chaleur, les structures de support soutiennent les pièces et neutralisent les forces de traction pendant le refroidissement rapide, réduisant ainsi les risques de déformation et de délamination. Un support insuffisant pour les surfaces orientées vers le bas entraîne des problèmes de forme et de précision dimensionnelle. Par conséquent, la sélection des paramètres pour les couches de support et de peau inférieure est cruciale pour atténuer les contraintes internes et la délamination. Il est essentiel de déterminer un "angle de construction fiable", c'est-à-dire l'angle minimal garantissant la production de pièces sans formation de crasse et sans détachement.
Comme décrit dans la section des méthodes, la roue a été examinée à trois angles de construction pendant la construction : 90°, 30° et 0°. Dans le cas du CI-A, une défaillance importante de la roue s'est produite, attribuée à la faiblesse des structures de support choisies avant le processus, comme le montre la figure 7. La combinaison du support de bloc et du support d'arbre s'est avérée inadéquate pour supporter le poids de la roue, entraînant une déformation de la structure de support, particulièrement visible à un angle de construction de 90˚. La déformation observée peut être attribuée au poids important exercé par la pièce construite et le dispositif de recouvrement pendant le processus d'impression. Le dispositif de recouvrement, en particulier, joue un rôle essentiel dans le processus de stratification en étalant la poudre sur le lit de construction. Toutefois, cette action répétitive, en particulier lors de l'application des couches suivantes, peut exercer une force excessive, entraînant des dommages, en particulier aux angles de 90° où les bords de la pièce imprimée sont intrinsèquement plus faibles.
Dans les cas de CI-B et CI-C, on a observé une construction réussie de la roue avec moins de défauts. La production d'une roue plus petite et plus grande avec un angle de construction de 30˚ réduit considérablement les défauts et les dommages au cours du processus de fabrication, affichant des résultats supérieurs à ceux des cas où l'angle de construction est fixé à 90˚ . Ce phénomène est clairement illustré dans la figure 8. L'angle de construction de 30˚ n'a provoqué aucun dommage, ce qui a permis de réduire le poids de la pièce imprimée et d'améliorer les performances du dispositif de recouvrement. Avec un angle de 30°, le dispositif de recouvrement entre en contact avec moins de poudre le long des bords qu'avec des angles de 90° et 0° lors de chaque mouvement d'étalement. Le succès de l'orientation à 30° est attribué à plusieurs facteurs clés. Tout d'abord, la transition progressive de la section transversale entre les supports et les pièces solides au sein de chaque couche minimise les concentrations de contraintes et les défauts potentiels, ce qui la distingue d'orientations telles que 0° où des changements brusques se produisent. Deuxièmement, l'absence de supports solides généralement requis pour les surplombs dans des orientations telles que 90 degrés a contribué de manière significative au succès de l'orientation à 30 degrés. Cette élimination des supports a non seulement permis de rationaliser le processus d'impression, mais aussi d'atténuer les problèmes liés au post-traitement et aux imperfections de surface, ce qui a permis d'améliorer la qualité et l'intégrité structurelle des pièces. En outre, il a été observé que les pièces imprimées avec une orientation de 30 degrés présentaient un poids réduit par rapport à celles imprimées avec une orientation de 90 degrés. Cette réduction de poids, bien qu'avantageuse dans diverses applications, a encore souligné l'efficacité de l'orientation à 30 degrés. Collectivement, ces résultats mettent en évidence les avantages multiples de l'orientation à 30 degrés dans la fabrication additive, offrant des indications précieuses pour l'optimisation des stratégies d'orientation dans les applications futures.
Dans le cas du CI-D, lorsque la roue fermée est petite, l'échec s'est produit lorsque l'angle de construction était de 0˚ . Malgré la petite taille du CI, la défaillance à cet angle n'était pas due à sa taille, mais plutôt attribuée à la faiblesse de la structure de support, comme le montre la figure 9. En outre, l'utilisation d'une vitesse de balayage élevée de 900 mm/s a entraîné une accumulation de débris sur la surface de la roue, comme le montre la figure 9. En outre, des dommages ont été observés le long de la bordure, causés par les réglages à haute puissance dans ces régions.
3.2 Impact des paramètres de la couche de fond sur la construction de la roue fermée
Le revêtement inférieur désigne généralement des couches, allant de 1 à 4, placées au-dessus des supports ou directement sur la poudre. Habituellement, trois couches sont identifiées comme des couches inférieures et nécessitent des paramètres de traitement distincts par rapport aux couches "intérieures" ou "centrales". Les paramètres liés à la couche inférieure, tels que la vitesse et la puissance de balayage, sont considérés comme essentiels pour la construction de toute pièce utilisant la technologie de fusion laser sur lit de poudre. Lorsque la densité d'énergie de la peau inférieure ne représente que 20 % de la densité d'énergie de la peau intérieure, la pièce subit des dommages notables. Même dans les cas où aucun dommage n'est observé, des signes de brûlure et des défauts se manifestent à la surface de la roue fermée, particulièrement évidents dans les grandes roues fermées telles que CI-A, comme le montre la figure 7. Cela souligne l'importance de deux facteurs principaux contribuant à la défaillance de la pièce : l'inadéquation de la structure de support et la densité d'énergie insuffisante de la peau du bas, qui mesure 12,15 J/mm³.
À mesure que le diamètre de la roue diminue, comme dans le cas d'une roue de 100 mm de diamètre, l'impact de la peau inférieure diminue, notamment à un angle de construction de 30˚ . Bien que la densité d'énergie de la peau inférieure ne représente que 20 % de la densité d'énergie de la peau intérieure, des brûlures mineures peuvent encore être observées dans des zones spécifiques de la pièce imprimée, comme le montre la figure 10. En outre, l'augmentation du diamètre de la roue augmente la probabilité d'endommagement de la pièce. Cependant, l'alignement de la densité d'énergie de la peau inférieure avec la densité d'énergie de la peau intérieure à un angle de 30˚ garantit une impression réussie de la roue sans défauts, comme le montre la figure 10.
La densité d'énergie sous la peau est un paramètre crucial dans le processus de construction des pièces, déterminé par la complexité et la taille de la pièce. Pour les petites pièces, son impact est moins prononcé que pour les grandes. Pour obtenir des pièces exemptes de défauts, la densité d'énergie de la peau inférieure devrait idéalement se situer entre 80 et 100 % de la densité d'énergie de la peau intérieure.
3.3 Effet de la densité d'énergie volumétrique (DEV) sur la microstructure de la roue à aubes
La roue imprimée avec une densité d'énergie de 35 J/mm³, considérée comme faible, présente un manque de fusion attribué à la vitesse de balayage élevée, qui fait que le laser n'a pas assez de temps pour faire fondre la poudre, comme le montre la figure 11. En augmentant la densité d'énergie à 55,55 J/mm³, ces problèmes de manque de fusion et de manque d'adhésivité sont réduits grâce à la densité d'énergie optimale, ce qui permet à la poudre de fondre correctement, comme l'illustre la figure 12.
3.4 Influence de la DVE sur la dureté
Les mesures de dureté Vickers des échantillons imprimés varient approximativement entre 226 et 233 HV. Deux échantillons, caractérisés par une densité d'énergie volumétrique (DEV) de 40 J/mm³, présentaient des valeurs de dureté inférieures à 230 HV. Il s'agit des échantillons CI-C-1 et CI-C-2, dont les densités d'énergie sont respectivement de 33,33 J/mm³ et 37,037 J/mm³. La majorité des échantillons se situent entre 220 et 230 HV, comme le montre le tableau 3. Notamment, l'échantillon CI-C-3, qui possède une DVE de 41,66 J/mm³, présente la dureté la plus élevée, soit 233 HV.
Les valeurs de dureté Vickers (HV) obtenues étaient comparables à celles des pièces en 316L fabriquées par coulée, qui présentent généralement une dureté de 210 HV. Cependant, les autres valeurs étaient supérieures à cette référence. On observe que plus un échantillon est poreux, plus sa dureté est faible, car la présence de pores permet aux indentations de pénétrer plus profondément, ce qui se traduit par des indentations plus grandes et, par conséquent, par des valeurs HV plus faibles. Dans cette expérience, des efforts intentionnels ont été faits pour éviter les pores de surface lors de chaque indentation, ce qui a entraîné une corrélation minimale entre la dureté et la porosité de surface.
3.5 Rugosité de la surface
La rugosité de la surface est un paramètre important dans la fusion laser sur lit de poudre, influencée par la densité d'énergie. L'augmentation de la densité d'énergie entraîne généralement une réduction de la rugosité moyenne de la pièce. Cette réduction est due au fait qu'une densité d'énergie plus élevée permet une exposition plus prolongée à une énergie élevée et à une vitesse faible, ce qui facilite la fusion de la poudre au cours du processus. En outre, la diminution de la vitesse de balayage augmente la densité d'énergie, réduisant ainsi l'effet de bille pendant le traitement, ce qui contribue encore à réduire la rugosité de la surface. Par exemple, dans la figure 13, la rugosité de surface maximale est observée à 13,82 µm lorsque la densité d'énergie est faible. Cependant, l'augmentation de la densité d'énergie à 55 J/mm3 entraîne une diminution de la rugosité de surface à 12,79 µm.
3.6 Comparaison avec l'étude précédente
Les résultats ont été comparés à la revue de la littérature basée sur l'essai de dureté, en particulier en les comparant à Eliasu et al[35]. En ce qui concerne les propriétés mécaniques, nous avons observé de petites différences dans l'essai de dureté par rapport à Eliasu et al[35], avec un changement de valeur entre 2 et 5 HV, comme le montre le tableau 4. En comparant la microstructure, on remarque que la microstructure d'Eliasu et al [35] est meilleure que notre résultat actuel, ce qui peut avoir causé les changements de dureté observés, comme le montre la figure 17.
4. Conclusions
L'impression d'une roue fermée par fusion laser sur lit de poudre nécessite une prise en compte minutieuse des paramètres d'impression afin d'atténuer les complexités associées au processus d'impression. Il s'agit notamment d'une conception subtile pour une sélection appropriée de l'angle de construction et de l'utilisation d'une densité d'énergie adéquate de la peau inférieure pour une fabrication réussie. Dans cette étude, l'acier inoxydable 316L est utilisé pour fabriquer la roue fermée grâce à la technologie LPBF. Pour obtenir des pièces imprimées réussies et améliorer la qualité globale des roues fermées, une combinaison optimale de plusieurs facteurs cruciaux doit être assurée.
- L'utilisation d'une roue plus petite et plus grande avec un angle de construction de 30˚ réduit considérablement les défauts et les dommages au cours du processus de fabrication, et donne des résultats supérieurs à ceux obtenus lorsque l'angle de construction est fixé à 90˚ .
- L'alignement de la densité d'énergie de la peau vers le bas avec la densité d'énergie de la peau vers l'intérieur à un angle de 30˚ garantit une impression réussie de la roue sans défauts.
- Lorsque la densité d'énergie de la peau inférieure ne représente que 20 % de la densité d'énergie de la peau intérieure, la pièce subit des dommages notables. Même dans les cas où aucun dommage n'est observé, des signes de brûlure et des défauts se manifestent sur la surface de la roue fermée, particulièrement évidents pour les roues fermées de grande taille.
- L'augmentation de la densité d'énergie à 55,55 J/mm3 entraîne une réduction de la poudre non fondue au cours du processus.
- L'augmentation de la densité d'énergie diminue la rugosité de la surface à 12,79 µm lorsque la densité d'énergie est de 55 J/mm3.
- La dureté de la roue varie entre 226 et 233 HV, atteignant un maximum à 233 HV lorsque la densité d'énergie est de 41,66 J/mm3.
Références
[1] P. Sulzer, Physical Principles, Centrifugal Pump Handbook, 2010, pp. 1-26.
[2] J.J.M. Timothy, C. Allison, Aaron M. Rimpel, Jason C. Wilkes, Robert Pelton, Karl Wygant,
Manufacturing and Testing Experience with Direct Metal Laser Sintering for Closed Centrifugal Compressor Impellers, 43rd Turbomachinery & 30th Pump Users Symposia, Pump & Turbo 2014, Houston, TX, 2014.
[3] A.A. Scot Laney, Derrick Bauer, Evaluation of Various Methods for Manufacturing One Piece, Small Tip Opening Centrifugal Compressor Impellers, Asia Turbomachinery and Pump Symposium, Marina Bay
Sands, Singapour, 2016.
[4] Meli, E. ; Rindi, A. ; Ridolfi, A. ; Furferi, R. ; Buonamici, F. ; Iurisci, G. ; Corbò, S. ; Cangioli, F. Design and Production of Innovative Turbomachinery Components via Topology Optimization and Additive
Manufacturing. Int. J. Rotating Mach. 2019, 2019, 1-12, https://doi.org/10.1155/2019/9546831.
[5] Lezama-Nicolás, R. ; Rodríguez-Salvador, M. ; Río-Belver, R. ; Bildosola,I. Une méthode bibliométrique pour évaluer la maturité technologique : le cas de la fabrication additive. Scientometrics 2018, 117, 1425- 1452, https://doi.org/10.1007/s11192-018-2941-1.
[6] Aota, L.S. ; Bajaj, P. ; Sandim, H.R.Z. ; Jägle, E.A. Laser Powder-Bed Fusion as an Alloy Development Tool : Parameter Selection for In-Situ Alloying Using Elemental Powders. Materials 2020, 13, 3922, doi:10.3390/ma13183922.
[7] Keshavarzkermani, A. ; Marzbanrad, E. ; Esmaeilizadeh, R. ; Mahmoodkhani, Y. ; Ali, U. ; Enrique, P.D. ; Zhou, N.Y. ; Bonakdar, A. ; Toyserkani, E. An investigation into the effect of process parameters on melt pool geometry, cell spacing, and grain refinement during laser powder bed fusion. Opt. Laser
Technol. 2019, 116, 83-91, https://doi.org/10.1016/j.optlastec.2019.03.012.
[8] Qu, S. ; Ding, J. ; Fu, J. ; Fu, M. ; Zhang, B. ; Song, X. High-precision laser powder bed fusion processing of pure copper. Addit. Manuf. 2021, 48, https://doi.org/10.1016/j.addma.2021.102417.
[9] Huang, S. ; Narayan, R.L. ; Tan, J.H.K. ; Sing, S.L. ; Yeong, W.Y. Resolving the porosity-unmelted
pendant l'alliage in situ de Ti34Nb par fusion laser sur lit de poudre. Acta Mater. 2020, 204, 116522, https://doi.org/10.1016/j.actamat.2020.116522.
[10] Mukherjee, T., Wei, H.L., De, A. et DebRoy, T., 2018. Heat and fluid flow in additive manufacturing- Part II : Powder bed fusion of stainless steel, and titanium, nickel and aluminum base alloys.
Computational Materials Science, 150,pp.369-380.
[11] Aota, L.S. ; Bajaj, P. ; Sandim, H.R.Z. ; Jägle, E.A. Laser Powder-Bed Fusion as an Alloy Development Tool : Parameter Selection for In-Situ Alloying Using Elemental Powders. Materials 2020, 13, 3922, doi:10.3390/ma13183922.
[12] Fernández, S. ; Jiménez, M. ; Porras, J. ; Romero, L. ; Espinosa, M.M. ; Domínguez, M. Additive
Manufacturing and Performance of Functional Hydraulic Pump Impellers in Fused Deposition Modeling Technology. J. Mech. Des. 2015, 138, 024501, https://doi.org/10.1115/1.4032089.
[13] Ponticelli, G.S. ; Tagliaferri, F. ; Venettacci, S. ; Horn, M. ; Giannini, O. ; Guarino, S. Re-Engineering of an Impeller for Submersible Electric Pump to Be Produced by Selective Laser Melting. Appl. Sci. 2021, 11, 7375, https://doi.org/10.3390/app11167375.
[14] Mikula, J. ; Ahluwalia, R. ; Laskowski, R. ; Wang, K. ; Vastola, G. ; Zhang, Y.-W. Modélisation de l'influence des paramètres du processus sur la formation de précipités dans la fabrication additive par fusion sur lit de poudre de l'IN718
IN718. Mater. Des. 2021, 207, 109851, https://doi.org/10.1016/j.matdes.2021.109851.
[15] O'brien, J. ; Montgomery, S. ; Yaghi, A. ; Afazov, S. Process chain simulation of laser powder bed fusion including heat treatment and surface hardening. CIRP J. Manuf. Sci. Technol. 2021, 32, 266-276,
https://doi.org/10.1016/j.cirpj.2021.01.006.
[16] Yavari, R. ; Williams, R. ; Riensche, A. ; Hooper, P.A. ; Cole, K.D. ; Jacquemetton, L. ; Halliday, H.(. ; Rao, P.K. Thermal modeling in metal additive manufacturing using graph theory - Application to laser powder bed fusion of alarge volume impeller. Addit. Manuf. 2021, 41, 101956,
https://doi.org/10.1016/j.addma.2021.101956.
[17] Tupac-Yupanqui, H. ; Armani, A. Additive Manufacturing of Functional Inconel 718 Parts from Recycled Materials. J. Mater. Eng. Perform. 2021, 30, 1177-1187, https://doi.org/10.1007/s11665-020-05402-8.
[18] Kladovasilakis, N. ; Kontodina, T. ; Charalampous, P. ; Kostavelis, I. ; Tzetzis, D. ; Tzovaras, D. A Case Study on 3D Scanning, Digital Reparation and Rapid Metal Additive Manufacturing of a Centrifugal Impeller. In Proceedings of the 24th Innovative Manufacturing Engineering and Energy International Conference (IManEE), Athènes, Grèce, 14-15 décembre 2020, https://doi.org/10.1088/1757-
899x/1037/1/012018.
[19] Tian, Y. ; Ren, H. ; He, J. ; Zha, X. ; Lin, K. ; Zhou, M. ; Xiong, Y. Surface roughness improvement of Ti- 6Al-4V alloy overhang structures via process optimization for laser-powder bed fusion. J. Manuf.
Process. 2024, 110, 434-446, https://doi.org/10.1016/j.jmapro.2024.01.008.
[20] Guo, J. ; Wang, Y. ; Wang, Y. ; Peng, S. ; Wang, F. Simulation Study on the Energy Utilization Efficiency of a Turbine Impeller Based on a Selective Laser Melting Process. Appl. Sci. 2023, 13, 10657,
https://doi.org/10.3390/app131910657.
[21] Yaghi, A. ; Ayvar-Soberanis, S. ; Moturu, S. ; Bilkhu, R. ; Afazov, S. Design against distortion for additive manufacturing. Addit. Manuf. 2019, 27, 224-235, https://doi.org/10.1016/j.addma.2019.03.010.
[22] Kumar, A. ; Shandiz, M.A. ; Sikan, F. ; Brochu, M. Microstructural and mechanical properties of an internal support-free IN625 closed impeller manufactured via laser powder bed fusion (L-PBF). Mater. Sci. Eng.
A 2023, 874, https://doi.org/10.1016/j.msea.2023.145080.
[23] O.D. Ian Campbell, Kowen Joseph, Wohlers Terry, 3D Prinitng and Additive Manufacturing Global State of the Industry, Wholers Report, Wholers Associates, 2018.
[24] Herzog, D. ; Asami, K. ; Scholl, C. ; Ohle, C. ; Emmelmann, C. ; Sharma, A. ; Markovic, N. ; Harris, A. Design guidelines for laser powder bed fusion in Inconel 718.J. Laser Appl. 2022, 34, 012015,
https://doi.org/10.2351/7.0000508.
[25] Rebaioli, L. ; Fassi, I. A review on benchmark artifacts for evaluating the geometric performance of additive manufacturing processes. Int. J. Adv. Manuf. Technol. 2017, 93, 2571-2598,
https://doi.org/10.1007/s00170-017-0570-0.
[26] Yang, S. ; Tang, Y. ; Zhao, Y.F. A new part consolidation method to embrace the design freedom of
de la fabrication additive. J. Manuf. Process. 2015, 20, 444-449, https://doi.org/10.1016/j.jmapro.2015.06.024.
[27] Grasso, M. ; Laguzza, V. ; Semeraro, Q. ; Colosimo, B.M. In-Process Monitoring of Selective Laser
Melting : Spatial Detection of Defects Via Image Data Analysis. J. Manuf. Sci. Eng. 2016, 139, 051001, https://doi.org/10.1115/1.4034715.
[28] Li, J. ; Cao, L. ; Xu, J. ; Wang, S. ; Zhou, Q. In situ porosity intelligent classification of selective laser melting based on coaxial monitoring and image processing. Measurement 2021, 187, 110232,
https://doi.org/10.1016/j.measurement.2021.110232.
[29] Leung, C.L.A. ; Marussi, S. ; Atwood, R.C. ; Towrie, M. ; Withers, P.J. ; Lee, P.D. In situ X-ray imaging of
des défauts et de la dynamique du bain de fusion dans la fabrication additive par laser. Nat. Commun. 2018, 9, 1-9, https://doi.org/10.1038/s41467-018-03734-7.
[30] Cacace, S. ; Pagani, L. ; Colosimo, B.M. ; Semeraro, Q. L'effet de la densité d'énergie et de la structure de la porosité
on tensile properties of 316L stainless steel produced by laser powder bed fusion. Prog. Addit. Manuf. 2022, 7, 1053-1070, https://doi.org/10.1007/s40964-022-00281-y.
[31] Sun, Z.J. ; Tan, X.P. ; Tor, S.B. ; Yeong, W.Y. Selective laser melting of stainless steel 316L with low
porosité et des taux de construction élevés. Mater. Des. 2016, 104, 197-204, https://doi.org/10.1016/j.matdes.2016.05.035.
[32] Clijsters S, Craeghs T, Buls S, Kempen K, Kruth JP (2014) In situ quality control of the selective laser melting process using a high-speed, real-time melt pool monitoring system. Int J Adv Manuf Technol. https:// doi. org/ 10. 1007/ s00170-014-6214-8
[33] Lippolis, V., Irurhe, O., Porricelli, A. C. R., Cortese, M., Schena, R., Imafidon, T., et al. (2017). Cooccurrence naturelle d'aflatoxines et d'ochratoxine A dans le gingembre (Zingiber officinale) du Nigéria. Food control 73, 1061-1067. https://doi.org/10.1016/j. foodcont.2016.10.026
[34] Gu, D. ; Shen, Y. Balling phenomena in direct laser sintering of stainless steel powder : Metallurgical mechanisms and control methods. Mater. Des. 2009, 30, 2903-2910,
https://doi.org/10.1016/j.matdes.2009.01.013.
[35] Eliasu, A. ; Czekanski, A. ; Boakye-Yiadom, S. Effect of laser powder bed fusion parameters on the
microstructural evolution and hardness of 316L stainless steel. Int. J. Adv. Manuf. Technol. 2021, 113, 2651-2669, https://doi.org/10.1007/s00170-021-06818-9.