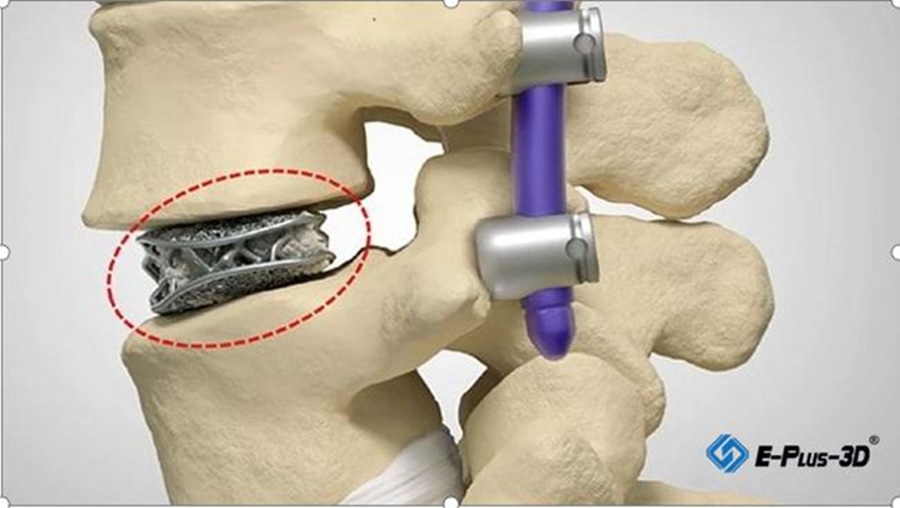
Voir la traduction automatique
Ceci est une traduction automatique. Pour voir le texte original en anglais cliquez ici
#Actualités du secteur
Fabrication d'implants rachidiens à l'aide de l'imprimante 3D métal EP-M250
Les imprimantes 3D en métal Eplus3D offrent des solutions pour les implants rachidiens
Personnalisation de la transformation par fabrication additive
La technologie de la fabrication additive ne cesse de progresser, tout comme ses applications et son accessibilité. Le prototypage rapide et l'outillage sont à l'avant-garde de l'impression 3D, mais l'objectif a toujours été de pouvoir imprimer directement pour la production ou directement pour la fabrication. Le monde médical ne fait pas exception. Bien que les premières applications de l'impression 3D dans le domaine médical aient été des prototypes et des guides de visualisation, cette technologie a finalement atteint le stade des implants personnalisés grâce à des imprimantes 3D de pointe.
Eplus3D reste fidèle à sa vision de fournir une solution 3D personnalisée pour tous. Avec sa dernière gamme d'imprimantes 3D métal, Eplus3D attire l'attention des partenaires médicaux qui tirent incroyablement parti de cette technologie. L'un des partenaires pionniers dans la création et l'utilisation d'implants médicaux est MANTIZ.
MANTIZ est une société de dispositifs médicaux qui utilise une ingénierie et une technologie supérieures pour permettre à tous les patients souffrant de troubles de la colonne vertébrale de mener une vie active et sans douleur. MANTIZ a obtenu la certification KFDA (approbation des dispositifs médicaux) et figure sur la liste HIRA (Health Insurance Review and Evaluation) en Corée du Sud. MANTIZ a commencé à développer des implants de cage imprimés en 3D en 2018 avec l'approbation et le financement du gouvernement. En mai 2019, ils ont lancé un système de cage PANTHER imprimé en 3D pour la chirurgie PLIF (Poster Lumbar Interbody fusion) / TLIF / OLIF / ALIF. Ce procédé utilise des implants de cage imprimés en 3D sans externaliser le processus de fabrication à un tiers. Cela permet aux clients d'économiser du temps et de l'argent et de réduire les risques d'erreurs de production. MANTIZ utilise l'imprimante 3D métallique EP-M250 d'Eplus3D pour fabriquer des cages imprimées en 3D en titane qui seront utilisées pour la chirurgie implantaire. L'ensemble du processus de mise en forme de l'implant est réalisé en interne par MANTIZ. La cage est conçue selon un cahier des charges. La taille, le matériau, la forme et la porosité sont essentiels à l'efficacité de l'implant. La conception complète de la cage est chargée dans le logiciel de l'imprimante, où elle est prête à être imprimée. Le grand lit d'impression de l'EP-M250 peut être utilisé pour imprimer plus de 50 implants individuels dans une structure. Lors de la transplantation, l'os et les tissus environnants commencent à fusionner avec l'implant, créant ainsi une structure solide dans la colonne vertébrale du patient. Hongwon Yoon (directeur technique de MANTIZ), l'inventeur du système de cage à imprimer en 3D PANTHER de MANTIZ, a déclaré : "Nous avons terminé le développement d'un implant de cage en titane imprimé en 3D plus amélioré à l'aide de l'imprimante 3D pour métaux EP-M250. Les résultats des tests mécaniques prouvent la sécurité et la fonctionnalité de l'implant. Impression 3D Le ratio moyen de pores fermés du composant solide en titane est de 3 %, ce qui favorise la liaison de la protéine de fusion osseuse aux cellules souches mésenchymateuses."
Veuillez consulter les images ci-dessous pour voir l'ensemble du processus, de la conception à l'impression, de l'impression à l'incorporation. Le monde de l'impression 3D est en constante évolution, et à mesure que la technologie progresse, l'application directe fait de même. La personnalisation au bout des doigts, plus abordable que jamais. Les secteurs de l'automobile, de l'aérospatiale et de la médecine utilisent désormais l'impression 3D directement en production, ce qui ne représente qu'une partie des capacités de cette technologie. Contactez directement Eplus3D (info@eplus3d.com) pour plus d'informations sur la manière d'intégrer la fabrication additive dans votre flux de travail quotidien.
Conception 3D et processus d'impression :
Conception intégrée avec un logiciel 3D professionnel
Préparation des pièces dans un logiciel d'impression 3D
Utilisation de l'EP-M250 d'Eplus3D pour l'impression 3D
Processus d'impression 3D du métal dans la chambre
Cages imprimées en 3D
Post-traitement comprenant le traitement thermique, le retrait des supports, le traitement de surface, la désinfection, etc.
Ce n'est qu'après une série de tests mécaniques que la cage imprimée en 3D peut être utilisée en chirurgie
Grâce au processus "conception-impression 3D-post-traitement-tests", le PANTHER peut être prêt pour la chirurgie. Actuellement, le PANTHER a déjà été utilisé pour le traitement de patients.
Avantage de la cage en titane imprimée en 3D :
PANTHER a été formulé pour optimiser la croissance osseuse pendant les procédures vertébrales, avec une gamme de taille de pores moyenne de 630-730μm dans la surface de contact des plaques d'extrémité vertébrales et une porosité moyenne de la section de la maille dans la gamme de 70% -80%.
Le potentiel est moyen
À propos d'Eplus3D
Eplus3D a été fondée en 2014, l'équipe technique centrale a plus de 25 ans d'accumulation de la technologie AM, a été engagée dans la recherche et le développement de systèmes de fabrication additive de qualité industrielle et de technologies d'application, avec MPBF™ (Metal Powder Bed Fusion) , PPBF™ (Polymer Powder Bed Fusion) et la technologie d'impression 3D de stéréo-lithographie, fournit des solutions d'application professionnelles pour les domaines de l'aérospatiale, de l'automobile, de l'outillage, de la santé, du dentaire, des biens de consommation, de la fabrication de précision, etc.
Eplus3D dispose de deux sites à Pékin et à Hangzhou, avec un investissement annuel dans la recherche scientifique de plus de 20 % du chiffre d'affaires et des brevets d'invention, des brevets de modèle d'utilité, des droits d'auteur de logiciel et des brevets d'apparence. Elle a réalisé de grandes avancées dans la conception, l'équipement, le processus, le logiciel, les matériaux et le post-traitement pour la fabrication additive, avec des équipements exportés dans plus de 40 pays et régions tels que l'Europe, l'Amérique, le Japon, la Corée du Sud et l'Asie du Sud-Est, etc.
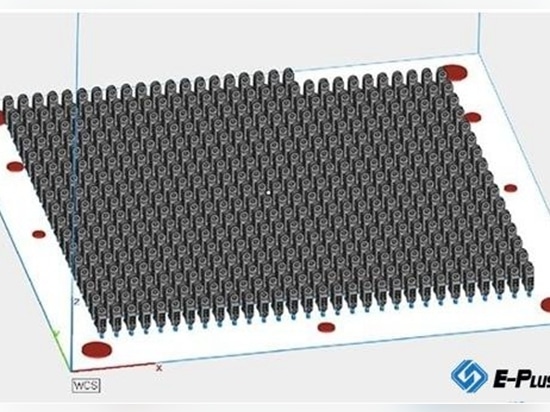
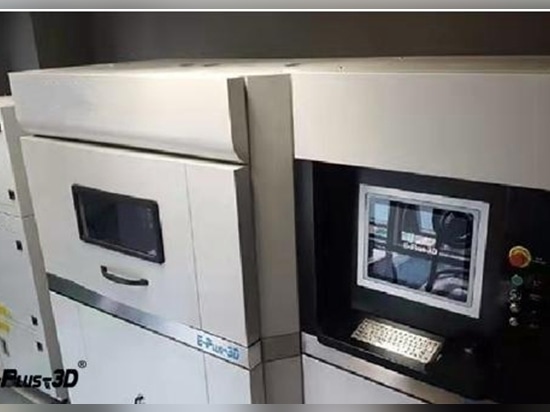
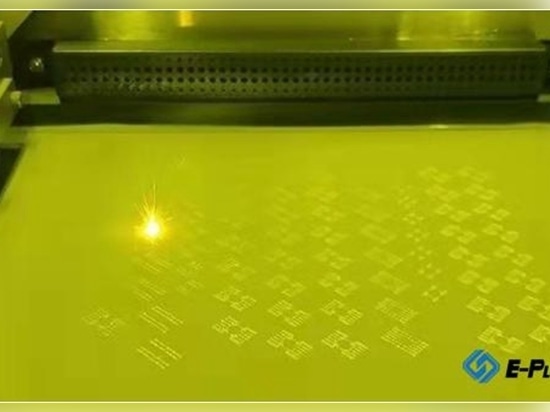
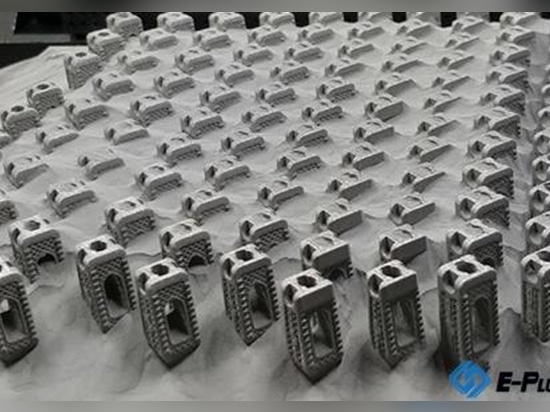
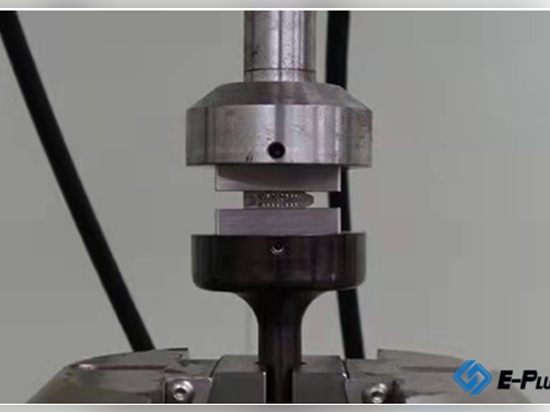
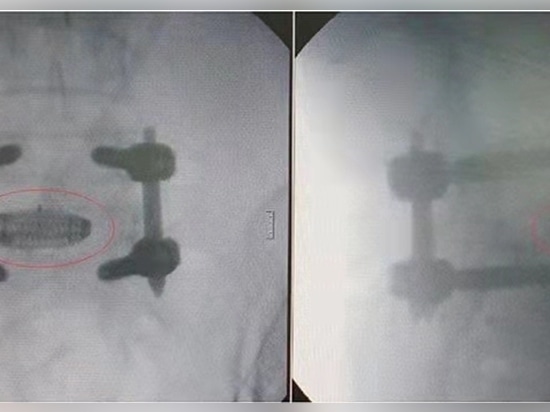
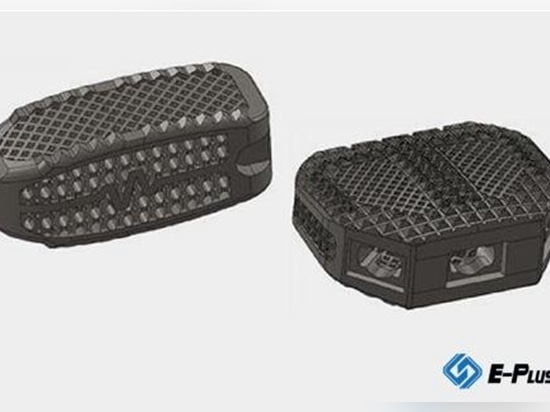