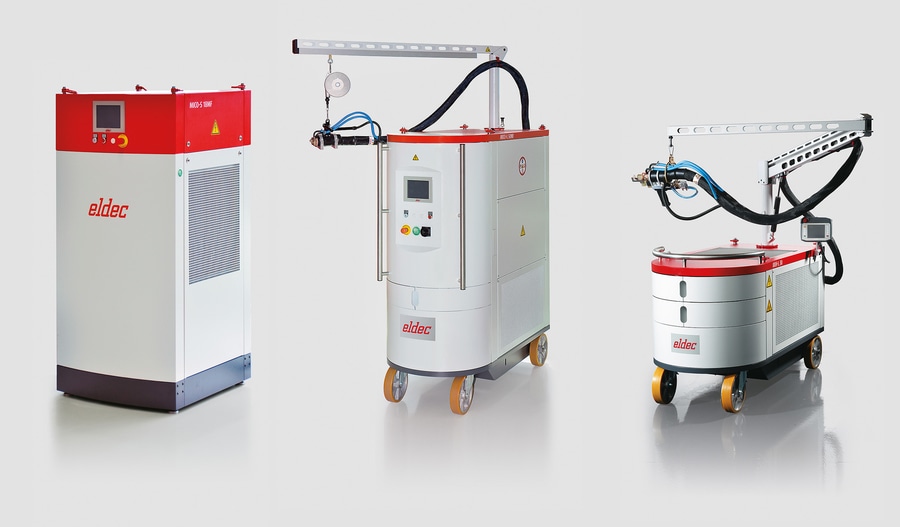
Voir la traduction automatique
Ceci est une traduction automatique. Pour voir le texte original en anglais cliquez ici
#Tendances produits
Générateurs de MICO d'eldec
Pleine dureté et processus courts pour l'outil et le moule faisant l'industrie
L'outil et le moule faisant des professionnels relèvent par habitude beaucoup de défis uniques à leur industrie. Afin d'assurer la stabilité des outils produits, des catégories très dures de l'acier sont exigées, cependant, les spécialistes doivent également pouvoir former avec précision ce matériel pour l'usage en créant les composants exigeants pour des choses telles que la fabrication de carrosserie. En d'autres termes, la qualité dans le processus toolmaking a un énorme impact sur la qualité à la fabrication d'automobile. Il est clair que dans ces conditions la dureté extérieure finale des outils soit essentielle, et le durcissement supplémentaire des tranchants est habituellement nécessaire. Les planificateurs de production chez Werkzeugbau Laichingen, dans Ulm, l'Allemagne, avaient compté sur la technologie de l'eldec : Leurs tranchants sont durcis par les générateurs mobiles et robustes de MICO. Cette technologie flexible de manière significative diminue et simplifie le processus de fabrication.
Les experts décrivent souvent toolmaking comme lien entre le développement et la production avec un impact considérable sur l'à valeur ajoutée industriel. C'est pourquoi l'industrie est considérée un avant-gardiste pour le développement continu des technologies de production que le ¬and est toujours à la recherche de nouvelles solutions pour améliorer des déroulements des opérations et la qualité. Le durcissement tranchant n'est aucune exception. Ce processus durcit les caractéristiques de l'outil que plus tard en refief doit soutenir la plus grande charge dans la machine le poinçon ou graver. La stabilité du tranchant est décisive en déterminant la durée de la vie d'outil.
Avantages du durcissement d'induction
Les outilleurs emploient généralement la bord-couche durcissant où la couche extérieure du tranchant est chauffée à environ 800 ou 900 degrés de Celsius (1,472-1,652 degrés Fahrenheit), selon le matériel. La « extinction », où la vraie transformation a lieu, puis se produit par le refroidissement naturel dans le ciel ambiant. En conséquence, la surface du bord est plus dure et plus résiliente pour porter (toolmaking typiquement exige une dureté de entre 54 et 56 HRC), alors que le noyau du matériel maintient sa dureté. Les diverses méthodes sont disponibles pour réaliser ces résultats. Les outilleurs utilisent principalement l'un ou l'autre de trempe au chalumeau, le laser très cher durcissant ou, alternativement, durcissement d'induction. Pourquoi est-ce que c'est ? « Pour commencer, toutes ces méthodes ont des applications flexibles. Même de grands, encombrants composants avec les géométries complexes peuvent être produits manuellement ou automatiquement quand utilisant des lasers », explique Stefan Tzschupke, chef des générateurs de développement des affaires à l'eldec. « Cependant, le durcissement d'induction offre des avantages significatifs en termes de qualité et temps de traitement, aussi bien que sécurité et coût. Notre technologie devient de plus en plus importante pour un nombre de plus en plus important des outilleurs. » Un examen rapide aux caractéristiques de la procédure d'eldec confirme cette évaluation. Le tranchant est chauffé par induction. De cette façon, l'outil atteint la température exigée beaucoup plus rapide, parce que la chaleur est fournie directement au volume sous la surface. Avec la flamme ou le laser durcissant, seulement la surface elle-même est chauffée au début. les sources d'énergie d'eldec permettent également pour commander avec précision la puissance, actuel, ou la température, permettant à des utilisateurs de répondre de façon optimale aux conditions spéciales aussi bien qu'aux conditions ambiantes du processus. En conséquence, le modèle durcissant est très uniforme. Un « autre avantage est que le processus ne produit d'aucun toxique ou les gaz explosifs qui pourraient souiller le lieu de travail », ajoute Tzschupke. « En conclusion, son bon rendement énergétique rend notre technologie beaucoup plus favorable à l'environnement que la trempe au chalumeau. »
Pour lire l'article complet, cliquez sur svp au lien.
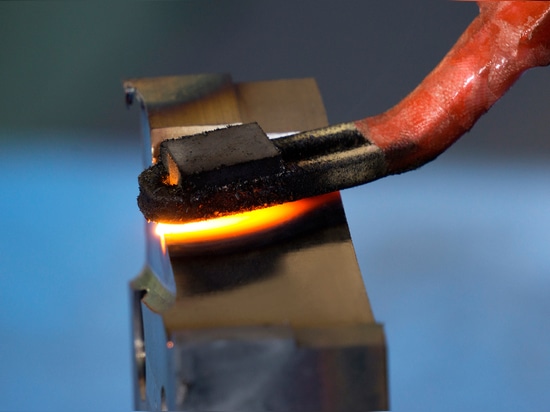
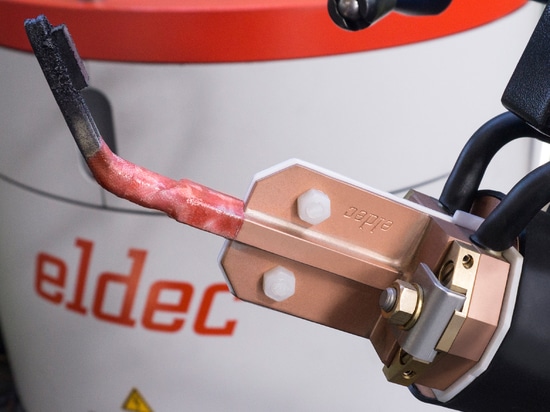
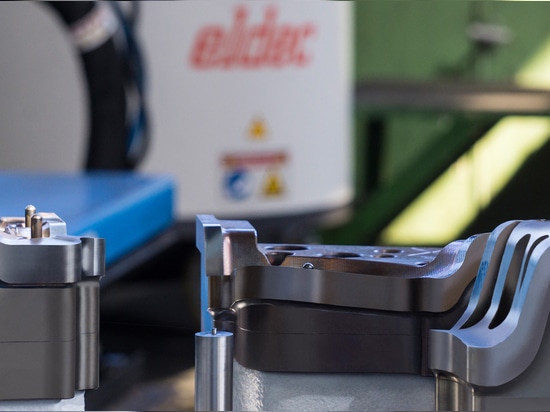
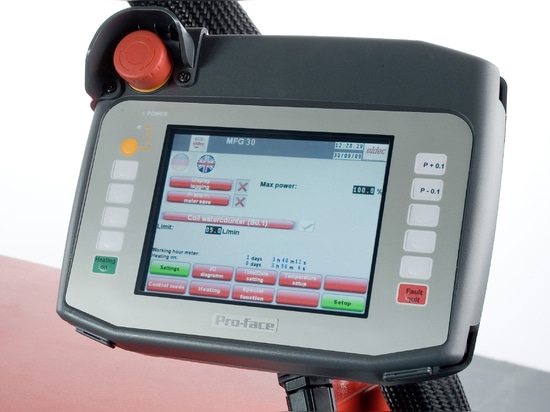