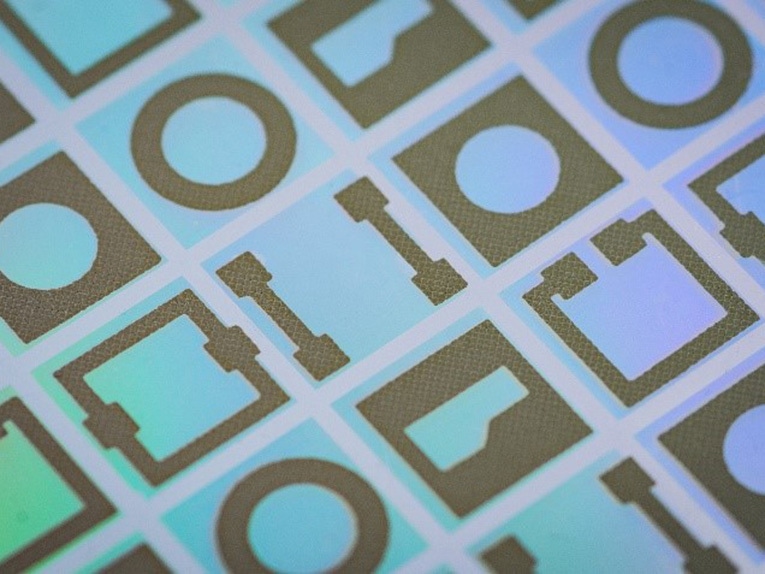
Voir la traduction automatique
Ceci est une traduction automatique. Pour voir le texte original en anglais cliquez ici
#Actualités du secteur
Production de micro-optiques moins coûteuse et plus simple
Grâce à la micro- et à la nano-optique, des systèmes optiques de plus en plus compacts sont créés. Ceux-ci ouvrent la voie à des fonctionnalités entièrement nouvelles qui ne peuvent être réalisées avec l'optique conventionnelle. Grâce à l'impression UV, la production de masse rentable de ces systèmes optiques est devenue une réalité.
Qu'est-ce que la micro-optique et où est-elle utilisée ?
En termes simples, les micro-optiques sont des versions miniaturisées des optiques conventionnelles. Les composants de cette dernière, tels que les lentilles, les miroirs ou les prismes, ne sont que quelques ordres de grandeur plus longs que la longueur d'onde de la lumière qui les traverse.
Les endoscopes médicaux sont une application où les avantages de la réduction de la taille des optiques deviennent particulièrement évidents. Ces dernières années, la micro-optique et les techniques de fabrication correspondantes ont permis de réduire l'ensemble du module optique (y compris le capteur d'image) à un cube dont la longueur des arêtes est inférieure à 1 mm (voir figure 1a).
Outre les dimensions réduites, la micro-optique permet également de concevoir des concepts nouveaux et améliorés pour des tâches optiques vieilles de plusieurs siècles, telles que les systèmes de projection. Au lieu d'utiliser des lentilles individuelles disposées l'une derrière l'autre pour créer une configuration encombrante pour la projection d'images, un réseau de microlentilles est utilisé pour paralléliser la projection. Cela permet d'obtenir un flux lumineux élevé pour une fraction de la taille des systèmes de projection conventionnels grâce à une longueur focale réduite (voir figure 1b).
Si la dimension est réduite de micro à nanoscopique, la méthode de guidage de la lumière passe de réfractive à diffractive. Cela ouvre une multitude de nouvelles possibilités. Par exemple, les éléments optiques diffractifs (DOE) peuvent être utilisés pour transformer un faisceau laser collimaté (droit) en pratiquement n'importe quelle distribution de lumière souhaitée. Un exemple notable est la création d'un motif de points utilisé dans la détection 3D pour mesurer la largeur, la hauteur et la profondeur d'un objet (voir figure 1c).
Comment fonctionne le processus de fabrication ?
Ce nouveau type d'optique nécessite naturellement de nouvelles méthodes de fabrication. Les méthodes conventionnelles, telles que le moulage par injection, sont moins adaptées en raison de la taille des structures et de la précision de l'alignement qu'elles requièrent.
Le processus de micro/nano-impression UV est désormais un outil établi, facilement disponible sur les machines standard proposées par plusieurs fabricants. Un matériau liquide et transparent, durcissant aux UV, est appliqué sur une plaquette de verre, puis mis en contact avec un tampon structuré. Une fois que la géométrie de l'optique, telle que les lentilles et les DOE, a été définie par le tampon, le matériau est durci par la lumière UV. Le tampon est ensuite retiré et la plaquette structurée est découpée en modules individuels (voir figure 2).
Intégration des ouvertures en tant que couche fonctionnelle
Les choses se compliquent légèrement lorsqu'il s'agit d'intégrer des caractéristiques supplémentaires dans un élément optique. Les ouvertures, par exemple, sont des éléments clés dans de nombreuses conceptions optiques.
Jusqu'à présent, les ouvertures étaient intégrées de manière standard dans les optiques imprimées à l'aide d'un processus photolithographique. Ce procédé consiste à créer d'abord une couche de chrome structurée sur une plaquette de verre, puis à imprimer l'optique directement sur la plaquette.
Le processus photolithographique comporte un grand nombre d'étapes :
- Revêtement d'une plaquette de verre avec une couche de chrome homogène
- Dépôt d'une résine photosensible
- Structuration de la résine photosensible à l'aide d'une étape de lithographie
- Développement chimique de la résine photosensible
- Élimination d'une partie de la couche de chrome
- Élimination de la résine photosensible restante
Inconvénients de cette solution :
- Ce procédé est très complexe et donc coûteux.
- Il limite également fortement les applications possibles de ces ouvertures. Ce procédé ne fonctionne que sur des plaquettes de verre et n'est généralement pas compatible avec la structuration d'une couche de chrome sur l'optique polymère elle-même.
- D'autres problèmes peuvent survenir en raison d'une adhérence insuffisante de la couche de chrome au verre ou du matériau polymère au chrome.
Nouvelle approche 1 : incorporation directe d'un matériau fonctionnel dans l'optique
Bon nombre des problèmes susmentionnés peuvent être évités en incorporant un matériau fonctionnel (noir, par exemple) directement dans l'optique polymère. Une façon d'y parvenir est d'imprimer des structures de canaux définies en plus de la structure optique pendant le processus d'impression. Ces canaux peuvent ensuite être remplis d'un matériau noir à faible viscosité qui est durci soit par la lumière UV, soit par la chaleur (voir figure 3). Cela simplifie énormément le processus.
Un autre avantage de cette option est que les propriétés thermomécaniques des deux matériaux (optiquement transparent et noir) sont beaucoup plus proches l'une de l'autre que celles du verre, du chrome et du polymère. Cela permet d'éviter les contraintes thermiques causées par des différences de coefficient de dilatation thermique (CTE). La fiabilité s'en trouve directement améliorée, comme l'ont montré les essais de cyclage en température. Comme cette méthode ne nécessite plus de substrats en verre, le poids et la hauteur de l'optique sont effectivement minimisés et les coûts sont réduits en même temps.
Nouvelle approche 2 : utilisation d'un support temporaire
Une autre approche possible consiste à commencer par un support temporaire (par exemple, une feuille de plastique). Les ouvertures sont produites sur le support par sérigraphie d'un polymère bloquant la lumière. Après durcissement du polymère aux UV ou à la chaleur, on procède à l'impression standard aux UV, où les structures optiques peuvent être alignées avec précision sur les ouvertures. Une fois que le matériau transparent a durci et que le tampon a été retiré, la feuille de support peut être décollée. Le résultat est un module optique entièrement monolithique (tout polymère) avec des ouvertures intégrées (voir figure 4).
Les deux nouvelles approches ont un avantage commun : les propriétés des matériaux noirs peuvent être adaptées à l'une ou l'autre conception optique et à ses processus respectifs :
- Exemple 1 : un matériau sérigraphiable avec une viscosité modérée et un coefficient d'absorption élevé pour une densité optique élevée dans des couches minces de quelques µm.
- Exemple 2 : un matériau destiné à remplir des structures fonctionnelles avec une faible viscosité et un coefficient d'absorption modéré pour une densité optique élevée dans des structures de quelques 100 µm.
- Il est même possible d'incorporer une fonction de filtre spectral directement dans le polymère (par exemple, bloquer une certaine gamme de longueurs d'onde tout en permettant la transmission dans une autre gamme de longueurs d'onde).
Intégration de couches fonctionnelles et conductrices d'électricité
Certaines applications nécessitent l'intégration de structures conductrices d'électricité dans l'élément optique. Un exemple est l'élément diffuseur utilisé dans les capteurs à temps de vol ou pour les capteurs de lumière structurée qui forment le faisceau laser collimaté de l'émetteur. Dans ce cas, les structures conductrices sont utilisées comme un filet de sécurité pour détecter d'éventuels dommages à l'élément diffuseur, évitant ainsi toute menace provenant du faisceau laser émis. Un processus similaire à celui utilisé pour les ouvertures peut être utilisé pour produire un tel filet de sécurité. Toutefois, un adhésif isotrope conducteur d'électricité (ICA) est utilisé à la place d'un polymère noir.
Tout d'abord, un ICA (par exemple DELO DUALBOND IC343) est sérigraphié sur une feuille de support temporaire contenant diverses structures (par exemple des pistes conductrices, des ouvertures). Un matériau transparent durcissant aux UV (par exemple DELO KATIOBOND OM614) est ensuite utilisé pour imprimer une nanostructure sur cette feuille, qui forme l'élément optique diffractif. En retirant la feuille de support, on obtient une plaquette de polymère complète avec plusieurs DOE et une structure conductrice intégrée (voir figure 6).
Conclusion
Ce procédé impressionne par sa simplicité et sa rentabilité :
- Des procédés simples d'impression UV peuvent être utilisés pour produire des éléments optiques miniaturisés tels que des lentilles ou des DOE avec des fonctionnalités supplémentaires (par exemple des conducteurs électriques ou des ouvertures noires).
- Seuls deux matériaux sont nécessaires à cet effet : Un matériau transparent durcissant aux UV pour l'optique principale et un matériau chargé durcissant aux UV ou à la chaleur qui fournit la conductivité électrique ou la propriété de protection contre la lumière.
- Cette approche permet également de surmonter les problèmes de fiabilité potentiels (par exemple, le décalage thermique), car les propriétés thermomécaniques des deux matériaux peuvent être adaptées.
Chez DELO, vous trouverez un vaste portefeuille de produits de ce type. Nous vous aiderons à trouver une solution adaptée aux exigences spécifiques de votre application.